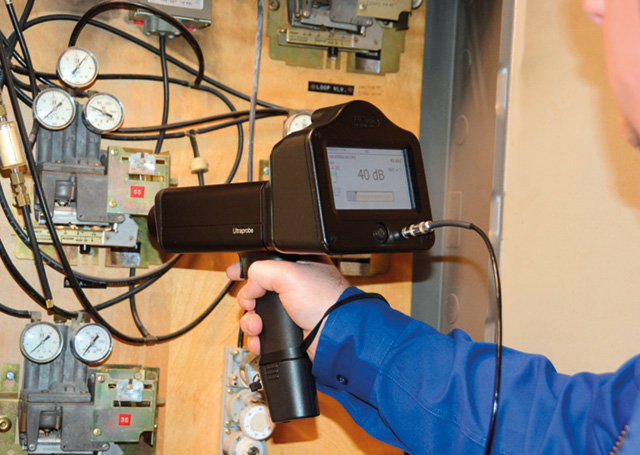
Contrary to what some might think, compressed air is not free. In fact, for what it takes to produce it, to what is generated, it is often considered the most expensive utility in a typical manufacturing facility. It is estimated that as much as 30% of the compressed air generated is lost via leaks! Christopher Hallum, UE System’s Regional Manager UK & Ireland explains.
Often, when a compressed air system struggles to meet the current demands on the system, spare compressors are rented and used as back-ups or time and effort is placed in installing an additional compressor. Both strategies are expensive.
Since compressed air systems inherently have leaks, regardless of piping, use, and design, implementing a compressed air leak management program can be an economical and effective way to improve its efficiency.
Locating compressed air with ultrasound, and then making the necessary repairs, can have tremendous payback in the money lost due to these leaks.
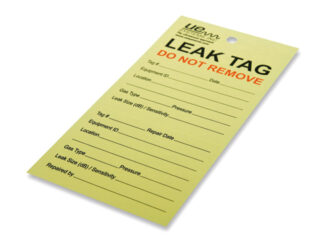
An effective ultrasonic compressed air leak survey will focus on seven key factors:
• Evaluation
• Detection
• Identification
• Tracking
• Repair
• Verification
• Re-Evaluation
By implementing these steps, a typical manufacturing plant could reduce its energy waste by roughly 10 to 20 percent.
Using Ultrasound for a Compressed Air Leak Survey
1. Select an ultrasound instrument
For ultrasonic leak detection, the suggested frequency setting is 40kHz. Then, if you wish to create a report about the detected leaks, you need a digital instrument that can display a decibel level. dB levels are the base to estimate how much a leak is costing.
2. The “Gross to Fine” Method
One thing to keep in mind is the fact that high frequency sound is very low energy. Thus, the sound will not travel through solid surfaces, but rather bounce and reflect off of them. That’s why it is important to scan in all directions with the ultrasound instrument, while adjusting the sensitivity. This will help to pinpoint the location of the compressed air leak. Once the general area of the leak has been located, use a focusing probe to pinpoint the exact location. This method is commonly referred to as the “Gross to Fine” method.
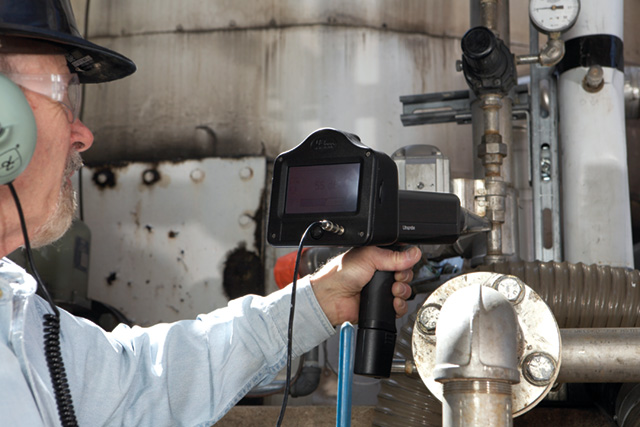
3. Creating an Inspection Route
It is recommended to perform a walk through prior to the inspection. The inspector should use this as an opportunity to determine the specific zones or areas where the compressed air is being used. Blueprints of the compressed air piping are also a handy resource. Make note of any safety hazards and any areas where accessibility may be difficult, or may require the use of ladders, extra PPE, or access to locked areas. For consistency, it is recommended to begin at the compressor, or supply side, and then move to the distribution lines, and then areas where the compressed air is being used. As the compressed air leaks are found with the ultrasound instrument, a tagging system should be in place to tag the leak at its site.
4. Documentation and Reporting
The success of a compressed air leak survey largely relies on the reporting and documentation of our findings. For documentation purposes, there is a Leak Survey App by UE Systems, available for iOS and Android. It allows the inspector to easily document the compressed air leaks, along with the associated costs. When reporting the cost and LPM (liters per minute) loss of compressed air leaks, it’s important to remember that it is an estimated cost, based off of the decibel level once the leak has been located, the cost per kilowatt hour of electricity, and the pressure at the leak site. Several independent studies have been done comparing an ultrasound leak survey report to actual energy savings, and it has been found that a leak survey is within 20% of the actual savings.
Conclusion
Compressed air is an expensive utility whose maintenance and cost is generally taken for granted. A successful compressed air leak survey depends on having the right ultrasound instrument, proper training of the personnel performing the survey, planning how it will be performed, documenting the leaks and associated costs, and initiating repairs once the leaks have been identified. Through proper documentation and reporting, an ultrasonic compressed air leak survey can show tremendous payback and energy savings.
www.uesystems.co.uk | chrish@uesystems.com |
t: +44 (0) 7930 352 188