Marc Stuart, Falkirk Service Centre Manager for Sulzer, discusses the challenges in repairing a high-voltage motor from an oil and gas platform.
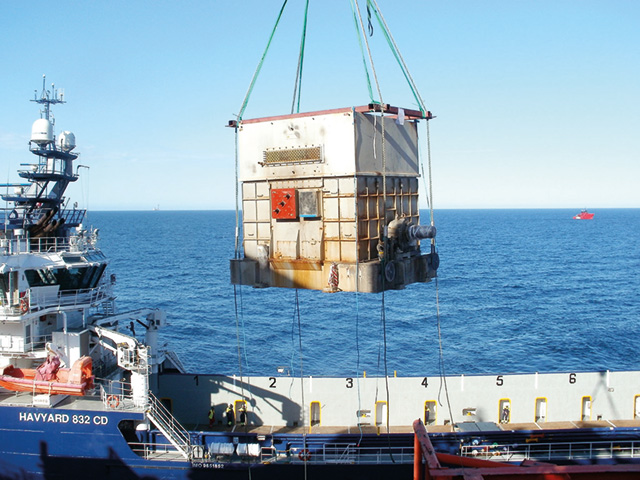
Floating production, storage and offloading vessels are purpose-built for the offshore oil and gas industry to process hydrocarbons and act as temporary storage facilities. They are complex structures with a great deal of equipment installed in close quarters. It is, therefore, quite an effort to remove a component as large as a 10.7 MW motor so that it can be taken onshore for planned maintenance.
Refurbishment projects such as this need to be completed by a properly qualified service centre that is approved to work on components that are Ex-rated and operate in potentially explosive atmospheres. The specialist design features that ensure safe operation must be maintained in this challenging environment.
Extending service life
In one example, Sulzer was contracted to complete a motor change due to deterioration of a 10.7 MW electric motor, which had been in service for 10 years. A number of repairs were suggested for the outgoing motor, including new stator coils, replacing bearings and checking critical clearances. The rotor only required routine maintenance but the whole project would enable the motor to provide at least another decade of reliable service.
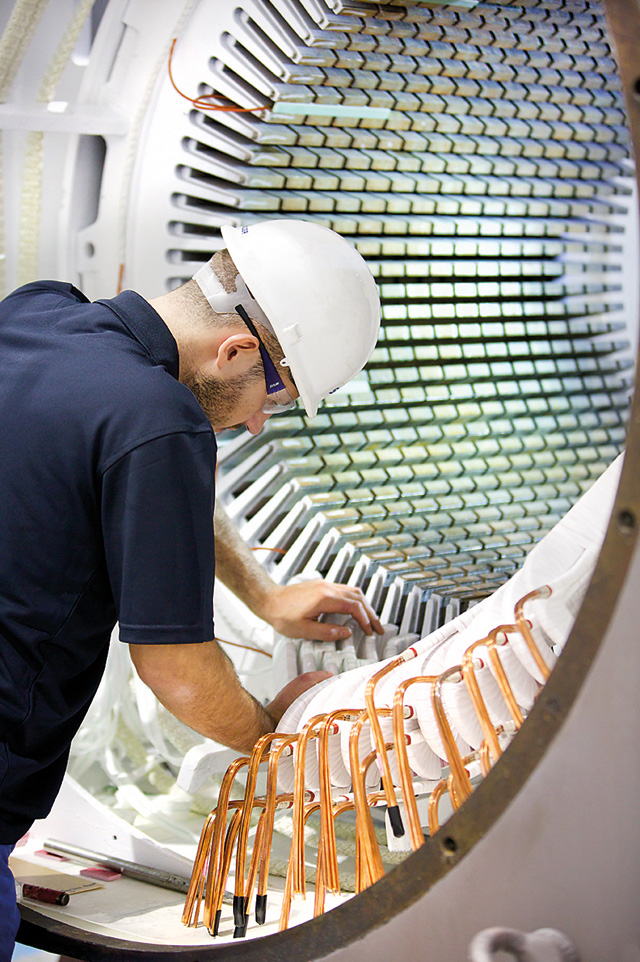
The motor, which was originally manufactured by Laurence Scott in 2007, powered a high-pressure export compressor. Sulzer is currently the authorised repairer for ATB Laurence Scott motors and offers its technical expertise and rapid response to all customers, especially those operating in North Sea oil and gas. Facilities in the Sulzer network, such as its in-house copper mill and high voltage coil manufacturing centre, combined with expertise in the offshore sector, were among the reasons that the company was selected.
Specialist training
Although much of the refurbishment process was routine, special attention was required to all the electrical connections and their enclosures to maintain continued compliance with Ex regulations. Any equipment that is designed for operation in potentially explosive atmospheres must be repaired and installed by suitably qualified engineers.
In this case, Sulzer was holding a spare motor in stock, and this was transferred on to the FPSO as part of the process.
Any downtime on an FPSO can incur significant costs in lost production, and for important assets such as the high-pressure export compressor, it is prudent to have spares available at short notice. However, due to the complex crane lift required to transfer the motors to and from the vessel, the operation had to be carefully timed to coincide with a calm sea, which can be a rarity in the North Sea.
Close cooperation
In situations where an unexpected issue requires immediate attention, Sulzer can draw up a rapid response plan to help a customer diagnose the problem and provide the most appropriate solution. The offshore industry is particularly averse to downtime, so round-the-clock working can be instigated to complete repairs in the shortest time.
The close technical cooperation between ATB Laurence Scott and Sulzer ensures that customers receive the highest level of maintenance service. In this case, that included a complete set of new stator coils, which were manufactured in Birmingham by Sulzer’s high voltage coil shop, while the mechanical repairs were completed in Falkirk.
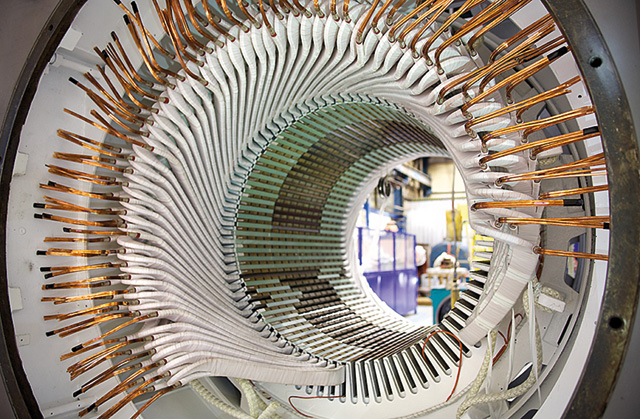
Once the work was complete, the rebuilt motor was comprehensively tested before a full factory acceptance test was carried out by ATB Laurence Scott. The test ascertains that the correct procedures have been completed and that the rebuilt motor met the original manufacturers’ standards.
Speed and expertise must go hand-in-hand for projects like this to be a success. Working with a team of skilled engineers that has the support of the OEM ensures the repairs will be made quickly, and in this sector, time is certainly of the essence.
www.sulzer.com/en/applications/oil-gas-chemicals/upstream
service.uk@sulzer.com | +44 (0)121 766 6161