Problems with pH readings may not always mean replacing your pH probe. Julian Edwards of ABB Measurement & Analytics in the UK explains how to troubleshoot some of the most common issues.
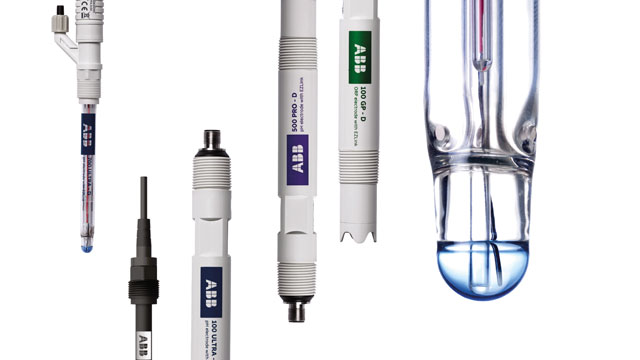
Many industries use pH measurement to monitor water quality. This includes the treatment of potable water and wastewater, but pH is also used in many other applications including power generation, pulp & paper, metals & mining and marine. In fact, more than 30% of all water quality measurements are pH measurements.
pH probes are not as easy to select and manage as many of the other sensors commonly used in industry. Most users are happy while everything is running smoothly, but if something goes wrong with a pH reading, the subtleties of electrochemistry mean that many engineers are not confident about diagnosing possible problems. There are general guidelines that can help users diagnose some of the most common faults and it is sometimes possible to fix a probe without resorting to buying a new sensor or other equipment.
pH measurements need three elements excluding the pH analyser: a pH electrode, a reference electrode and a temperature sensor (temperature compensator). These may be separate but are often integrated into a single combination electrode. Problems can arise with any of the elements or from other aspects of the installation, such as faulty cables or connections.
Here are some typical faults and the most likely causes behind them.
Short-scaling or sluggish response
Short-scaling (where the pH reading is not the value expected) or a slow, sluggish response can result from ageing of the pH electrode.
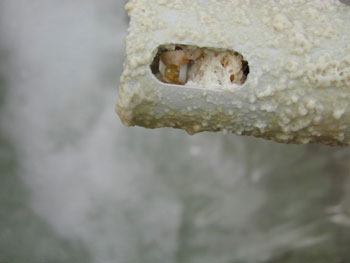
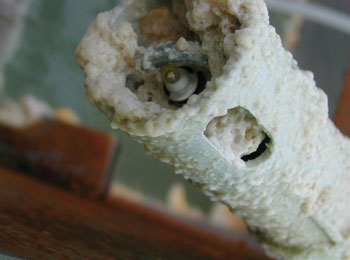
The response of the probe to pH depends on the diffusion of ions from the sample to a pH-sensitive glass where ion exchange takes place. Some types of contamination slow this process, leading to a sluggish response, while others block some of the ion exchange, resulting in short-scaling.
The usual suspects are deposits of grease, proteins, or scale, depending on the application. For example, a manufacturing process involving machinery will often have oil in the wash water, while food production raises the possibility of protein deposits. Scale problems are more likely in hard water areas.
If grease is the cause, a good wash with an organic solvent such as isopropanol is the answer. If the cause is scaling due to water hardness, the probe might need an overnight soak in acid to remove scale, while an enzyme such as pepsin can digest protein deposits.
Although deposits from the sample are the primary cause of contamination, they are not the only possibility. Be sure that dirty fingers have not left deposits on the glass during installation, for example.
Analogue sensors use a high impedance cable that makes them susceptible to interference. This can restrict the length of the cable connecting the sensor to the transmitter. With digital pH sensors, the issues associated with high impedance and restrictions on cable length are removed without compromising accuracy.
Erratic readings
Readings that “bounce” around and are not stable are usually the result of contamination or poisoning of the reference electrode. Reference poisoning lies behind more than 95% of the problems with pH sensors. The reference must be connected to the sample so eventual contamination is inevitable, although it can take years to occur in benign applications. The most common poisons are sulphides, which are present in biogas and in many power generation applications. Bromides can also be a problem.
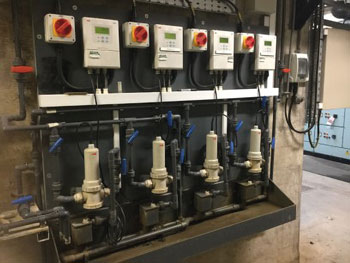
Once poisoning occurs, the reference electrode must be replaced, but there are other possibilities worth checking first. For example, make sure that there is continuity between the reference solution and sample solution. Ensure the reference probe is fully topped up with filling solution, if a refillable type is being used. A gentle shake might solve the problem, making sure the solution is in contact with the junction. Additionally, a check on the liquid junction to see that it is clean is also advisable.
Some digital sensors remove this problem by giving an early warning of electrode failure. This relieves the headache of investigating the alternatives, and the concern of lost production due to unreliable readings
Calibration issues
pH probes are dynamic systems and must be calibrated regularly. How regularly will depend on the application – a suitable interval could be anything from a week to a year. For a typical, non-critical process application such as effluent monitoring, three- to six-month intervals will usually suffice. Of course, some issues will only appear during calibration, even though everything seemed fine during normal operations.
The theoretical response of a pH probe is logarithmic and a plot of pH against output voltage should give a linear graph with a given slope. This theoretical slope is what the probe should follow, with any deviation usually expressed in percentage terms. A perfect sensor would indicate 100%; ABB probes are despatched from the factory at 98.5% or better. A slope value as low as 80% is generally acceptable in most practical applications.
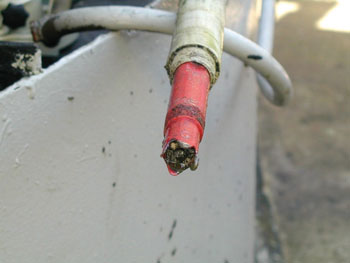
If you find that the probe has a high slope, the sensor glass may be coated with the previous sample. High slope values are often the result of contamination by a previous high ionic sample, or calibration standards being at fault. Try cleaning the probe as already described, but if this fails you may need to replace it.
A low slope may mean that the electrode is depleted of ions. This tends to happen with aged electrodes, or sometimes if the probe is being used in a low ionic water application that normally operates across a very narrow pH range. For example, if a sensor is used in the final stage of effluent purification, it will only see samples that are almost exclusively pH neutral. If this is the case, challenging the probe by submerging it in acid will often rejuvenate it.
As well as the slope value, calibration also provides a check reading, which indicates how far the sensor deviates when responding to a particular pH. ABB sensors are shipped with a maximum deviation of ±0.3pH in this value. The key point about the check reading is that it should not change. If it does, it suggests that something is happening with the reference side of the system.
Usually, the check reading will change very slowly over a long period of time; it will potentially rise and fall with each calibration but, if the values are recorded, a general drift in value in one direction, up or down, will be observed. Any sudden change in check value should be investigated.
Ask the experts
Although users should be able to diagnose and treat some of the common problems that arise with pH measurements, the fact remains that pH sensors are complex, dynamic electrochemical systems. If you are still in doubt, it may be best to check with your supplier. Reputable vendors will always offer to support their equipment with expert advice to solve any issues.
For more information about how ABB can help with your pH installation, email enquiries.mp.uk@gb.abb.com or call 0870 600 6122, reference ‘pH’.