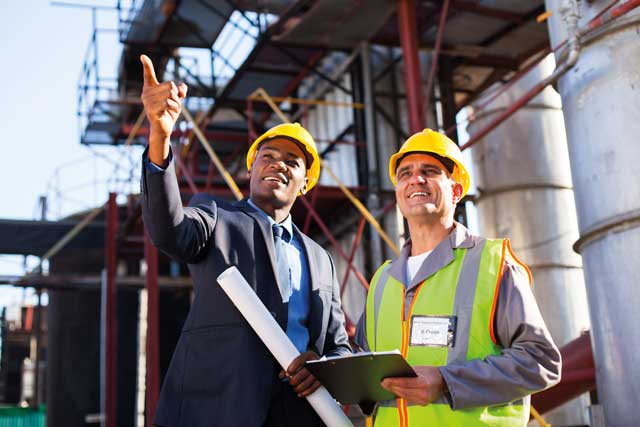
ABSTRACT
The third of a series of three, this article sets out to describe where the Early Equipment Management (EEM) principle embedded within the TPM philosophy can bring substantial improvements to a company’s existing new product development and introduction processes involving capital physical assets.
EEM is driven by a belief that behind the plant and equipment used in any production process there are three functional groups that are essential partners for optimising new product and equipment introduction, namely:
- Commercial (sales, marketing and finance)
- Engineering (design, product, tooling, equipment, process and procurement)
- Operations (operators and maintainers).
This three-way partnership requires true teamwork in a sustained drive towards improving project and design management performance through the early identification and elimination of hidden losses such as poor maintainability, operability and reliability plus the essential safety, energy and environmental considerations. This is based on the accepted reality that as much as two-thirds of total life cycle costs are determined in the early concept and design specification stages: hence the EEM pillar of TPM.
By tapping into the knowledge base of your existing front line operators and maintainers at the concept and high level design stage onwards, you stand a realistic chance of minimising the risk of expensive and disruptive retrofits during and after commissioning of new capital equipment.
1 Early Equipment Management
The fifth founding pillar of TPM (Figure 1), Early Equipment Management (EEM) is also occasionally referred to as TPM for Design to highlight the fact that it is about the early involvement of existing operators and maintainers at the very start of a capital equipment investment, namely at the concept and definition stage.
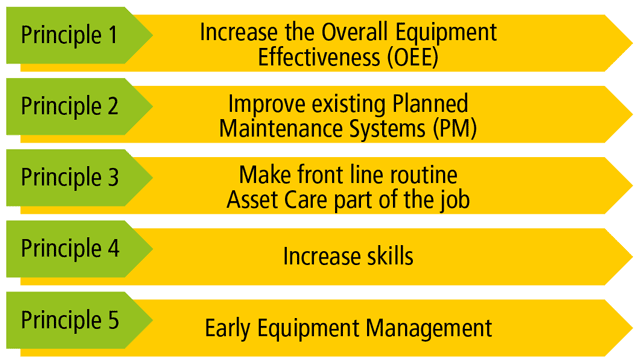
Figure 2 illustrates the EEM alignment to the four maturity milestones (MS1-MS4), and how this alignment between all five foundation pillars moves towards the goal of striving for the four zeros: zero accidents, zero defects, zero breakdowns and zero operator interventions.
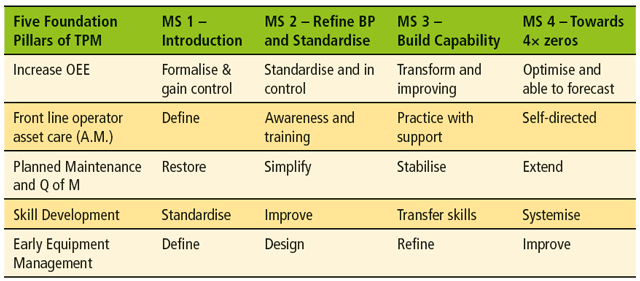
2 The principles of Early Equipment Management
EEM is a systematic and structured way of using common sense. That is, if you are going to design or buy a new machine, then make sure you involve the existing operators and maintainers in the vital investment decisions by tapping into their existing practical knowledge base at the earliest possible opportunity.
It is generally accepted that a manufacturing organisation’s commercial and financial people need an early input, together with their design engineering colleagues, in order to set the customer expectations and the financial and performance guidelines within which a new machine or process has to work. EEM suggests there is a third vital member of this partnership, and that is Operations. The aim is to acquire a machine or process that is both easy to operate and easy to maintain by considering the views of the front-line operators and maintainers at the design concept stage, not at the commissioning and ramp-up stage when it is too late or expensive to change things.
In other words, behind the plant and equipment used in any operations process there are three functional groups that are the essential partners for new product and equipment introduction, namely:
- Commercial (sales, marketing and finance)
- Engineering (design, product, tooling, equipment, process and procurement)
- Operations (operators and maintainers)
The EEM philosophy recognises that these activities must be coordinated and focused on the TPM objectives as a shared responsibility. The partnership requires a sustained drive towards improving project and design management performance through the early identification and elimination of hidden losses such as poor maintainability, operability, reliability, safety and environment (easily remembered as MORSE). This is depicted in Figure 3, The essential partners of EEM. These losses should be picked up, addressed and eliminated early in the equipment management process, and not when the equipment arrives on the manufacturing floor for start-up production – where the goal might be described as “flawless operation from day one”.
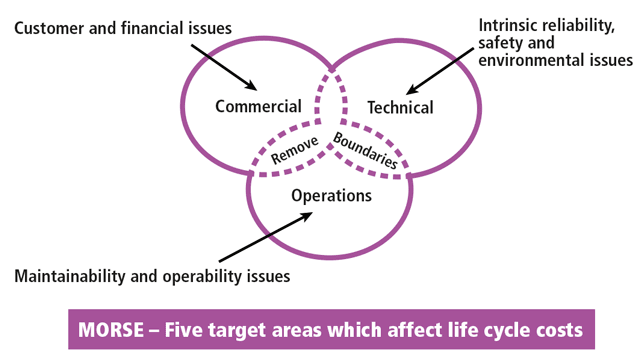
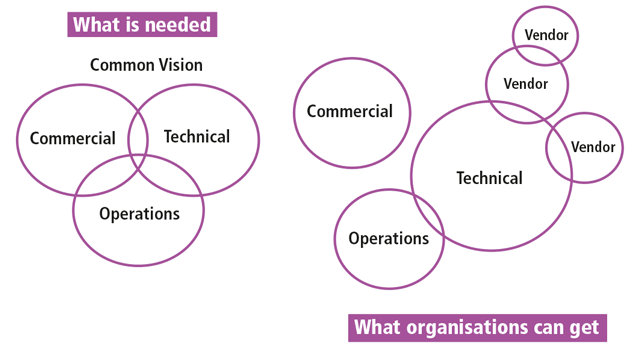
Typical benefits of adopting the EEM approach are illustrated by these three examples.
- Dry packing – $150,000 (£116,000) annual benefits from early management capital project
- Chemical process line – $300,000 (£232,000) additional annual benefits from capital project
- Machining centre – New capital investment reached 75% OEE in three weeks against a historical background of c45%.
3 The hidden costs of investment decisions
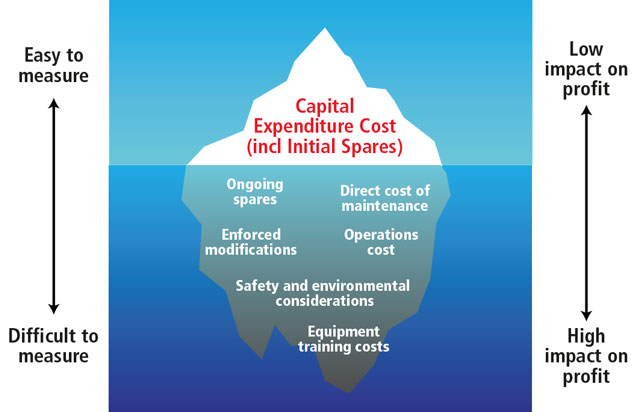
Like the iceberg shown in Figure 5, the true costs of investment decisions are seven-eighths hidden. It is easy to measure the capital cost when a new machine or process is bought, but the costs of owning the equipment over its lifetime (referred to here as total life cycle costs – TLCC) will include:
- the cost of spares
- maintenance expenditure
- how much the equipment costs to operate
- the opportunity costs of ineffective performance, and hence low OEE.
An item of equipment costing less than another at the time of purchase might well cost significantly more to run and repair over its useful life. Only by estimating those continuing costs, predicting their impact, and comparing the different potential options and solutions at the outset can a better understanding of the added value and hence profitability of that asset over the long term be gained. If the equipment does not meet its specified running rate, and causes safety or environmental concerns, the impact on profitability can be significantly greater than the initial difference in purchase price. The EEM process might not resolve all these issues, but it forces organisations and suppliers to plan and predict better outcomes.
4 Tackling ‘urgency addiction’
A dilemma facing many companies is what might be called “urgency addiction”, where project timetables and unrealistic promises conspire against getting the appropriate people involved at the right time. Urgency to meet design deadlines means that ideas are defined and selected, and the project moves on to the next phase, without sufficient thought, challenge, discussion and debate. This is based on the fundamental belief and the reality that as much as two-third of total lifecycle costs are fixed in the early design concept and high level design specification phases. Hence the need for the EEM pillar to be embedded in the TPM system to make sure all parties are involved at this critical stage.
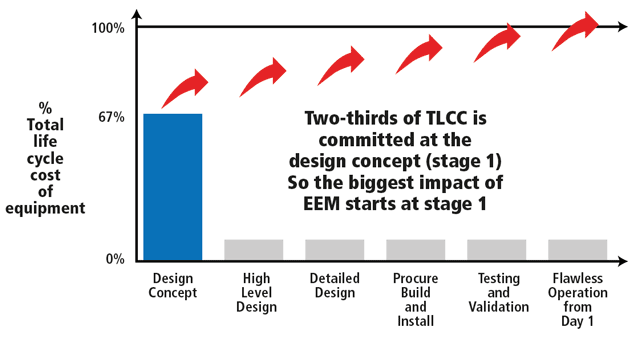
In Figure 6, showing where the costs are committed, six main phases within the concept to delivery cycle are proposed, as follows:
- Design concept
- High level design
- Detailed design
- Procure, build and install
- Testing and validation
- Flawless operation from day one.
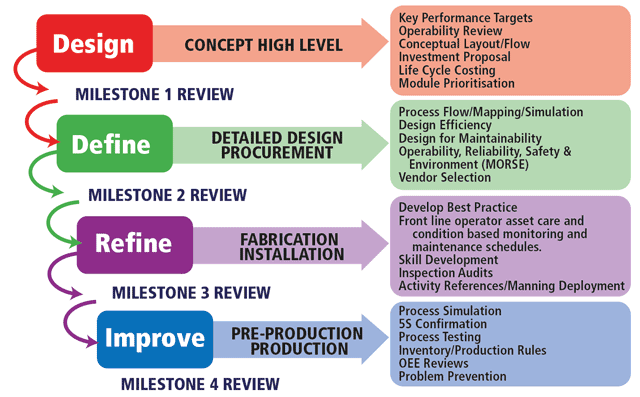
Figure 7, The EEM route to vertical start-up, illustrates how the above-mentioned phases of an asset’s lifecycle may be managed from an operations and maintenance viewpoint by the four TPM milestone management levels, described as define, design, refine and improve, where:
At milestone MS1, Define = Concept to delivery
At milestone MS2, Design = High level and detailed design
At milestone MS3, Refine = Fabrication, procurement and build
At milestone MS4, Improve = Testing, commissioning and operations.
The typical management focus and delivery characteristics are shown as outputs on the right-hand side of the figure. The four levels have clear alignment to the four TPM maturity milestones shown in figure 2, which are in turn complementary and integral to the five founding principles (figure 1).
5 Enhancements EEM can bring to the business
In order to identify what the EEM philosophy can add to a company’s existing new product development and hence new equipment processes, the rationale is as follows:
There are three main TPM for Design techniques used via EEM, which are referred to as:
- objective testing,
- knowledge base management
- milestone management.
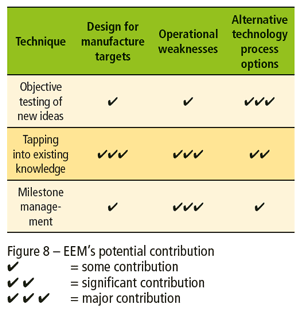
These are illustrated in figure 8 as EEM’s potential contribution by focusing on maintenance prevention and operations contribution and impact.
It is necessary to be very specific about what is really meant by the phrase “tapping into existing knowledge”. One of the best ways of doing this, as far as TPM is concerned, is to remind oneself of what the TPM teams of operators and their maintenance colleagues experience when they work through the eight equipment steps on TPM pilot projects on existing assets. They can bring this knowledge – which is based on learning by doing – to the next generation of equipment and hence to the EEM discussions.
This learning experience can be illustrated as shown in Figure 9.
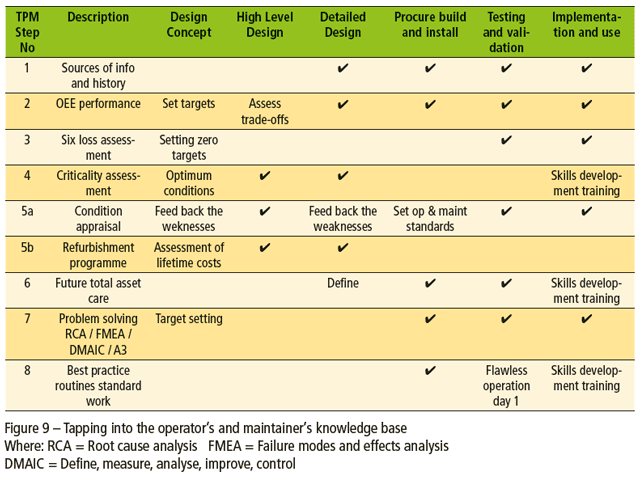
6 Potential benefits of adopting the EEM approach
Early Equipment Management has been shown to provide benefits in three main areas of equipment, people and business, as follows:
Equipment benefits:
- Setting a front-end vision to strive for flawless operation from day one production start-up
- Improved reliability, product quality and productivity
- Established standard work and best practice procedures prior to start-up, including focusing on the MORSE checklists.
People benefits:
- Structured feedback ensuring all opinions are considered and respected
- Prior knowledge and experience captured and embodied
- Early identification of skills requirements, with training started in advance of commissioning
- Early involvement building trust, ownership and realistic expectations.
Business benefits:
- Reduction in lifecycle costs as a measurable route to increased profitability
- Milestone sign-offs prompting a regular, structured and precise business review
- Production ramp-up faster with key performance indicators agreed prior to start-up.
Figure 10 illustrates why EEM makes sense, and is a useful way of illustrating the “before” and “after” effect of using the EEM philosophy. The green line illustrates how the EEM system captures significant total lifecycle cost impact changes, which are seen as opportunities early in the development cycle. This is as opposed to the red line, where changes are forced on the team as expensive retrofit necessities.
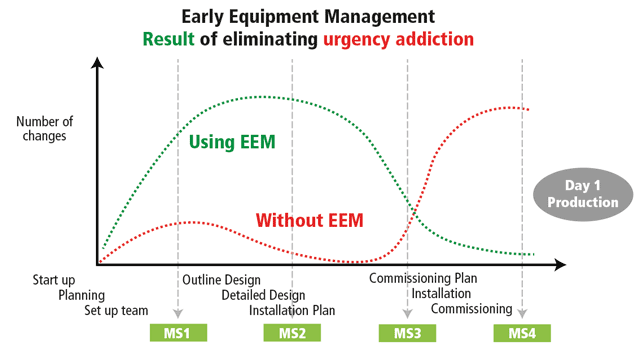
7 The detail behind the EEM pillar
In the authors’ book TPM – a foundation of operational excellence [1] the chapter on EEM includes five case studies and concludes with a requirement for an initial front-end planning day, followed by a two-day practitioners’ workshop. Supporting appendices provide further details on running such a workshop and on undertaking an EEM honesty check, as well as an EEM project data checklist and an example of a MORSE checklist.
EEM Planning Day
Typically, an EEM planning day would set out to agree the following:
- Identification of the potential upcoming live project or projects in which to undertake a trial of the EEM philosophy and system
- The project team structure, its members and their roles and responsibilities
- The perceived improvements that the EEM process might bring to the project, taking into account the necessary alignment to tailor it to the company’s existing new product development and new asset systems and processes
- How the EEM approach will enhance (rather than replace) the existing project management tracking processes
- How the maximum transfer may be made of existing knowledge, gained through applying the TPM System to the existing assets; and what will be the potential impact and benefit of doing this on a forthcoming project involving significant capital expenditure
- Changes to and expansion of the MORSE checklists to reflect the specific organisation’s product technology, vocabulary and resultant asset characteristics
- The two-day EEM practitioners’ workshop: attendees, purpose, content, outcomes and timing.
The Two-Day Practitioners Workshop
The purpose of the two-day practitioners’ workshop is to address, by doing and application, how the activities identified in the planning day need to be co-ordinated and focused on the business and manufacturing imperatives, and into the objectives, in order to maximise their potential. This requires a sustained drive towards improving project and design management performance. It also requires that the EEM process demonstrates effectiveness as early as possible through the elimination of potential hidden losses which arise from poor or inadequate MORSE issues.
The intention is to use an upcoming new project to see where the EEM philosophy could enhance the company’s existing and proven new product development processes and to use and embed any lessons arising from the workshop by building on the existing processes as part of an embedded culture of continuous improvement
EEM Honesty Check
The authors use a list of ten checkpoint questions that they have developed over the years as the result of running EEM practitioners workshops for the offshore oil and gas industry, and aeroengine, food and drink, packaging, electrical and electronic and life sciences manufacturers, where the significance of new product or equipment focus is paramount in the total lifecycle process.
The EEM systematic approach addresses each of the ten fundamental reasons for gaps in existing new product introduction and capital project spending practices. It also recognises that it is the person carrying out the front line day-to-day tasks on the new asset who is the key, and the way in which they are supported is vital to achieve true cost-effectiveness.
An EEM Project data checklist lists 16 questions to ask ahead of the start of a new capital project.
An example of a MORSE checklist illustrates the practical potential of adopting the EEM philosophy as a series of “what if…” questions, to ask retrospectively on a recent project to highlight what would be done differently if starting afresh.
8 Conclusion
As stated in the previous articles, the TPM philosophy is first and foremost a system of work in which EEM is one of the founding pillars.
By viewing TPM as a core system in your business you can identify the ideal behaviour patterns which you need the system to support. Ideal observable behaviour encouraged via EEM includes:
- safety awareness and management
- following, improving and adhering to standards
- teamwork, with respect and humility
- equipment consciousness, ownership, pride
- willingness to learn new skills
- seeking and using data
- problem-solving root cause, ideas for problem elimination/problem prevention
- experiment and testing to allow improvement
- listening to and acting on ideas
- customer awareness
- fastidious cleanliness, workplace organisation
- eagerness to challenge current state performance.
Clearly defining core systems such as EEM and their constituent processes is a fundamental step in achieving sustainable operational excellence.
[1] TPM – a foundation of operational excellence.
Peter Willmott, John Quirke and Andy Brunskill.
Published by SA Partners, 2019.
ISBN 978-1-9993748-1-5.
£39.99 with a £2 donation shared between Friends of Chernobyl’s Children and The Prince’s Trust for each copy sold.
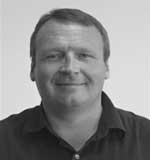
Andy Brunskill
Partner and Global TPM Lead
SA Partners LLP