Using MBVI, a single reading can cover all your bearings in one go – including those you can’t get an accelerometer near. Geoff Walker, operations director of Faraday Predictive, explains.
Condition monitoring has long been recognised as a useful technique to optimise maintenance work and avoid unexpected breakdowns. There are a wide range of techniques, including oil analysis, thermography, motion amplification and ultrasound, but vibration monitoring is by far the most commonly used. There is now a new approach, literally offering a new twist to vibration monitoring.
Conventional vibration monitoring uses sensors, most commonly accelerometers, that detect movement in a radial direction (up and down, or side to side) – or sometimes an axial direction. Bearing problems have been a major focus for vibration monitoring. To get a good result, readings need to be taken directly in line with each of the bearing housings, with typically at least four measurements needed for most items of equipment, where you have two bearings in the electric motor and two bearings in the driven equipment.
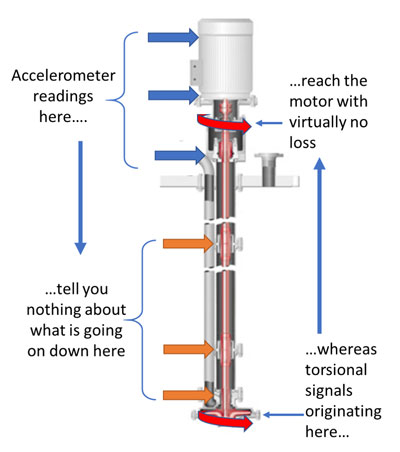
It is not always possible to get a good direct “line of sight” from the sensor to the bearing – for example with jacketed equipment, or for some duct mounted fans. And other equipment may not be accessible for taking vibration readings – such as long-shaft, submersible-head pumps (as shown in the illustration).
But there is an easy way to obtain readings in these awkward situations, by using a different type of vibration: torsional vibration. Moreover, torsional vibration is excited by a wide range of phenomena inside equipment, not just rolling element bearing faults, and it can be measured by effectively using the drive motor itself as a sensor.
Torsional vibration
Whereas conventional vibration sensors measure movement of the shaft perpendicular to its axis, torsional vibration is movement of the shaft twisting along its axis. The motor driving the equipment “sees” this vibration as subtle variations in the torque required to drive the equipment. Because motor current is affected by the load on the motor, subtle variations in torque result in subtle variations of current relative to voltage, and this can be detected and automatically analysed by a model-based voltage and current (MBVI) system to provide a broad range of fault diagnostics and condition monitoring.
Because a shaft is designed to transmit torque from one end to the other, the motor can pick up signals coming from bearings anywhere along the length of the shaft. So even with a long-shaft submerged pump like that illustrated, problems at the bottom bearing can be detected. In fact problems with any of the bearings are detected from this single measurement location. The different bearings can be discriminated by their characteristic frequencies.
Because MBVI systems are based on torsional signals, they can also detect signals that conventional accelerometers may not pick up so clearly – including journal bearing problems, vane pass rate issues, rubbing and flow turbulence. The table below shows how some phenomena – such as those affecting journal bearings and rolling element bearings – actually show up more clearly using the motor as a sensor than a conventional accelerometer.
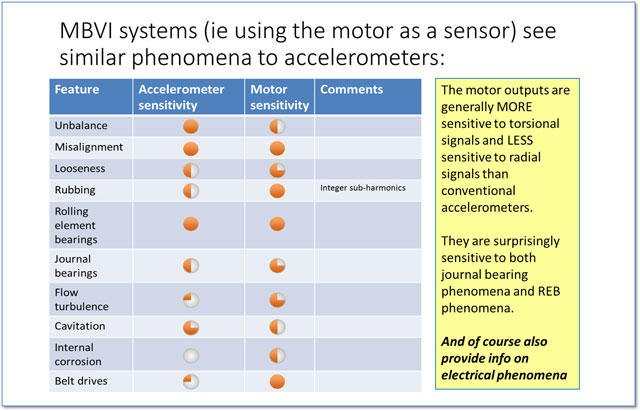
Because MBVI systems measure motor voltage and current, they can also detect electrical faults with the motor. They can also give additional information on the load on the equipment (is it being damaged by being overloaded?), its speed, the energy being consumed, and the amount of energy being wasted by developing faults, allowing energy saving potential to be calculated.
MBVI systems provide automatic diagnosis of faults and recommended interventions, for example with belt drives (see diagram) – these are an element particularly prone to wear, which can lead to large unnecessary vibrations elsewhere in the system.
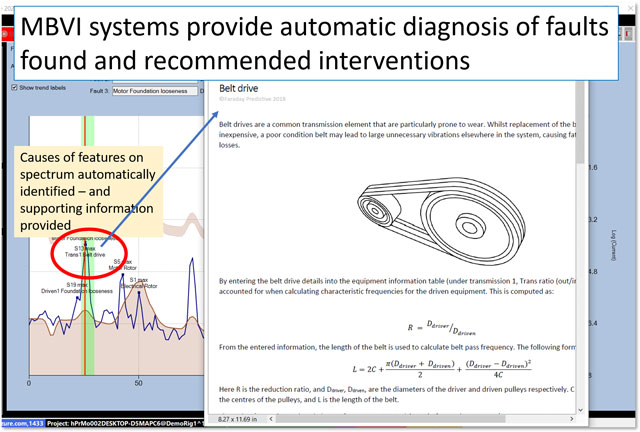
MBVI systems are available as fixed or portable units. Fixed units can store up to three months’ data locally, and the data can be downloaded periodically via USB, meaning that you can have continuous condition monitoring, with no need for network cabling if you choose.
And if you want to try before you buy, you can get testing done on your own machines by Faraday Predictive using a portable kit, giving you a risk-free way to prove the benefit before investing in buying kit of your own.
info@faradaypredictive.com
tel: 0333 772 0748
www.faradaypredictive.com