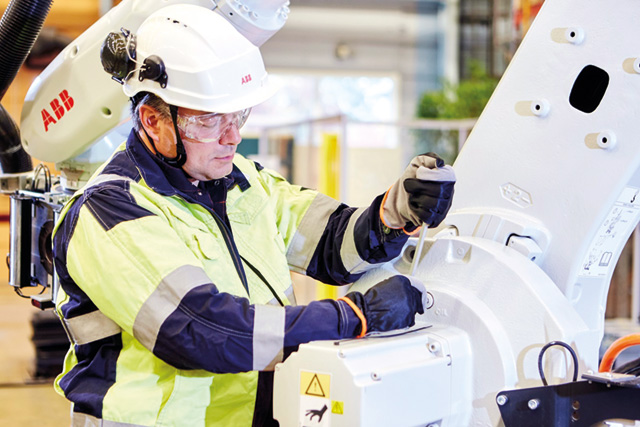
The need to keep production lines running at their optimum performance requires that the machinery and equipment used in those lines should be doing the same. Julian Ware of ABB Robotics explains how condition-based maintenance can help ensure that those robots most in need of attention on a factory floor receive the care they need to keep them in good working order.
With robots playing a vital role in a multitude of manufacturing processes, it is vital to ensure that every one deployed on a production floor is kept operating at peak condition in order to prevent disruption caused by an unexpected failure.
There are many factors that can affect the performance of a robot on the factory floor.
One is age. The long lifespan of industrial robots means that some of the units being used on production lines are getting older. Understandably, manufacturers would like to extend their lifetime rather than replace large numbers of robots.
Another factor is the need to avoid long MTTR (Mean Time Til Repair) periods – if the spare part is not on site, delays can be incurred while the part is ordered and delivered. The need to cover ’what if’ scenarios can also make it difficult to know how many spare parts to purchase.
A third factor is the way robots are programmed and used. Factors such as incorrect usage, wrongly defined loads, high energy collisions, oil contamination or late oil change can all contribute to reducing the lifetime of the gearbox and an increased risk of premature failure.
Measuring wear and tear
One area where problems can arise is the gear boxes that play a major role in the movement of a robot’s various axes. There are several issues that can reduce the life span of a compact gearbox, one of them being the duty factor. The robot’s duty factor is calculated as the time that at least one axis is moving divided by the total production time.
Previously, it has been difficult for users to determine whether key parts such as gear boxes are becoming worn or in need of replacement. The result has been that problems either go unnoticed until the robot fails or the user carries unnecessary stocks of parts or is unable to source the right parts when they are needed. This leads to disrupted production while the robot is offline.
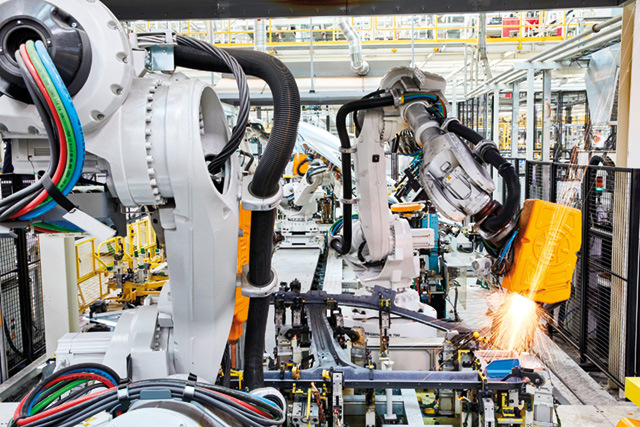
A data-based approach to maintenance
Designed for customers with large fleets of robots, developments in Condition-Based Maintenance service technologies are enabling the creation of customized preventive maintenance schedules. These can be for either individual robots or fleets of robots. Based on real-time operational data, they allow robot users to optimize productivity and minimize downtime.
Monitoring also minimizes the likelihood of premature failure and extends the Mean Time Between Failure (MTBF) rate, as well as prolonging the operational life of the robot.
Insights maximize performance
By providing up-to-the-minute information on robot status, CBM technologies enable users to gain the insights they need to create a preventive maintenance schedule to help keep robots in good working order and to help maximize performance. Users can see whether any remedial action is required, such as a repair or the replacement of any affected parts.
This allows spare parts to be purchased at the right time, ensuring they are available but not taking up capital and space by being held in stock for extended periods. As well as better budget management, users can ensure they have the correct resources on hand and can plan in advance when the repair needs to be performed, reducing the risk of unplanned downtime.
By making maintenance and repair more predictable, conditionbased maintenance helps plants eliminate unexpected robot downtime caused by failures or delays in obtaining spare parts.
Keeping on the road to improvement
Ensuring that robots continue to work for the maximum amount of time is key to maintaining the flexibility and productivity demanded by manufacturing plants – condition-based maintenance is a vital tool in ensuring that manufacturers can achieve this and stay competitive.
www.abb.com/robotics | robotics@gb.abb.com |
t: 01908 350300