When selecting an engineering training course provider, a range of factors should be considered to make sure that employees return to work as competent, empowered individuals, says Technical Training Solutions director Martin Smith
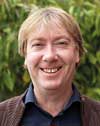
In many industry sectors, business success and continued growth is being hampered by skills shortages or by companies not investing in relevant training for their employees.
In spite of this, most nationally recognised, accredited engineering training courses tend to take a broad brush approach to course content, with very little relevant practical assessment to gauge whether the delegates are competent at the end of the course. There is often a disconnection between what is taught and what the delegates are actually doing on a day-to-day basis in the workplace.
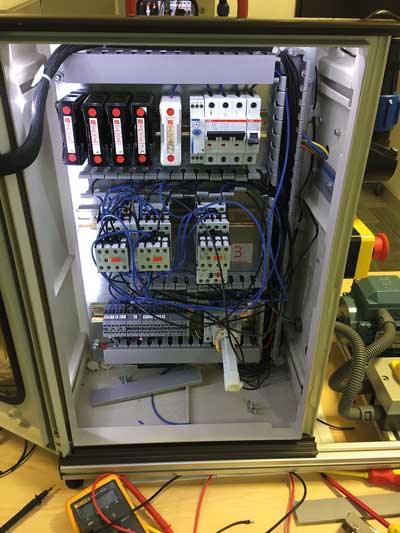
A certificate of competence or attendance?
Many employers feel that a training certificate simply represents a “proof of attendance” and is no guarantee of competence. Employers should look for a training provider that focuses on the practical side of training, which runs in parallel with the theory. This will encourage interaction with practical training rigs and a learning by doing approach.
The objective is to improve the delegates’ knowledge and understanding, which will lead to competence in that discipline. Courses should not produce “robots” who have been taught about theory only – they need to understand the subject matter, and why they are being asked to do things in a certain way.
Keeping delegates’ attention on a training course doesn’t mean doing three days of theory followed by one day of practical sessions. The two should run in parallel with lots of crossover; they should be intrinsically linked. Delegates should be assessed during and at the end of the course to check for competence. This shouldn’t just be a multiple choice assessment – the focus of assessment should be on the practical exercises, ideally on special purpose training rigs designed for that course.
“Death by PowerPoint” should be avoided at all costs as delegates don’t want to listen to long lectures. Each subject should be presented in its most straightforward context so that candidates can explore the essential issues and engage with the learning experience intended.
For example, if candidates are learning about isolating three-phase motors, specially-wound 40V three-phase motors should be provided for them so that they can connect the motor control gear and demonstrate that they can individually isolate the motors in a range of scenarios.
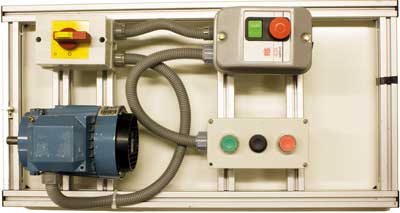
Taking ownership of machines
Production downtime in the process industries – food and beverage processing, metal processing, chemicals and pharmaceuticals – can be extremely costly, so employers need to train their production operators to take more responsibility for machines, including their maintenance and availability.
Employers should make their staff feel more motivated by providing the appropriate training that allows these individuals to feel more valued, improving their confidence and decision-making. Upskilling operators should lead to improved productivity, reduced maintenance costs and increased machine uptime.
With this in mind, look for a training provider that offers training that encourages delegates to look at the equipment or machine in a different way when they return to work. This means the courses should be designed so that delegates are more likely to relate all the course content to their day jobs.
They will be able to apply the most up-to-date legislation and best practice when carrying out everyday activities at work, and they’ll have a much better understanding of why they are carrying out each of these tasks.
Training should be designed to empower staff by promoting ownership of their equipment, and encouraging them to look after their machines from the viewpoint of cleaning, maintenance and safety.
www.technicaltrainingsolutions.co.uk
tech.training@zen.co.uk | Tel: 01634 731 470