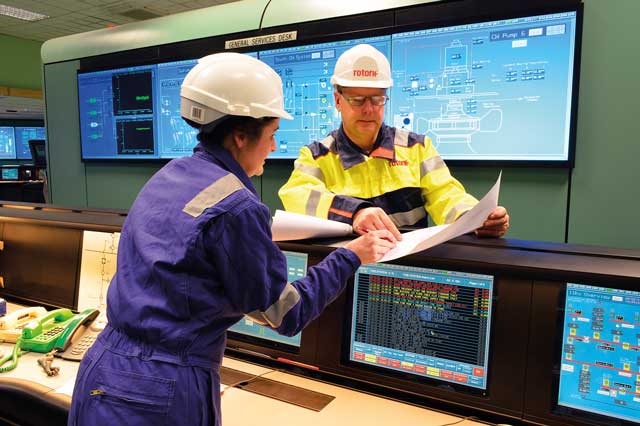
Lifetime management of actuators is essential for maintaining reliable, undisturbed operation on sites around the world. Dave Godfrey, Rotork product manager for service and aftermarket, describes how a four-tiered approach can provide clients with optimal levels of support.
Plant availability is a key element in the efficient running of modern processes. The reliability of the assets, such as actuators for valves, installed in a plant can contribute substantially to uptime.
Plant managers today demand access to more information, more quickly than ever before. Process operators must have the ability for full control, 24 hours a day.
Asset management is essential for maintaining reliable site operation and minimising costs. A maintenance strategy assists in understanding and managing the inherent risk that ageing equipment brings to plant and operational goals, and provides solutions to allow predictive and preventive maintenance to maximise the life of the plant.
A lifetime management programme will provide increased asset reliability, lower cost of ownership and greater plant uptime.
Actuator manufacturer Rotork believes that health checks, planned maintenance, enhanced warranty and predictive maintenance are the four most important things to consider when making plans for lifetime management.
Health checks
Plant operators have historically struggled with managing assets. Legacy IT systems, changes in recording or naming conventions and changes in priorities have all led to situations where they do not know what they have, and more importantly what condition it’s in. This is not limited to a single industry or sector but is a global issue.
The problem of not knowing is that you cannot plan, budget or resource appropriately. A health check can help to fill the gaps in the organisation’s knowledge. This is an assessment of actuator condition relative to design specification and operational use.
Planned maintenance
One of the challenges operators face is identifying the condition of their assets. A health check can help to provide an idea of how actuators are functioning; planned maintenance takes things a step further with thorough product inspections and active repair management.
This includes an intrusive inspection to confirm that equipment is within specification. The datalogger and configuration will be benchmarked, O-rings and batteries may be replaced and functional tests (manual, remote and local) will be carried out.
Enhanced warranty
For companies which use budgeting and cost management as key decision-making factors, enhanced warranty can be appropriate. Rotork works with clients to generate a cost-risk management framework, allowing asset planning to be optimised. Historical performance is reviewed through datalogger interrogation, and health checks are carried out at least twice a year.
Predictive maintenance
Predictive maintenance encompasses all previous tiers, helping to solve problems before they escalate and lead to costly unplanned downtime. Using machine learning, an archive of datalogger records is compared to identify trends and patterns which occur prior to failures. When these patterns are identified, maintenance can be carried out before a problem occurs, helping to maintain smooth operation as much as possible.
Lifetime management in action
The value of the lifetime management system was demonstrated in an application with a well-known chemical solutions company. There was a motor operated valve (MOV) in use on the customer’s site. Although the MOV was continuing to function without any signs of a fault, Rotork was able to predict that a problem might soon develop. This was found to be the case less than a month later when the valve failed. With the ability to foresee problems like this, a great deal of time and money can be saved.
This approach to aftercare creates a continuing relationship with the customer, which helps them to understand the risks associated with ageing equipment, while actively helping to avoid those risks and increasing site efficiency and productivity at the same time.
Dave.Godfrey@Rotork.com | +44 (0)1225 733515 | Rotork.com