Fork lift truck maker Combilift says productivity is running at around 90% after it reconfigured its operations to introduce Covid-19 safety measures. Meanwhile the emergency is helping to drive up interest in its products, said managing director Martin McCarthy.
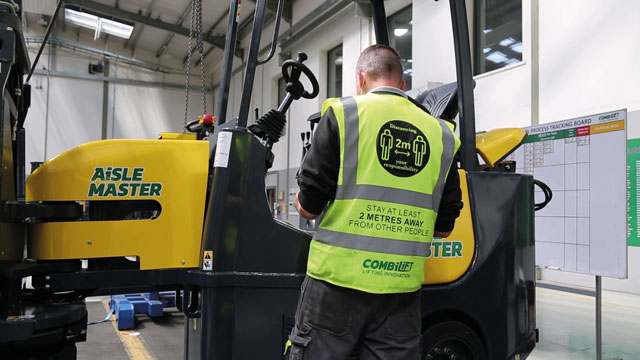
Combilift employs 600 workers at a €50m factory in Monaghan, Ireland, opened in 2018. When Ireland went into lockdown on 17 March, the company was classified as an essential business. But it decided to suspend production for three weeks to introduce additional safety measures and to give staff more confidence about returning to work.
The factory had always operated on a single-shift basis five days a week. On reopening, a two-shift system was introduced so that there are fewer people in the plant at any time. Mr McVicar acknowledged that the size of the plant, at 46,500 sq ft, made social distancing easier, but the canteen still presented difficulties. It has been closed, and eight individual canteens have been set up around the site, with staggered breaks. This arrangement also reflects how the site is organised, he added.
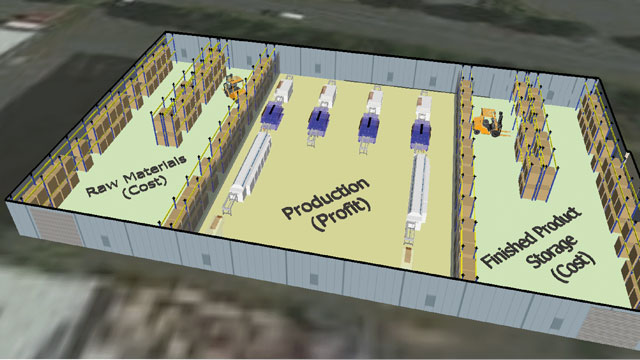
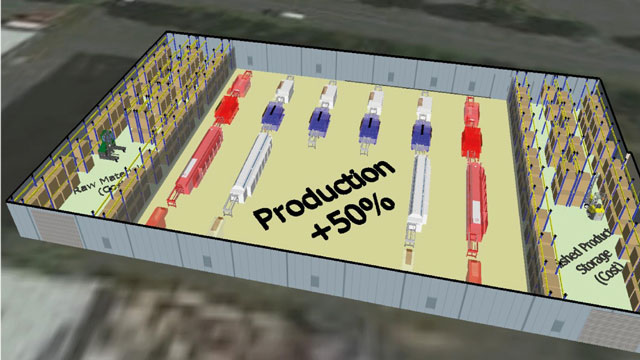
Hand sanitiser stations have been provided. Thermal imaging has been introduced at entrances and exits as a non-intrusive way of screening staff for high temperatures. An alert is sent if anyone’s temperature is above normal.
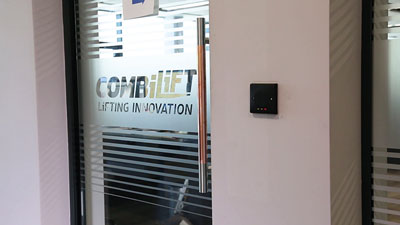
The fingerprint clock-in system has been changed to adopt the same contactless fobs used for door security on the site. Where possible doors are being kept open, and door handles have had a copper covering added – the coronavirus only survives for a few minutes on copper.
Wearing masks is mandatory in the plant, including in the office and administration areas. Mr McVicar said: “Wearing a face mask takes one to two days to get used to and then feels normal.” He added that the two-shift system had been a good way of improving social distancing cost-effectively: “Adopting two-shift operations has allowed us to introduce 2m social distancing without having to make major layout changes to the plant.” He recommended this as a key measure to other manufacturers who might have more limited space.
Overall, he said, “our productivity level isn’t 100%, but we think it’s running at 90%.”
The company is producing all models, and has not had too many difficulties with the supply chain. “The biggest challenge came at the end of February, with 26 suppliers in northern Italy,” he said, but in the event many businesses in Italy kept operating at 50% capacity. Combilift doesn’t run a just in time operation and had a sufficient buffer of stock to tide it over when the Italian firms could not deliver for two or three weeks.
The emergency appears to be increasing interest in the company’s products. Enquiries are up and in Germany the market is up by 2% over last year.
“Our products allow customers to reduce storage space for raw materials and increase space for production so that it’s easier to do social distancing,” Mr McVicar said.
Combilift does not just produce lift trucks but advises on warehouse solutions, with a team that produces warehouse plans. Normally this relied on a Combilift person visiting the customer’s factory to do a survey and see where efficiency could be improved. That is not possible in the current climate, so the company has developed a way of doing virtual site surveys so that layouts can be designed without visiting the plant.
The client walks around the premises sending images to Combilift experts using WhatsAppp and technology developed in-house. “We don’t record the whole thing, but we can take snapshots of areas of interest and ask for dimensions of those areas,” Mr McVicar said.
This has reduced the need to travel and improves efficiency, with turnaround time reduced to 24 hours.