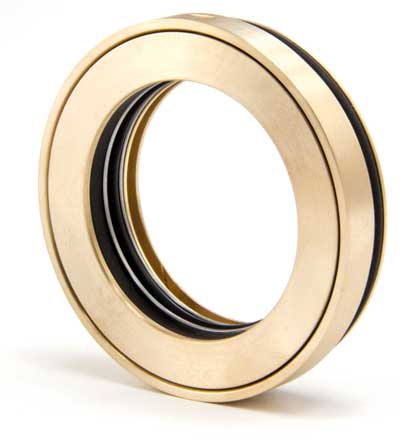
With advanced retrofittable bearing protector seals readily available on the market, pump bearing failure should be the exception not the norm, says Dr Chris Carmody, special products manager of AESSEAL.
Bearing failures account for roughly 40% of all pump and rotating equipment malfunctions, so routine downtime for maintenance and repair is a common occurrence in countless industries.
More than half those bearing failures are the result of contamination of the lubrication oil by particles of dust and dirt, or corrosion caused by ingress of water or other process fluids, according to Pump Users Handbook: Life Extension by Heinz Bloch (2011). And at the root of these failures are outdated sealing products such as the traditional lip seal.
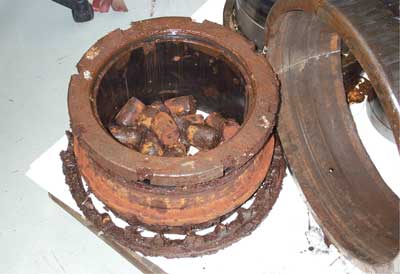
Surface contact with the rotating shaft means lip seals start to deteriorate almost immediately after installation, allowing particles and fluids into the bearing chamber, contaminating the lubrication oil and causing corrosion. The ingress of moisture or particles into the bearing chamber might be minute, but the impact on efficient operations can be significant.
For example, research indicates that water contamination as low as 0.002% – that’s just a single drop of water in a typical bearing chamber – can reduce bearing life in some oils by as much as 48%. An oil-lubricated 45mm radial bearing running at constant load and speed under ultra-clean conditions (contamination factor ŋc = 1) has been calculated to complete 15,250 operating hours. Introduce severely contaminated conditions where ŋc = 0.02 and its operational life plummets to just 287 hours – a dramatic decrease in mean time between failures.
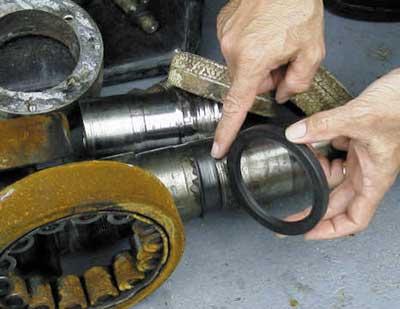
In the worst case, the shaft or shaft sleeve can also become worn and damaged, requiring expensive repair or replacement.
It’s no secret among maintenance teams that inefficient seals are a prime cause of bearing failure and that modern bearing protector seals are readily available which can be retrofitted. So why do companies with an otherwise exemplary approach to operational efficiency persist in using outdated technology?
The answer is often as mundane as it is illogical. The seals were specified with the equipment – which may now be decades old – and have been failing regularly for so long that it’s become routine simply to pick a replacement lip seal off the shelf in the effort to get operations running again as swiftly as possible.
Advanced bearing protector seals have been developed which employ magnetically energised seal faces (the faces are made from antimony carbon and tungsten carbide rather than elastomers) and labyrinth seal technology to eliminate the external contamination and loss of lubrication which account for 52% of bearing failures. Labyrinth seals provide a complex path against leakage and work dynamically, relying on a close but non-contacting fit with the rotating shaft.
If bearing seals are to work to optimum efficiency they must facilitate the “breathing cycle” required by rotating equipment, allowing the oil/air mixture to move through the bearing seal when it heats and expands with the rotating equipment, and then sucking it back into the bearing housing as it cools. In conventional seals this process allows dust particles and moisture to be sucked in at the same time.
AESSEAL recently launched the MagTecta-S, which combines the best of existing MagTecta and LabTecta technology to offer a cost-effective reliability upgrade. These incorporate “dynamic lift technology” to facilitate the breathing cycle while preventing the ingress of contaminating dust and moisture. This exploits the centrifugal motion induced by the rotating equipment to open a temporary micro-gap, allowing expansion of the oil/air mixture in the bearing housing and allowing the equipment to “breathe”. When the equipment stops rotating the micro-gap immediately closes, forming a perfect seal against potential contaminants.
The seal they provide significantly improves operational efficiency and justifies investment in more effective synthetic lubricants.
Crucially, though many lip seals are machined integrally into the bearing plate by the original manufacturer, particularly in older equipment, advanced bearing protector seals can be retrofitted on to shafts. Once fitted, they require minimal maintenance and will provide protection until the bearings reach the end of their natural life.
While lip seals are the weakest link in the operation and maintenance of rotating equipment, labyrinth bearing protector seals can form the bedrock for significant efficiency gains and cost savings.