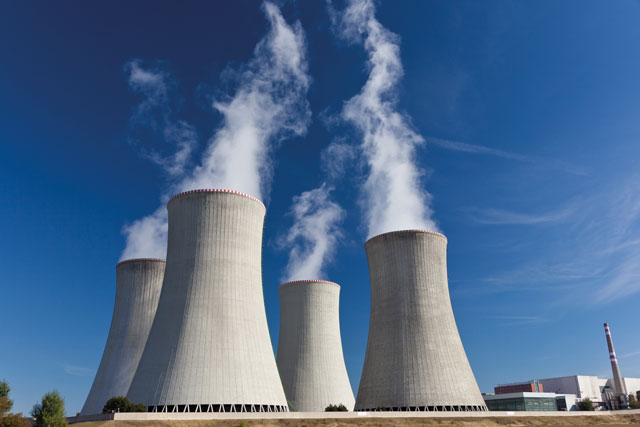
Abstract
By the very nature of their action, cooling systems may suffer considerable levels of system contamination. This can be caused by suspended solids in the make-up water, the “scrubbing” action, of cooling towers, or by process leaks encouraging microbial activity. Having instituted extensive chemical treatments, many owners and operators believe they are operating an effective and safe water system. But how safe are they really?
John Wilson, sales manager UK & Ireland of Amiad Water Systems UK, discusses some of the hidden truths.
Introduction
The key purpose of any cooling tower or system is to remove heat from some part of a process, and the methods used to accomplish this are wide and varied. Many cooling systems rely on water as part of the heat removal process. While being an effective medium for heat transfer, when used in cooling systems water can lead to a number of hidden problems, because the cooling process effectively drags contaminants into the water.
If this contamination is not removed from the system it will provide the substrate for microbial activity to develop. Once established, removal and treatment can be problematic, which is why keeping a clean system in the first place is much more desirable.
Plant performance can be reduced because of the reduction of heat transfer efficiency through contaminants collecting in the water. Effective removal of these particles can boost efficiency and therefore performance.
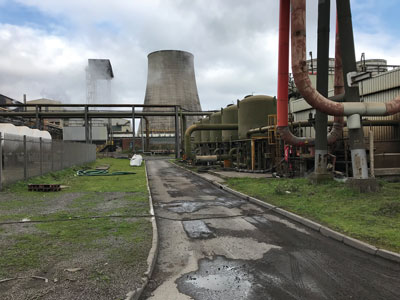
The contamination in the water is a combination of biomass and mineral scale, both of which will become attached to the inner heat transfer surfaces of the system. This will in turn reduce the heat transfer efficiency, at the same time creating an irregular surface for other contamination to build on, further reducing the overall system efficiency.
A biofilm of less than 150 micron will reduce efficiency significantly, but this can continually build, and often gets completely out of control. This can lead to pipework that is severely reduced in diameter, or, in extreme cases, totally blocked. In these situations drastic action is often required, such as a thorough clean-out using expensive acid flushing, or the system may need to be completely replaced. High levels of bio-fouling inhibit the ability of chemicals to do their work, further exacerbating the problem.
Legionella pneumophilia and related bacteria occur naturally in many water sources and if present in a cooling system which recirculates the water can multiply if the conditions become favourable. Legionella bacteria can cause serious health problems and diseases, collectively known as Legionellosis.
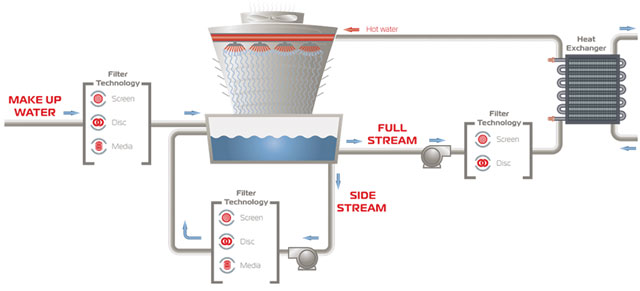
The cooling industry is widely regulated to help prevent these potentially harmful bacteria being given the opportunity to develop. A chemical treatment regime is commonly instituted to reduce the levels of bacteria to a suitable level.
The general guidance is that a chemical treatment regime must be combined with adequate monitoring, and that the treatment programme must provide control of four key elements that can affect any cooling water system: scale, corrosion, biological fouling and suspended solids.
Generally water treatment chemicals together with some form of pre-treatment will adequately control scale, corrosion and biological fouling. But what about suspended solids control? The potential for suspended solids to increase is always present. Suspended solids contamination can come from many sources, such as windblown dust and other airborne contaminants, pipework corrosion, system contamination from process, changes in raw water make-up or other local issues.
With operators seeking to employ what they believe to be a quick fix, operators regularly focus on just one aspect of the water treatment regime. Little do they realise that this could in fact make the situation worse, as is pointed out by the Health & Safety Executive’s (HSE) advice:
“An appropriate cooling water treatment programme must be capable of controlling not only legionella and other microbial activity, but also corrosion, scale formation and fouling, and include appropriate measures, such as regular physical cleaning and disinfection, to maintain the system’s cleanliness. This is very important since these aspects are often interrelated and failure to control one aspect will often lead to other problems and will increase the legionella risk.”
In reality, it is common to see cooling system installations that have focused on compliance, with operators using extensive chemical treatments in the belief that this will ensure they do not fail microbiological tests. Conventional chemical techniques employed may involve adding inhibitors to control corrosion and scale formation, biocides to control microbial growth and dispersants to control fouling. These measures alone will not necessarily result in an efficient cooling system if the water is heavily contaminated with solids.
This can lead to the issues of poor energy transfer, blockages and system shutdowns mentioned above that result from poor quality cooling water being circulated. The consequences of having to shut down and rectify the problem can have a significant impact on the operational costs for that particular site.
Often the problems associated with poor heat transfer develop over time and operators miss the indicators that point towards a highly inefficient system. What starts as a small change, such as increasing the recirculation pumps to compensate for the lower heat transfer, can end eventually with a system so heavily contaminated and inefficient that it requires intervention to resolve.
Formation of biofilm
Generally, 80-90% of the particles in a cooling system are less than 10 micron in size and it is these particles which lead to most of the problems.
In most systems the process cooling water is passed through a system of pipework and, if a cooling tower is present, it is passed over the cooling area of the tower, or through a chiller or heater.
The pipework will normally be plastic, steel, stainless or, in many systems, a combination of all three. The surfaces of these materials are microscopically rough. This allows small particles, typically less than 5-6 micron, to attach themselves to the surfaces of the pipework and cooling system. Some may be killed off by chemicals but they still hold their position, often building up to give a smooth internal pipe surface. This is called biofilm, something with which any operator will familiar.
Underneath the biofilm the pipe surface remains colonised with live bacteria, protected from chemicals, kept warm and fed on a continuous basis.
Biofilms will ultimately provide an environment where water treatment chemicals cannot function and can enable huge numbers of different bacteria species to proliferate. A mature biofilm will be a very complex structure containing both aerobic and anaerobic bacteria together with protozoa. The inclusion of protozoa is a major factor in the ultimate colonisation of a system by Legionella bacteria.
Where biofilm has formed, major problems with plant and equipment as well as the stability of the cooling can be expected, and there is increased risk of breaching health and safety laws.
Effective and reliable side-stream filtration can remove these smaller elements and minimise their contamination of the system.
Side-stream filtration
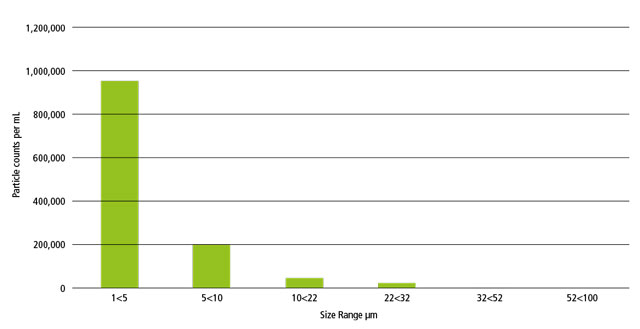
A common practice to improve the performance of the total water treatment programme is the inclusion of side-stream filtration, whereby a volume of recirculating cooling water is passed through a side-stream loop to reduce overall loading of solids. Typically these use kinetic or centrifugal separators, or other technology such as self-cleaning screen filters, disc filters or even conventional media filters. As a standard practice such systems are then combined with chemical treatment. These technologies filter to a limit of at best around 15-20 micron, and in tests typically show a solids loading of anywhere from 10 mg/l to 80 mg/l of physical matter (some even more if the make-up water is not mains water – for example, abstracted from a borehole, river or lagoon).
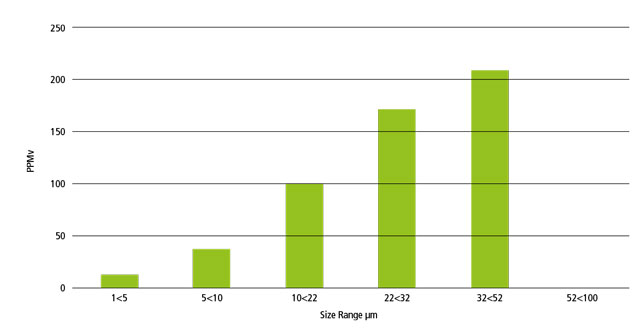
In reality, the majority of medium or small systems tend not to have any filtration, either side-stream or otherwise. Those that employ filtration tend to be larger systems or those with problematic units where, commonly, filtration is retrofitted once fouling has become established.
Nevertheless, the operational benefits of effective filtration in cooling water are very significant, not only contributing to good microbiological maintenance but also to maximise heat exchange efficiency and reducing maintenance costs.
Fitting side-stream filtration will dramatically improve overall performance and allow the chemicals to work more effectively.
However, the implications of what is contained in the cooling water must be thoroughly understood before a correct side-stream filtration solution can be implemented.
Analysis
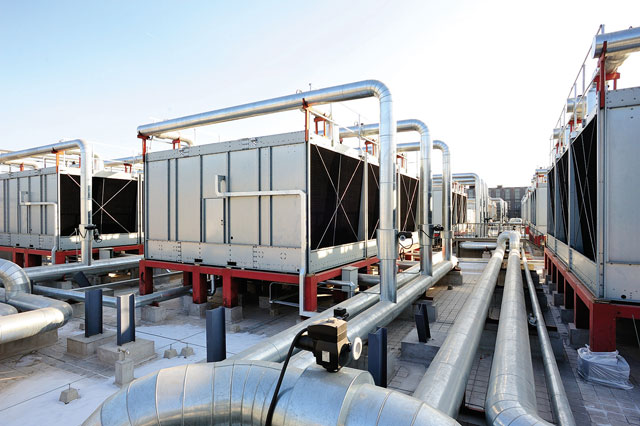
Meaningful water analysis is essential. It is quite common for operators to occasionally do a total suspended solids (TSS) test but this only reveals how much solid particulate material there is in the water. It is necessary to determine the distribution of particle sizes and volumes present through a particle size distribution (PSD) test.
A PSD will commonly show that a considerable proportion of the solid particles are very small and as low as 1 micron in size. It is not just particle size that matters but the volume of the particles. For example, the particle count for <5 micron particles might be very high but particles of this size might only represent a small fraction of the volume. The graphs on this page illustrate an example where almost 95% of the particles are below 10 micron in size, but they account for less than 10% of the particle volume.
If a 10 micron filter was operating at a 95% removal efficiency, though the volume of particles above 10micron in size would be reduced significantly, this would only translate to a reduction in total suspended solids if the water contained a reasonable number of particles above 10 micron in size. If most of the particles are below 10 micron then there will be a limited change in TSS. The important point is to try and characterise the water so that you can understand how it will interact with a given type and size of filter.
The remaining small particles will cycle round the cooling system, building up over time and causing problems through their accumulation. As a result it is necessary to consider the cost-effectiveness of removing them.
Choice of side-stream filtration system
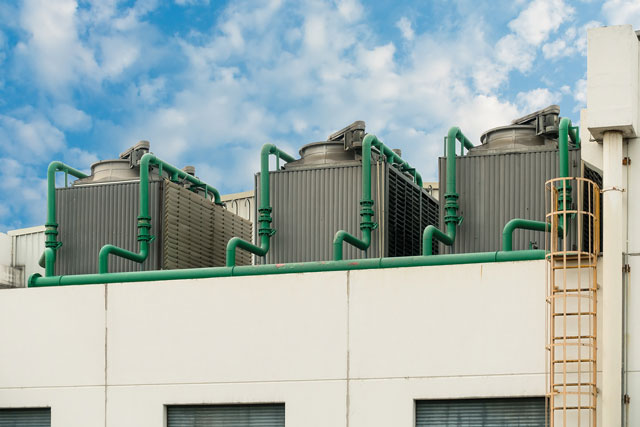
Effective side-stream filtration should be based on selecting the most appropriate technology for the application and making sure that it can effectively remove the type of solids in the water. There is a wide choice of technology from which to choose with each type having its own distinct pros and cons.
Consideration should be given to how clean and efficient the cooling system needs to be. For example, an intermittent cooling requirement for a seasonal operator will have a completely different set of requirements from a site operating 24 hours a day all year round, which cannot be shut down.
Here is a short list to consider when choosing side-stream filtration and the options available:
• What is the nature of the particles? Organic or inorganic? Understanding the origins of the water will generally indicate whether the particles are likely to be organic or inorganic.
• What level of filtration is really needed? In some situations the finer particles will build up but can be periodically flushed from the system as part of the blowdown process, which is the flushing of a portion of the concentrated cooling system water and replacing it with fresh make-up water. However, if operating a closed loop system, flushing or increasing the blowdown will be less desirable. In this case, removing the finer particles will be necessary to maintain the efficiency of the system. There will be a trade-off between how clean to run the system and what is deemed an acceptable level of fouling, which will often be influenced by how critical it is to maintain the cooling, and the cost and life of the cooling equipment itself.
• How much space is available? Would a screen filter which requires a smaller footprint than a media filter be effective with the type of solids particles?
• Is the site sensitive to water losses? Sites with tight abstraction/discharge limits may not be able to afford water losses.
• Do you need uninterrupted filtration? Operators running 24/7 whose systems are not shut down regularly will have different requirements from a site that is operating day shifts, five days a week.
• What would be the cost of maintenance and the impact on operation? Ease of maintenance might be a key consideration if working in a geographically remote location such as an offshore platform.
The table below summarises the key attributes of various filtration options available and how they perform in different applications.
Conclusion
In conclusion, there needs to be a better understanding of the implications of a “quick fix” approach to cooling tower and cooling water filtration. Operators may feel they have achieved biological control, but biofilm in the pipework, unless thoroughly treated, can unexpectedly appear and cause major problems, not just to a process but, more seriously, to public health.
The best and most efficient side-stream filtration system is the one that provides the best possible return on investment by improving plant efficiency, reducing both operational and maintenance costs and, most importantly, meeting HSE requirements.
Amiad Water Systems UK is able to offer both an informed opinion but also an unbiased view of the filtration technologies available. With over 50 years experience in the field of water filtration it can help guide your towards the solution that is both cost-effective and maximises the efficiency of your cooling system.
For further information visit www.amiad.com