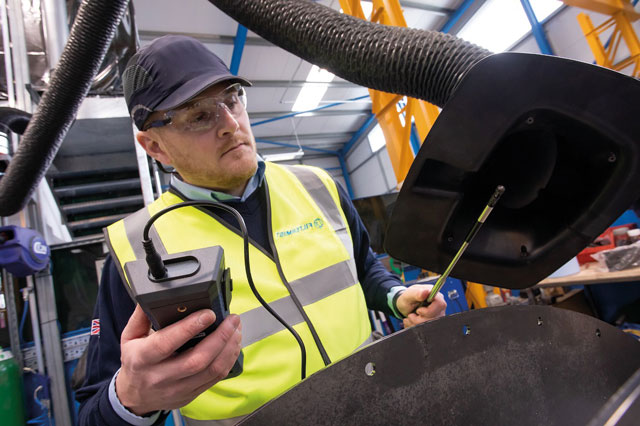
Effective local exhaust ventilation removes contaminated air from metalworking processes at source, but regular tests are required to make sure it is operating correctly, says Carl Latham, Filtermist Systems divisional sales director (aftersales).
The Health and Safety Executive’s current Manufacturing Sector Plan includes an inspection programme targeting fabricated metal premises in a bid to reduce incidents of occupational lung disease.
The recently published Health and Safety at Work: Summary Statistics for Great Britain 2020 states that there are still approximately 12,000 deaths from lung disease every year which are attributed to past exposure at work. In manufacturing industry, significant causes of work-related respiratory disease are exposure to metalworking fluids (MWFs) and welding fumes. Mild steel welding fumes were reclassified as a carcinogen in February 2019, and airborne MWF particles can cause a range of illnesses including occupational hypersensitivity pneumonitis (also known as allergic extrinsic alveolitis) and occupational asthma.
Employers have a legal responsibility under the Control of Substances Hazardous to Health Regulations 2002 to protect employees from exposure to any substance considered hazardous to health. The HSE generally recommends using local exhaust ventilation (LEV) on all CNC machine tools as the most effective way of controlling contaminated air at source.
LEV systems capture, contain and treat air contaminated with oil mist, fume, smoke and dust at source before it can escape into the wider working environment. The term “LEV” means a system that includes a hood (or multiple hoods), ducting, a filter, a fan and a discharge mechanism.
LEV TExT reports
For employers who have installed LEV systems on their machine tools, COSHH regulations require thorough examination and testing (TExT) at least once every 14 months by a competent person. Some applications require more frequent testing – these include processes in which blasting is carried out in or incidental to the cleaning of metal castings, which require testing once a month, and processes giving off dust or fume in which non-ferrous metal castings are produced, which require TExTs once every six months. Full details can be found in HSE publication HSG258 – Controlling Airborne Contaminants at Work.
COSHH Regulation 9.4 states that in addition to regular testing, “every employer shall keep a suitable record of the examinations and tests… and of repairs carried out as a result” and that records shall be kept available for five years.
The HSE recommends including a wide range of information in LEV test reports to provide a comprehensive record of both the LEV system and the examination results. This seems like common sense, but Filtermist still hears from customers who have been given a one-page summary. This is all very well until there is a problem and it proves difficult to cross-reference with previous results.
Ideally, LEV test reports should include the following information: an initial risk assessment; safety policy; method statement; the customer’s name and date the examination took place; the reference number for the system that the report relates to and the substance/process being controlled.
There should be a photo of the LEV system and product reference; details of the system’s intended performance; test point details including photos or schematic drawings; quantitative assessment readings and details of any repairs required. There should also be a statement of competence for the test engineer, and finally a report of observations and recommendations for improvement.
Operator checks and servicing
Employees are also required to play a part in ensuring control measures are working effectively. Operators should report any defects in the LEV system “forthwith” so that any performance issues can be addressed as quickly as possible. A visual aid such as a pressure gauge or monitoring system helps employees to fulfil this obligation. Machine operators should undertake and log daily, weekly and monthly checks. Ideally manufacturers of LEV systems should supply a user manual and LEV logbook for this purpose.
Regular servicing by experienced engineers is recommended for many LEV systems, as this allows any problems to be identified and resolved in between routine LEV tests.
No-one should contract a lung disease as a direct result of their working environment, so everyone has a role to play in ensuring the air in their workplace is clean and safe to breathe.
Filtermist provides a comprehensive, UK-wide service to assist with COSHH compliance, from site audits and LEV equipment manufacturing, to installation, commissioning and aftersales services, including routine and reactive maintenance, and LEV testing.
Further information: www.filtermist.co.uk | 01952 290500.