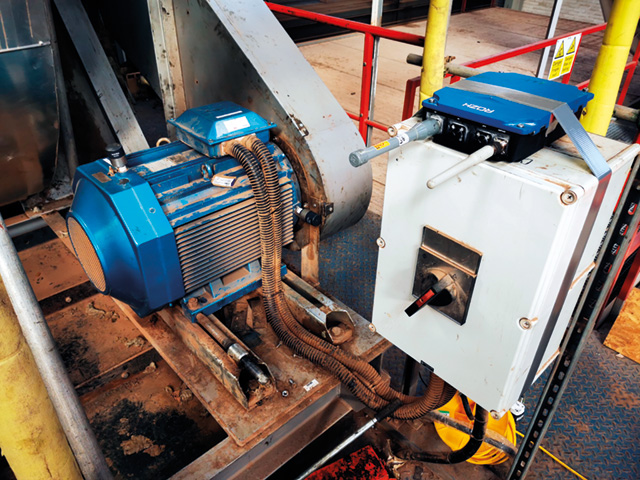
Jason Tweedy, Head of Condition Monitoring at Brammer Buck & Hickman, explains why vibration analysis is increasingly regarded as business critical. As well as predicting the need for replacing parts, shoddy repair work can also be spotted.
Analysing machinery for vibration is becoming increasingly popular as it allows early detection of wear, fatigue and failure in rotating machinery. That’s because vibration occurs in all rotational assets, but generally highlights an issue discovered by higher readings and particular frequencies, mostly as the result of wear and tear but also as a consequence of poor maintenance practices.
Vibration builds and leads to equipment failure. A wide range of components and machinery are impacted by vibration, with some of the most common being bearings and gearboxes. Vibration Analysis identifies potential problems and a predicted time to failure (in some cases up to one year in advance of equipment failure!) to enable you to get the replacement part in stock and schedule proactive maintenance, thereby reducing unexpected downtime.
Furthermore, Vibration Analysis saves money on repairs and maintenance, so works out to be a good investment. This can be clearly seen with a client of ours who was replacing all the bearings on a particular machine every month as they couldn’t afford to have that machine fail. We implemented a Vibration Analysis service with them which has stopped this expensive practice. Instead, we are able to identify which bearings need to be replaced. At the same time, we directed that customer to a number of issues that they weren’t aware of, allowing them to take proactive action.
In-house or outsource?
Whilst you can buy relatively inexpensive monitoring equipment to undertake vibration analysis in-house, your staff will need to know how to effectively use that equipment, understand the data and interpret it into meaningful action. This is why many companies now outsource Vibration Analysis to a specialist company.
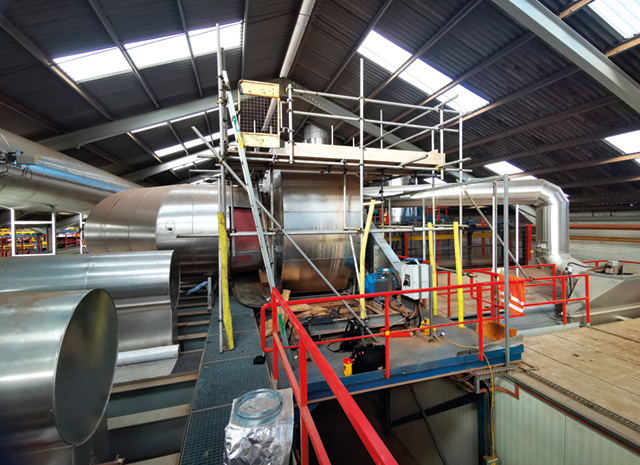
If you outsource, you can expect a typical analysis to take around three days. The engineers will measure the absolute and relative vibration on your machinery and compare it with your historical baseline data. The report supplied should detail the findings for each of your assets, along with clear photographs, and a remedial list of actions required to remedy any faults.
This analysis should be repeated regularly, depending on your site and processes.
Vibration analysis delivering results
It’s not just ageing or worn parts that can be identified by Vibration Analysis. One customer uses our Vibration Analysis service to firstly identify potential issues during the bi-annual shutdowns for repair and major maintenance. Then we return after the repair work has been done to ensure it has been carried out correctly. We’ve been able to identify some poor repair work, which would have reduced the life of the component part and led to unnecessary downtime, enabling it to be remedied before the site returned to production.
Similarly, we were asked by a brick manufacturer to look at a repair done on a critical fan used to regulate the kiln temperature. The Vibration Analysis showed the repaired fan was actually worse than when initially removed, with a catalogue of mistakes identified. Ultimately the customer decided to buy a new fan, but this was on a long lead time so, in the meantime, we helped to make the existing fan work until the new one arrived.
We also installed a temporary wireless Vibration Analysis unit to monitor severe fluctuations in the fan, so they could be caught before breaking the fan beyond repair. The Vibration Analysis service and the work we carried out prevented the site from closing, which would have been hugely costly.
Condition monitoring in all its forms has seen a significant uptake over the past decade, with vibration monitoring and analysis gaining greater traction. Manufacturing, engineering and processing sites are seeing genuine benefits and in many instances Vibration Analysis is becoming business critical.
https://uk.rubix.com/en/service/condition-monitoring |
engineering@bbh-rubix.com| t: : 0870 240 2100