
Remanufacturing automatic lubrication systems, rather than replacing them, could reduce the cost of maintaining wind turbines – helping them produce energy more cost-effectively, says Sian How of SKF.
Lubrication is vital to rotating machinery – especially in a system like a wind turbine. Effective lubrication helps parts to keep running as smoothly as possible, which minimises the high cost of repairs and maintenance.
Cost control helps to raise the efficiency of wind power generation, making it more competitive with other forms of energy. With this in mind, operators are keen to minimise cost wherever they can, and maximise the levelised cost of energy (LCOE).
Lube system failure
It is inevitable that parts will eventually fail – and this will often be due to the lubrication system. This could have many causes, such as contamination from dust or dirt, air entering the system or clogged lubrication points.
However, a more common reason is that the pump unit becomes worn or damaged. This usually happens because pump elements are neglected – which eventually leads to malfunction. Without a functioning pump unit, the lubrication system will not work. Pump elements are often seen as disposable because they are relatively cheap. However, this means they can be replaced cheaply – at a much lower cost than replacing an entire lubrication system.
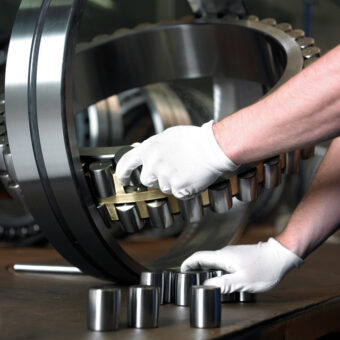
And, with an eye still on cost, failed parts can be refurbished – or remanufactured – rather than being replaced with new ones. The concept of remanufacturing is usually associated with large bearings but can also be applied to areas such as lubricant systems.
A pump part can be assessed for its level of damage and – where possible – send to a specialist remanufacturer for repair. Lubrication systems can usually be remanufactured once before they are replaced – which effectively doubles their service life.
Remanufacturers can also add further value with various aftermarket services. For instance, to avoid repeat problems, they can provide consultation, root-cause analysis of failures, corrective action plans and training. This may identify and address incorrect set-ups and practices leading to contamination, for example. Advice on condition monitoring – which can help avoid the conditions that lead to serious lubrication system failure – is also available.
Proven technique
Remanufacturing is well-proven in industry, especially for bearings. In the rail industry, for instance – which relies heavily on maintenance – remanufacturing has reduced the need to buy new components. In addition, remanufacturing helps to save energy and raw materials – which improves sustainability performance.
SKF has performed an environmental life-cycle impact comparison between new and remanufactured compact tapered roller bearings in the rail industry. The results show that remanufacturing bearings can reduce environmental impact by about two-thirds. This, on top of potential cost savings, makes remanufacturing an attractive option.
Overall, there are several benefits to remanufacturing bearings in the rail industry. These include: reduced need to purchase new components; energy and raw material savings; less waste generation; and cost saving.
The same principles apply to remanufacturing of lubrication systems. Despite the benefits, lubrication system remanufacturing is rarely used in the wind energy industry. Operators have traditionally disposed of lubrication systems when they fail, so the idea of repairing components is quite new
Cost savings
As operators look to maximise LCOE, cost saving measures become more important. For this reason, specialists are offering more extensive remanufacturing lubrication systems services. SKF recently opened a dedicated centre in the UK and has facilities across the world that can restore lubrication systems.
The savings can be substantial. While a complete lubrication system typically costs around £1,750, a new pump unit for it costs about £700. If the pump unit is remanufactured – rather than being replaced – it costs even less.
Remanufacturing helps to increase service life, raise sustainability performance and cut costs. Shifting to it will require a change in attitude, but support is available from engineering specialists and component suppliers. If applied widely, remanufacturing could help wind become the preferred source of renewable energy.
www.skf.co.uk | marketing.uk@skf.com |
t: + 44 (0)1582 490049