Oil condition sensing can complement vibration monitoring, enhancing the effectiveness of a predictive maintenance programme and detection of the main failure modes. Gill Sensors & Controls product manager Simon Foulser explains
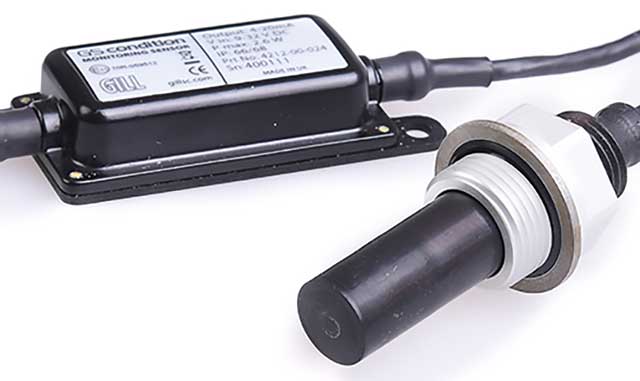
Improved productivity is a continuous demand on any business and there are many ways to achieve it. In manufacturing, maximising machinery availability is a key element.
Predictive maintenance determines when maintenance needs to be carried out, based on the condition of the machine. There are five root causes of machine failure – balance, alignment, looseness, lubricant quality and contamination. Providing insight into when any one of these conditions is developing can be achieved through vibration or oil condition monitoring.
Vibration monitoring is the most common technique, because most of the conditions described above will generate some form of vibration. The sensors are usually small and easy to mount without having to stop the machine.
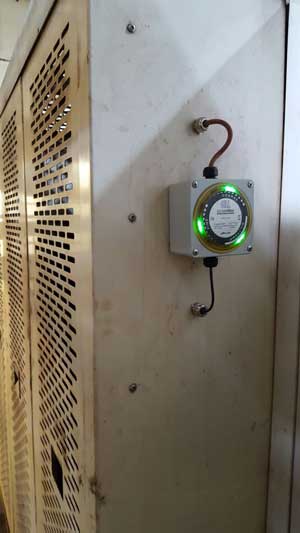
Operating continuously they can transmit data wirelessly to a datalogger or remote screen. Handheld units are also available but limited to where an operator has access.
The vibration signal is derived from many components and vibration monitoring requires a thorough understanding of the frequency response of all components. This requires a skilled operator to determine what “normal” vibrations are, what indicates a change in condition and what level of abnormal vibrations should signal an alert. Systems can filter the data, but require a trained operator to configure them.
A typical motor/gearbox assembly could require four sensors: two on the motor, at the drive and non-drive ends, and on the gearbox input and output shafts.
Oil condition monitoring sensors are now available, generally measuring a single parameter and providing continual, real-time analysis. For the five root causes, particle detection will provide the insight required, either with magnetic ferrous debris sensors or particle counters.
Oil condition and vibration provide considerable insight about machinery health. However, independently they are unable to provide complete coverage of the five root causes.
If an electric motor has a problem with a shaft bearing, vibration monitoring will provide indication of a problem. However, if a gearbox bearing is failing, it will deposit debris in the oil before a measureable increase in vibration occurs.
Some studies estimate oil condition monitoring provides up to 10 times earlier warning than vibration monitoring. Oil condition has advantages in low-speed machinery (below 5 rpm), where the amplitude of the vibration signal might not be strong enough to overcome the noise factor.
Oil monitoring will provide early warning of component breakdown, but gearboxes have several bearings, so it will not pinpoint where the problem is. Vibration monitoring will assist this.
Palo Verde Nuclear Generating Station combined vibration and oil condition monitoring into a common working group. In an assessment of detection of bearing defects, oil condition was responsible for detecting 40%, vibration for 33%, and both techniques converged on the remaining 27%. The loss of either technology reduced detection performance and control of root causes of failure.
Understanding the root cause of failure provides an additional insight into preventing breakdowns. Combining primary and secondary detection provides more data, enabling deeper understanding of failures. This informs changes in maintenance, operation or design, permanently eliminating causes of breakdown.
Real-time sensors for oil condition monitoring make this combination practical and affordable. They complement vibration sensors for continuous measurement with outputs that can be accessed locally or remotely.
Gear tooth wear and fracture are common failure modes. Using vibration analysis to detect gear wear is difficult because of the number of vibration signals. Oil condition monitoring provides early indications of contact fatigue, abrasion and adhesive wear.
However, breakage of a gear tooth is unlikely to produce a detectable quantity of wear particles, especially when caused by a sudden impact or material defect. Monitoring gear mesh frequency using vibration analysis will pinpoint a broken gear tooth virtually every time.
By combining oil condition and vibration monitoring, a number of benefits compared with conventional condition monitoring practices can be realised. These include accurate, efficient and early fault detection as well as performing root cause analysis.
info@gillsc.com | www.gillsc.com
+44 (0)1590 613900