In chemical and process plants where many items of equipment are duplicated, the performance of an individual asset is not the whole story. This is where Overall Plant Effectiveness comes in, says IBM associate partner Debajyoti Chakraborty
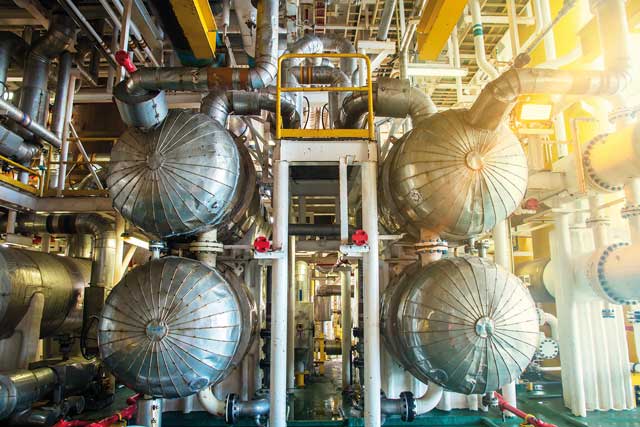
In its long history, Enterprise asset management (EAM) has never seen the exponential advances in technology around it as have been happening since the last decade.
Industry 4.0 has brought operational data to the EAM system. Big Data analytics allowed insights to be extracted from the engineering system, from geographic information, historic weather patterns, and semi-structured or unstructured information such as logs, reports and so on to make better decisions.
The next technology explosion for asset management is just around the corner. Edge computing and 5G technology are processing real time data much quicker than before. At the same time Industry 5.0 is making human-robot collaboration a reality, which in turn will allow engineers to make quicker and more accurate decisions from the real-time analytics.
One of the biggest cultural changes influenced by these advances is to bring production operations and asset management teams closer than ever before. Maintenance and reliability engineers are now able to view end-to-end performance rather than the behaviour of individual assets. This provides a new opportunity to link asset performance to Overall Plant Effectiveness (OPE), not just to the Overall Equipment Effectiveness (OEE).
OEE, measured as throughput ~ availability ~ quality, is one of the best-known approaches for measuring asset effectiveness. OEE is appropriate when the performance of an isolated asset is important; OPE, though measured with the same dimensions, is more relevant when a set of connected assets support the production operation.
Where OPE applies
In industries such as mining or construction, the health of individual items of equipment (or assets) is key. Operational efficiency is often directly linked to the performance and availability of several stand-alone assets. OEE perfectly fits these sectors.
However, in the process industry, from steel manufacturing to chemicals and petroleum processing, operational efficiency depends on the performance of a series of interconnected assets, and OPE is a more appropriate measure.
The benefit is huge. An OPE-focused approach takes a section of a plant’s operation into consideration. It enables the production operation team to understand whether an asset’s performance could influence another connected asset’s behaviour. Similarly, the asset management team is able to predict if the slow deviation of multiple connected assets could create process abnormalities and affect quality, among other possible undesirable outcomes.
Imagine that in a chemical plant, the heat transfer efficiency of a shell and tube heat exchanger is slowly reducing due to the cooling water’s increasing turbidity. Simultaneously a catalyst injection pump has started injecting less catalyst due to a leaky plunger. Both assets could still operate within their design service levels without raising any alarms, but the combined effect could affect finished product quality. The OEE of the individual assets remains as it was, but the plant OPE is affected.
Consider another situation where the opposite happens. More than 80% of process plant assets have a standby. These assets are periodically interchanged so that their cumulative operating hours are roughly equalised. If one such asset, for example a cooling water circulation pump, fails, the standby asset takes over, and the plant availability remains unaffected. Even though OEE of the failed asset is now zero because of its unavailability and engineers rush to fi x it quickly, hardly anything happens to the plant operation; in other word, OPE is not affected.
Measuring OPE
Measuring both OEE and OPE and maintaining these at high level are important for all.
However, measuring and managing OPE are relatively difficult. Whereas availability or throughput of a pump or compressor are straightforward to measure, the potential impact on quality of the interconnected asset system’s performance is not. This requires the ability to measure performance of the connected asset system. At times, external factors could also affect the performance of the asset system and plant operation. Quality issues such as sticker defects in steel or a high percentage of sulphur in aviation fuel could occur for many reasons, including the service level deviation of multiple connected assets, raw material properties, weather fluctuations, improper production planning, a manual error or a combination of several of these factors.
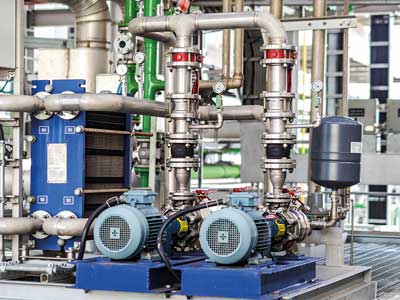
Measurement of OPE also assumes the responsibility of managing the target OPE of a plant. This requires the capability of drilling down from the plant level performance to the factors influencing a poor OPE.
Hence measuring and managing OPE needs sophisticated technology to ingest data from multiple sources, strong domain skills to incorporate possible causes of potential OPE fluctuations and robust analytics to spot anomalies at asset system level and also at the individual asset levels. Algorithms to measure OPE could also need to consider causes external to the asset performance.
Now this is possible. Real or near real time sensor data and edge analytics enable reliability engineers to track individual assets’ serviceability deviations, the corresponding impact on other connected assets and finally the plant’s availability, throughput and product quality.
A fresh approach, such as IBM’s new reliability management framework “S-DAM” (Serviceability Driven Asset Management), enables OPE to be tracked at plant level while also providing the capability to drill down to measure OEE of an individual asset.
The technology is powerful, but it is not enough on its own. Reliability engineers are responsible for driving this change. However, they need support and commitment from the production operations, engineering and project teams and to convince the maintenance teams. The ability to exploit technology still requires leadership, and the leaders of organisations must empower reliability engineers to act so that the change can happen.
Further info: deb.chakraborty@uk.ibm.com
https://www.linkedin.com/in/debchakraborty1/