Contaminant-free compressed air and lower life cycle costs can be achieved at the same time in food and beverage operations, says David De Pril, head of product management and marketing, ELGi Europe.
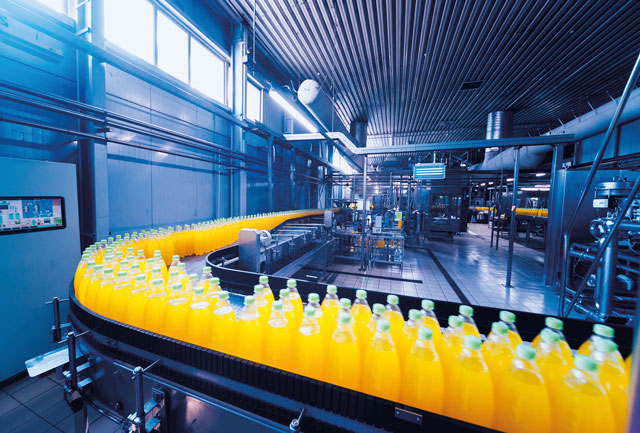
On a recent visit to a production site of a major global drinks manufacturer, I was surprised to learn of the complexity and seriousness of the company’s approach to ensuring oil-free air. Though it had employed the latest technologies and machines, the company had not foreseen that small oil leaks would be spilled on and absorbed into the concrete floor during maintenance. This oil would evaporate during hot weather and those contaminants would then be drawn into the compressor, leading to tiny but significant levels of oil contamination.
The solution entailed placing the compressor equipment in a contaminant-free environment, regular cleaning of an epoxy-resin floor and strict protocols to maintain this environment.
For food and beverage (F&B) companies, the importance of oil-free compressed air is nothing new. Oil-free compressors meeting ISO standard 8573-1 specifying purity classes for particles, water and oil have proved critical. But as with all such stringent standards, they add to costs and energy consumption, and ultimately make life harder for operations leaders who need to reduce the life cycle cost of their capital investments.
In addition all sectors, including F&B, face the challenge of improving the environmental sustainability of their organisations.
The well-known phrase “from farm to fork” is often used in consideration of the sustainability of the entire food production supply chain. There is rightly a focus on the need to avoid contaminants throughout the chain. Given that compressed air is used in most stages of food and drink production, from oxygenating the water in aquaculture or fish farms, to preparing fizzy drinks or in the sanitation of bottles and packaging, contaminant-free air is a must.
Contaminant-free air versus low life cycle cost
F&B operations require compressed air that is completely oil-free. These applications demand wide operating temperatures of 0-45°C, stringent air purity standards higher than ISO 8573-Class I, high levels of safety, and eco-friendly operation to name but a few.
Contaminants can enter the food chain inadvertently and unintentionally at all stages. The ALARA principle states that the presence of a contaminant should be reduced “as low as reasonably achievable”, clearly establishing the priority for all aspects of food production – especially the compressed air industry.
Addressing this issue, in 2018, Food Drink Europe published the Toolbox for Preventing the Transfer of Undesired Mineral Oil Hydrocarbons into Food by Food Federation Germany (formerly the German Federation for Food Law and Food Science or BLL). It contains guidance and recommendations for the food industry in limiting contamination from various stages of food production. The guide recommends users to “check compressed air for oil penetration on a regular basis” and “use oil-free compressors, and if possible, draw in zero-emission environmental air”. It sounds simple, but real life F&B operations are anything but simple.
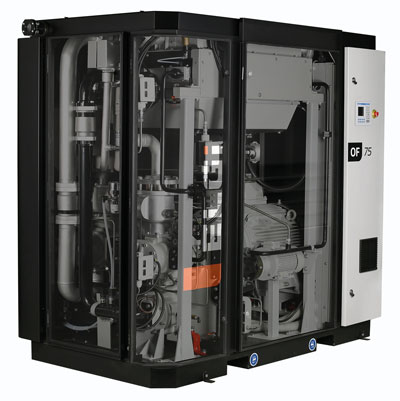
Filter it out
To meet such standards, in an oil-free screw compressor, an air cooler removes the heat from the compression chamber. The dry running rotors rotate at high speeds to achieve high volumetric efficiencies. Timing gears synchronise rotation to prevent contact. A separate lubrication system lubricates the timing gears. And finally, an effective sealing system prevents the entry of lubricating oil into the compression chamber.
Filtering removes much of the oil but not all of it. For example, pre-filters, high efficiency coalescing filters and activated carbon filters remove trapped oil to a great extent. But these filters themselves have limitations. For instance, above 20°C, coalescing filters cannot remove fine oil vapour, leaving very fine particles of residual oil in the form of aerosols; and activated carbon filters are not usable at filtration temperatures above 40ºC because the carbon absorbs the oil vapour, gets saturated, and becomes ineffective.
Moreover, filters create drag, resulting in increased energy use and costs. For every filter that is installed in the downstream compressor line, the increased differential pressure results in increased energy consumption of around 1% per filter. Filters are often installed and paired in combinations in the compressor room and at the point of use, resulting in further costs.
It is no wonder, then, that contaminant-free air in the F&B sector has seemed at odds with the need to reduce the life cycle cost.
Best of both worlds
Today, innovation and new product development have resulted in solutions that provide ISO:8573 (P-2):2007 ‘Class 0’ oil-free air, to ensure that 100% contaminant-free air is produced for various applications in manufacturing and packaging processes.
Technological advances and market developments in oil-free technology and ‘Class 0’ certified compressors mean that operations have access to technology that provides not only oil-free air that meets the most stringent standards, but also achieves much higher energy savings and uptime at lower life cycle costs.
ELGi is one of the few compressor companies that designs and makes its own oil-free air-ends as well as its own pressure vessels, castings, and motors while also conducting complete machining and compressor assembly. With in-house technology and manufacturing capabilities of these various elements, compressors can be engineered to provide maximum uptime and reliability, leading to an optimised compressed air system for operators.
The technology exists to cater affordably to the dual demands of contaminant-free air and improved life cycle cost. Food and beverage operational leaders need not only the best and most reliable compressors, but also expert support in designing and optimising the complete compressed air system.
A solution-focused, comprehensive approach building on the components but holistically looking beyond just the compressor room is essential to lowering the life cycle cost.
The F&B sector must contend with increasingly demanding regulatory challenges regarding quality, safety and energy efficiency while addressing the need to feed a growing population sustainably. Given that compressed air is often referred to as the “fifth utility” in acknowledgement of its vital role in manufacturing, the compressed air industry must continually innovate so as to support F&B operations in meeting these challenges.
Oil-free air will become more prevalent, supported by design initiatives to further improve cost and efficiency; data will serve as a key enabler, and with this the evolution of change will speed up, delivering ever-increasing savings and improvements for this vital energy source in manufacturing.
ELGi offers a complete range of compressed air solutions from oil-lubricated and oil-free rotary screw, reciprocating and centrifugal compressors, to dryers, filters and downstream accessories.
Further info:
ELGi Compressors Europe
euenquiry@elgi.com or elgieuropemarketing@elgi.com
www.elgiaircompressors.eu
ELGi Compressors UK
ELGi-UK_Ireland@elgi.com | +44 2037693605 | www.elgi.uk