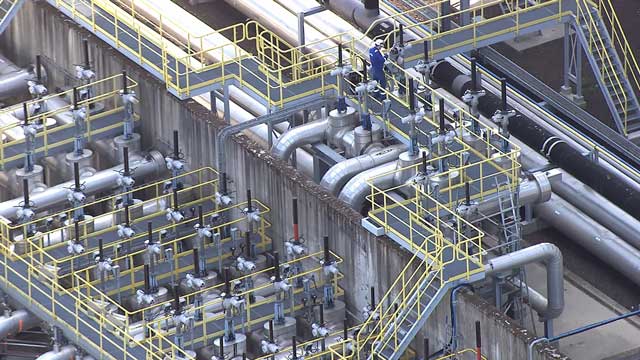
A intelligent asset management system currently under trial will analyse information from valve actuator dataloggers, and relay it to operators to allow accurate prediction of maintenance and repair work, says Liam Jones of Rotork.
Intelligent asset management technology could save operators costly site downtime, while providing the opportunity to gain greater in-depth knowledge of the condition and status of their actuators and valves.
The asset management principle is based on the industrial internet of things (IIoT) technology, using devices embedded with sensors, electronics and software to allow them to collect and exchange data.
However, the technology is not about the devices themselves: it is about the data they produce and store which allows smart, quick decisions to be made, saving money and time as well as increasing safety and improving performance.
A real-life example of data not being fully used is a smart meter. It knows how often a tap or shower is used and can also detect a leak. However, if someone left home in the morning leaving a tap running, there is no way for the meter to relay that information or stop the leak. In future, internet of things technology will be used to stop the leak happening.
IIoT’s greatest value lies in improving asset management. Rotork’s technology provides a way of completing that link by analysing, acting and making recommendations based on the data. Data can be collected from the field by a service engineer using a tablet or uploaded directly to the cloud and displayed online.
Rotork’s system for intelligently managing assets, currently being trialled, can analyse the wealth of information gathered via a valve actuator’s datalogger and relay it to the user in a clear, user-friendly way
Actuators are able to monitor and feed back valve information such as valve position (open/closed), and monitor faults. On-board sensors process and log information such as torque level, status, vibration and temperature.
The system provides operators with the ability to manage risks and get a better understanding of assets by constantly monitoring actuator status. This information enables the plant operator to accurately predict maintenance work and repair, to minimise downtime, save money and improve safety, efficiency and reliability.
Although additional pipework routes through which gas or fluids can be directed, known as redundancies, can be used to reduce downtime, companies can lose substantial amounts of money if a site is out of action for a period of time.
The biggest benefit from using asset management technology is the increased uptime, because potential issues can be predicted. This means they can be quickly rectified before they turn into a more serious problem or cause a shutdown. An unplanned plant shutdown can be very costly and can sometimes result in added risks to the environment or safety.
Plant operators are wirelessly connecting their sites to internet-based services at a rapidly increasing rate, with some companies claiming they see wireless communication soon becoming more secure than wired. These days, wireless protocols offer high levels of security compared with the limited protection offered by legacy wired protocols.
Recognition of the benefits of implementing IIoT technology is growing and being viewed as an efficient and secure way of managing assets at both small and large sites. With the ability to access in-depth data through cloud-based technology as a way of scheduling maintenance and predicting potential actuator problems, plant operators can significantly reduce downtime.
Rotork is introducing its own system for intelligently managing assets and is carrying out trials with a select number of customers in a limited scope environment. For parties interested in this system, Rotork is happy to discuss a limited scope implementation.