When it expanded operations to a second factory in Romania, Universal Alloy Corporation turned to heat transfer specialist Fulton for the supply and commissioning of steam boilers. Fulton national consultant specialist Leigh Bryan reports.
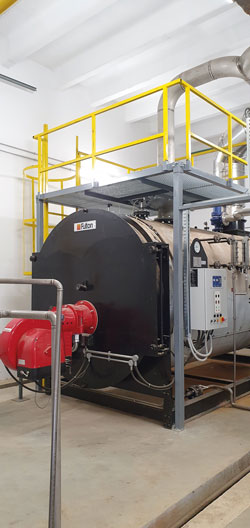
Romania-based Universal Alloy Corporation (UAC) is a manufacturer and fabricator of high-strength, hard alloy extrusions for aircraft structures or any application where precision-engineered products are critical. When it expanded operations to an all-new plant built to cope with increased demand from the airline industry, a requirement arose for new steam boilers with increased capacity, higher efficiency and more eco-friendly emissions.
The company turned to heat transfer specialist Fulton to undertake its second installation for UAC in Romania and the third across UAC’s sites in Europe and Vietnam.
In accordance with strict Romanian regulations on the installation of new plant and equipment, including steam boilers, as the original equipment manufacturer Fulton had to be in attendance at the system testing stage. This also ensured reliable, maintainable steam could be provided, prior to a planned visit by several prestigious UAC customers. Fulton’s engineering services supplied staff from the UK and, in line with current COVID-19 guidelines, on their return the engineers had to self-isolate for two weeks following the test-fire visit.
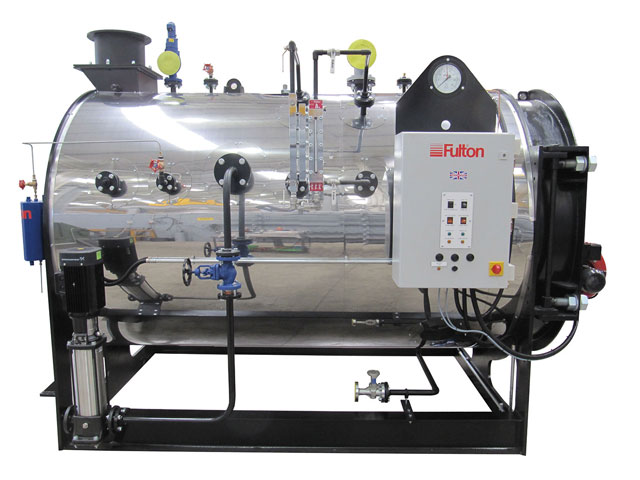
Fulton supplied two RBC horizontal steam boilers. Under normal operating conditions, the two boilers are set up for N+1 redundancy, in which at any time one boiler is in operation and the other is available as backup.
The steam is used to heat water in several large vessels via coils, with the water being used for quenching during component processing. Steam is also passed through coils for a heater-dryer system at the end of the same processing line.
For the steam boilers supplied to UAC, Fulton worked with renowned burner manufacturer Weishaupt and supplied the RBCs with two low-NOx, fully-modulating burners. It reconfigured the boiler steam outlet nozzles to run at just 2 bar. The use of a Siemens high integrity digital burner management system means the boilers are capable of achieving at least 7:1 turndown, something not always achievable from large horizontal firetube boilers.
In contrast to typical gas pressures in the UK of approximately 20 mbar, or 60 mbar on the continent, the supply at UAC’s site in Romania was 1.6 bar, so Fulton and Weishaupt provided an overprotection rig for the gas components in the gas train. Though the gas supply to the gas train is now regulated to 95 millibar, the over-protection rig operates a slam-shut system should the gas pressure exceed 180 millibar, completely preventing any possible component damage.
In addition to November’s test-firing visit, two Fulton engineers visited Romania in September to service the RBC boiler at UAC’s original factory and to commission the two boilers at the new plant. Again, both engineers followed COVID-19 guidelines on self-isolating on returning to the UK.
Both visits provided an opportunity to train key boiler operators at UAC’s new manufacturing plant. As well as receiving the usual instruction and guidance, the operators were educated on the start-up procedures in both low fire hold and auto-modulation modes for these particular boilers.
Offering higher capacities than the 2500 kg/h maximum for its VSRT range of vertical boilers, with outputs to 4787 kg/h and a maximum working pressure of 10.34 bar, Fulton’s RBC range can be specified with matched multi-stage oil, modulating gas or dual-fuel burners as standard, with other burners available on request. The boilers are constructed to BS12953, meet current and anticipated legislation and have been engineered to provide a substantial performance margin.
Further information: +44 (0)117 972 3322
email sales@fulton.co.uk | www.fulton.co.uk.