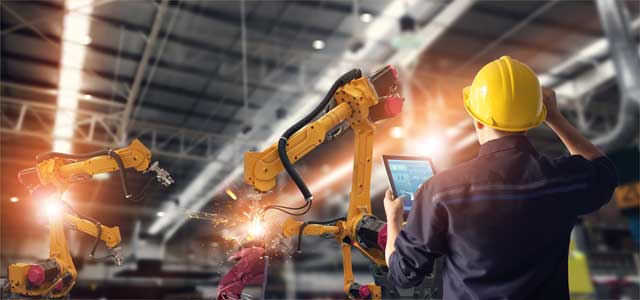
ABSTRACT
The Covid-19 pandemic and other factors, such as Brexit, are highlighting the need to ensure the UK manufacturing sector is both competitive and resilient. A major difference between manufacturing businesses in the UK and their competitors overseas is the low rate of adoption of robot automation. This has resulted in lower levels of productivity.
This paper discusses the positive impact an increase in robot adoption could provide to UK manufacturing for both growth and productivity. The use of robots has often been seen as a threat to employment and this issue is also considered. To address the low uptake it is suggested that government support and assistance is required, particularly due to the large numbers of SMEs within the UK. A number of government measures are proposed both to encourage and help these business to apply robot automation to their manufacturing operations. Finally the conclusion provides an indication of the benefits that could accrue from the increased use of robot automation within the UK.
Introduction
The full impact of the Covid-19 outbreak on UK manufacturing will probably not be known for a number of years to come. However the closedowns, travel restrictions and general uncertainty happening across the world has certainly highlighted issues in the way the manufacturing sector currently operates. Complex and long distance supply chains have been stressed or broken by the impact of the virus in different countries. Also, the dependence on manual operations has made it difficult to maintain productive capability given the restrictions on travel and social distancing requirements, never mind the general nervousness of employees in attending work.
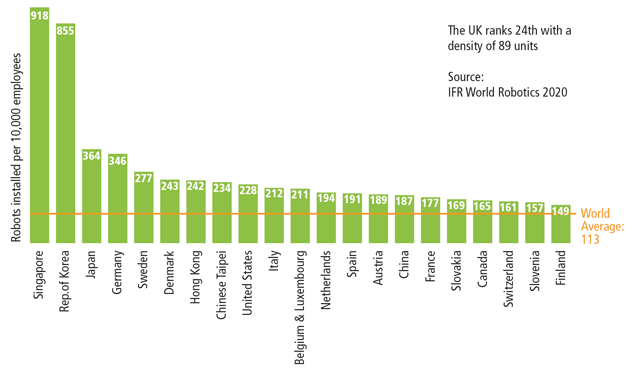
These current issues have added to challenges already being faced in UK manufacturing including the rising minimum wage, increasing material and energy costs, low levels of productivity and also Brexit. One of the implications of Brexit was to reduce the availability of so-called “low-cost labour”. The UK has become a much less attractive place for Eastern European workers and there was an increasing trend of workers returning to their home countries. Current government policy is to restrict immigration and therefore it is unlikely workers from other countries will be available, even if they wish to come.
A slightly longer-term challenge is the growing trend towards mass customisation requiring local, agile manufacturing to truly meet the needs of a consumer wanting to specify exactly what they want and expecting prompt delivery as well. The increased cost of transport, and the environmental concerns regarding carbon footprints are also adding to the drive towards reshoring of manufacturing.
Perhaps now is the time to consider a different approach to manufacturing in the UK. The application of automation and robotics technologies provides the opportunity to build a highly productive manufacturing sector that is resilient in the face of future global challenges. One key benefit from the much greater application of robot automation is to provide the opportunity to utilise workforces much more efficiently and productively: to use the skills and attributes of staff to add value to the products and not in performing mundane, repetitive or dirty demanding tasks. A reduced dependence of labour would then provide greater flexibility of capacity and resilience in times of labour shortages. If a factory is largely automated it is much easier to scale production by varying operating times.
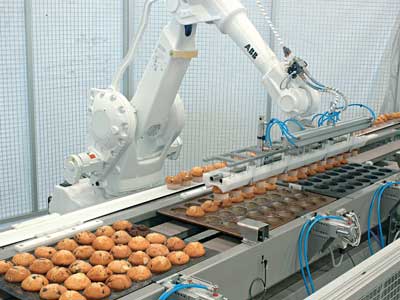
(such as muffin picking), or arduous (such as
palletising, below).
Automation and productivity Robots improve productivity when they are applied to tasks that they perform more efficiently and to a higher and more consistent level of quality than humans. In their study focused specifically on robotics,
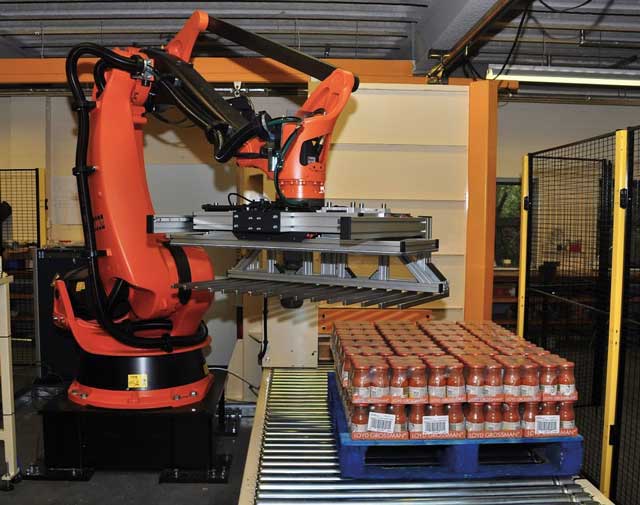
Graetz and Michaels concluded that an increased density of robots increased annual growth of GDP and labour productivity between 1993 and 2007 by about 0.37 and 0.36 percentage points respectively across 17 countries studied. This represented 10% of total GDP growth in these countries over the time period and was comparable to the 0.35 percentage point estimated total contribution of steam technology to British annual labour productivity growth between 1850 and 1910 [1].
There is a host of international evidence to demonstrate the link between technology uptake and productivity growth. McKinsey Global Institute provided a comprehensive round-up of the benefits of automation, which included higher productivity, better safety records, higher wages, access to cheaper and higher-quality goods and a rising standard of living [2].
In the UK, figures from the Society of Motor Manufacturers and Traders (SMMT) illustrate the positive impact automation has had in the automotive sector. The adoption of advanced technologies in the sector increased productivity (measured as vehicles manufactured per person) by a factor of 3 between 1984 and 2016. Between 2011 and 2016 the greatest rate of growth for vehicle manufacture also coincided with an increase in employment in the sector, from 124,000 to over 150,000.
The UK is lagging behind other advanced nations in overall productivity: UK output per hour worked grew by an average of 0.2% p.a. (2008-2017), compared with France 0.6%, Germany 0.8% and the US 1% per year. This lagging productivity is in part due to UK companies not adopting automation at the same rate as those overseas. To illustrate this point, robot adoption in the UK is significantly lagging behind its major competitors. The International Federation of Robotics calculates robot density data, the number of robots per 10,000 employees (Fig 1). This shows that the UK has a robot density of 89, below the world average of 113. Examples of other countries include South Korea at 855, Germany at 346, the US at 228, Italy at 212, Spain at 191 and France at 177 [3].
If the UK continues to fall further behind it will find it increasingly difficult to compete. However, there is a benefit in this starting position. It is not necessary to develop new solutions or technologies. The answers are already in place, proven and are available.
Opportunity for UK manufacturing to grow
Automation can result in radical improvements in cost efficiency, allowing work to move back to the UK from low-wage economies and strengthening UK supply chains. As an example, increased productivity is enabling firms such as Whirlpool, Caterpillar and Ford Motor in the US and Adidas in Germany to restructure their supply chains, bringing back parts of the manufacturing process to the country of origin.
The Reshoring Initiative in the US estimates that 250,000 jobs have been brought back to the country by reshoring and inwardbound foreign direct investment since 2010 [4]. Not only does automation permit reshoring, companies that deploy robots are less likely to relocate or move work offshore in the first place, according to a report by the Fraunhofer Institute for Systems and Innovation Research [5]. Reshoring brings other advantages, with the potential for demand spill-overs into other sectors, the accumulation of specialist manufacturing knowhow that is critical for attracting and expanding talent, and for national competitiveness.
There is also a link between productivity, company competitiveness and increased demand [1]. If the increase in production results in wage increases or increased employment overall, increased demand spills over into other sectors of the economy [6], creating a virtuous circle of increased productivity, increased demand, increased wages and spending power, leading to increased demand for other products and sectors. Economist Tyler Cowen points out that manufacturing in particular seems to create strong spill-over effects, both within the sector and in complementary sectors [7].
Impact on jobs
The tasks traditionally most suited to automation are those which are repetitive, high volume, hazardous or arduous, require a high degree of precision or cleanliness, or are high speed. Automation is increasingly becoming applicable to low volume tasks. Successful automation of a process traditionally depended on having known, consistent and ordered inputs. More advanced technologies, particularly the use of machine learning and artificial intelligence, will significantly increase the flexibility of automation applications and open up more activities to be automated. Tasks requiring creativity and unique, variable and undefined activities will remain the least likely tasks for automation.
There has been much publicity regarding the risk of large-scale job losses from automation. More detailed analysis takes a view of tasks, rather than jobs, being automated, such as that by Arntz et al [8]. This analysis suggests that less than 10% of jobs can be automated entirely and that the level of potential automation of tasks within a job varies greatly according to job and industry. As McKinsey puts it, “More occupations will change than will be automated away” [2]. This is an important differentiation as it paints a picture, supported by BARA’s experience, of a future in which robots and humans will work together, doing what each does best, with positive effects not only for the competitiveness of the fi rm, with attendant repercussions for employees, but also on the quality of work carried out by people.
It is also important to note the fact that a shrinking labour force in one sector does not automatically equate to aggregate job losses – the issue is whether the losses in one sector or job type are balanced by gains in another. For example, Bessen argues that from a historical viewpoint, new jobs in sectors such as manufacturing and services have replaced jobs lost in sectors such as agriculture in the US, where employment has fallen from around 40% of the labour force in 1900 to less than 2% today [9]. Similarly, a survey by the World Economic Forum of member companies predicted that robotics will be a strong driver of employment growth in the survey’s Architecture and Engineering job family [10]. Consultant Deloitte argues that “While technology has potentially contributed to the loss of over 800,000 lower-skilled jobs [in the UK] there is equally strong evidence to suggest that it has helped to create nearly 3.5 million new higher-skilled ones in their place” [11].
One of the strongest arguments for automation adoption and productivity improvement as an engine of job creation is the fact that the nations with the highest robot density – South Korea, Japan and Germany – also have among the lowest unemployment rates.
The data indicates that mature economies with a high density of industrial robots have lost manufacturing jobs at a slower pace than those that have invested less in robots. This suggests at least that automation does not destroy jobs, even if it does not establish a definitive correlation between productivity and job creation. In some countries, the manufacturing sector has been hollowed out not by automation, but by offshoring – a process that can have a more damaging long-term effect on both employment levels and growth. One way to protect against offshoring, or drive reshoring, is to maintain high levels of productivity at home.
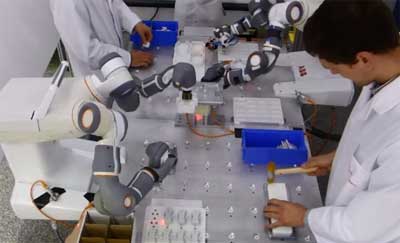
Government support
Over recent times much of UK industrial policy has been driven by the market, with the government taking a hands-off approach to industrial strategy. This started to change with the Made Smarter initiative on Industry 4.0, but the issues surrounding Brexit have delayed progress.
Most developed countries have active government interventions to promote leadership and the adoption of industrial digital technologies (IDTs) in their industrial bases. For example, while the UK lacks a clear narrative, Germany has Industry 4.0, the US has “America Makes”, China has “Made in China 2025” and France has “Industrie du Futur”.
A large percentage of UK companies are small or medium firms (SMEs), and unfortunately industrial SMEs frequently lack the information, expertise, skills, training, resources, strategy and, moreover, the confidence to adopt new technologies. This means that appropriate support and advice is essential.
Unlike other developed nations, the UK’s tax system does not provide incentives for increased automation among SMEs. It is vital that the government supports industry through a more robust capital allowances scheme for adopters of automation solutions.
It is also critical to upskill industrial workers in the use of industrial digital technologies, ensuring quality training and education can be accessed. Training must be available to support the UK labour force, both for reskilling and upskilling the existing workforce and embedding the requisite skills in people entering the labour market.
Well-judged interventions in skills, capital allowances and the overall UK narrative can bring huge benefits to the UK’s industrial digital capabilities. Government policy should focus on these areas and always aim to be embracing the future.
This can be achieved in three ways. First, via a high-profile campaign, supported by senior politicians, promoting the need to increase automation adoption and the benefits that will result. Second, by providing a financial support package to subsidise the provision of independent support and advice to companies for the development, specification and procurement of automation solutions.
Third, by providing financial incentives specifically aimed at encouraging investment in automation. This might be achieved via a repackaging of the Annual Investment Allowance or R&D tax credits, but a more direct approach would provide greater impact.
It is important the financial support together with the promotional campaign are elements of a dedicated and coordinated programme to revitalise UK manufacturing and promote the importance of a strong manufacturing sector.
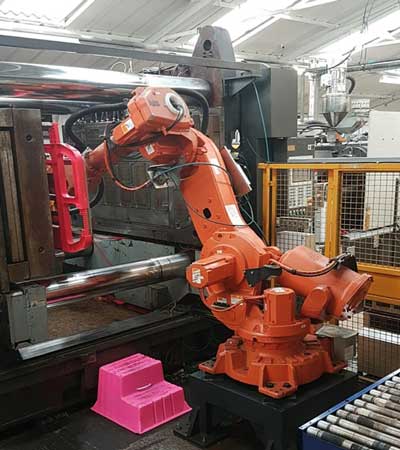
Conclusion
The Made Smarter Review [12] found that industrial digitalisation could be worth as much as £455bn to Britain’s manufacturers over the next decade. If its recommendations are implemented in full, the UK manufacturing sector could grow at up to 3% per year and create 175,000 new jobs.
The application of robot solutions also provides the agility to achieve the goal of mass customisation. Cost-efficient operations no longer require mass production in large factories, often located in lower cost labour countries. Much smaller local operations with the capability and flexibility to meet local needs can also be cost-efficient. For example, robots are being used in one factory to cut out customised flip-flops based on a 3D laser scan of the customer’s feet [13]. This level of personalisation would not be feasible without advances in automation technologies. Being local, the factory is not only more responsive to customer requirements but it is not affected by issues that may arise in other parts of the world.
As stated by McKinsey [2] automation leads to cheaper and higher quality goods as well as a rising standard of living. In addition to the social benefits of a healthy manufacturing industry providing employment and tax revenue, automation offers broader societal benefits of greater efficiency in resource and energy use and reduced carbon dioxide emissions. Productivity and efficiency improvements drive down manufacturing costs and enable lower consumer prices for goods, and resilience of supply. In addition, automation can lead to improved product quality, hygiene, traceability and reduced lead times.
More recently, significant government support has been promised for UK companies during the coronavirus pandemic. This may not herald a period of much stronger government intervention, but it could start a partnership between government and industry – a true cooperation for the benefit of both the economy and the people of this country.
The increased use of robot automation should not be seen as a threat to jobs. This is about building a strong manufacturing sector which is truly competitive on a global basis and therefore provides stable employment in roles which are both interesting and challenging. It is about achieving the benefits outlined above for the workers, the consumers and the country as a whole.
If the UK can achieve this objective it will build a future manufacturing sector which provides a strong contribution to the UK economy and well-paid employment for generations to come.
References
[1] Graetz, Georg, and Guy Michaels. 2015. Robots at Work. Centre for Economic Performance
[2] McKinsey Global Institute. 2017. “A Future That Works: Automation,
Employment and Productivity.”
[3] International Federation of Robotics. 2020. World Robotics 2020 – Industrial Robots. International Federation of Robotics
[4] Reshoring Initiative. 2015. “Reshoring Initiative Data Report 2015.” reshorenow.org. Accessed February 02, 2017. http://reshorenow.org/content/ pdf/2015_Data_Summary.pdf).
[5] European Commission. 2015. Analysis of the impact of robotic systems on employment in the European Union. Luxembourg: Publications Office of the European Union
[6] Zierahn, Ulrich, Terry Gregory, and Melanie Arntz. 2016. Racing With or Against the Machine? Evidence from Europe. Discussion Paper No. 16-053, ZEW Centre for European Economic Research
[7] Cowen, Tyler. 2016. Economic Development in an ‘Average is Over’ World. George Martin University
[8] Arntz, Melanie, Terry Gregory, and Ulrich Zierahn. 2016. The Risk of Automation for Jobs in OECD Countries: A Comparative Analysis. OECD Social, Employment and Migration Working Paper No. 189, Paris: OECD Publishing
[9] Bessen, James. 2016. How Computer Automation Affects Occupations: Technology, jobs, and skills. Law & Economics Working Paper No. 15-49, Boston University School of Law
[10] World Economic Forum. 2016. The Future of Jobs: Employment, Skill and Workforce Strategy for the Fourth Industrial Revolution. Global Challenge Report, World Economic Forum
[11] Deloitte LLP. 2015. From Brawn to Brains: The Impact of Technology on Jobs in the UK. Deloitte LLP
[12] Made Smarter Review 2017
[13] International Federation of Robotics. 2016. World Robotics Industrial Robots 2016. International Federation of Robotics
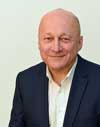
Mike Wilson
Chairman – British Automation and Robot Association Chief AutomationOfficer – The Manufacturing Technology Centre