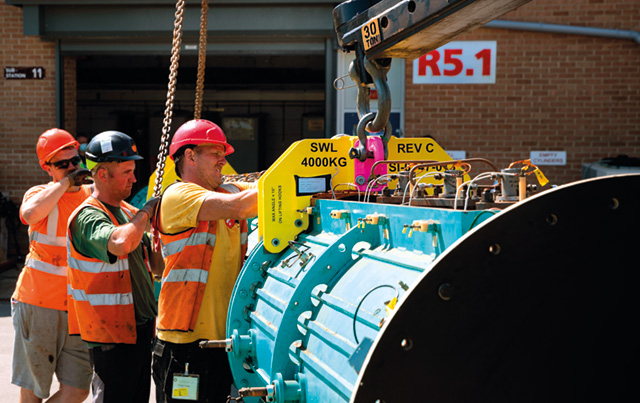
ABSTRACT
At a world leading Oxfordshire research facility maintenance of a particle accelerator that makes neutrons and muons occurs against a radioactive background, so must be an organised and optimised affair.
Maintenance is a crucial part of the unique research effort involving thousands of research scientists and engineers that aims to produce the materials of the future and deliver wide ranging benefits such as a potentially net-zero National Grid.
The engineers involved are at the cusp of the next generation of computer aided maintenance, explain Accelerator Design Group Leader Galen Aymar and Mike Glover, Electrical Systems Division Head, ISIS Neutron and Muon Source at the STFC Rutherford Appleton Laboratory.
Introduction
Society’s biggest challenges can be hard to predict, but when they do arise, expert analysis is crucial to getting the upper hand. Just like a better telescope enables you to see in more detail, we not only need to develop, but also maintain the equipment that will help to find the answers to new questions we’ve not faced before. Those at the ISIS Neutron and Muon Source confront this very challenge – and it’s a particularly exciting and complex endeavour because of the unique research that takes place at the facility.
A world-leading facility for research
The ISIS Neutron and Muon Source, based at the STFC Rutherford Appleton Laboratory in Oxfordshire, is a world-leading facility defining the materials that will shape our society and economy for decades to come. It supports a national and international community of more than 4000 scientists who use the facility’s particle accelerator for research in physics, chemistry, materials science, geology, engineering and biology.
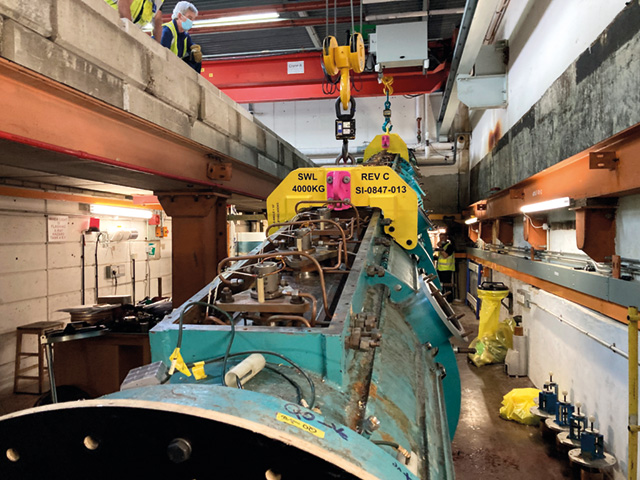
tank in one piece was only just feasible, and the weight of the tank was close to the limit of the current crane
At the facility, beams of neutrons and muons created using the accelerator are fed into a suite of cutting-edge instruments. In a similar way to how we can see things through a microscope because of how light interacts with it, our researchers observe how neutrons and muons interact with materials. This provides them with important information about processes that occur at the atomic level.
As the complexities of human society and human science become more and more intertwined it is important that the UK has the tools to stay ahead. We support researchers from both industry and academia, who come to the facility to employ a range of techniques to explore the materials of batteries for electric cars, chemicals for detergents and shampoos, and even the inner workings of a virus, to name but a few.
Time is invaluable at such a facility like ours; we are active 24/7, continually providing the tools for investigation. As a result, we are constantly working against the clock. Like any large research facility, thousands of researchers apply for time to use our beamlines annually, some of whom have even planned their experiments years ahead. Our role in maintenance is to ensure that their experiments can run smoothly and successfully, so they get the most out of their time at the facility.
With this in mind, most of our maintenance must be completed while parts of the facility are still in operation, and any downtime must be minimised wherever possible. In the unlikely event of the full stoppage of a particle beamline, it could take up to five days to get back up and running. This not only means lost time for experiments, but also wasted energy. Maintenance must be an optimised and organised affair.
Maintaining a machine that makes neutrons and muons
There are three main parts of the facility that must be taken into account when considering maintenance at the ISIS Neutron and Muon Source: the particle accelerator, the targets that particles hit to create the neutrons and muons, and the instruments used for research.
To create neutrons, high energy protons, accelerated by the particle accelerator, are aimed at a tungsten target to generate an intense beam of neutrons. These neutrons are slowed to optimal speeds using a series of moderators, and then directed to a suite of neutron instruments, each optimised to explore the different properties of those materials. A small fraction of these protons also interact with a carbon target, creating pions which decay into muons and are likewise directed to a suite of muon instruments.
These conditions are therefore naturally radioactive, producing an added layer of risk management to the maintenance work we would look to conduct. It means that in many cases we are focused on reducing the amount of time a repair takes to reduce human exposure to radiation. Or we ensure we can do it while the facility is not running during a period of ‘shut down’. As a result, we need clear programmes for preventative or predictive maintenance in order to stop issues from developing before they reach the point of severe loss of function.
The process used to generate particles creates a large amount of heat, and cooling is an essential part of the particle acceleration process. Many parts are surrounded by watercooling systems for instance. At the same time, such a high throughput of water means that the erosion of parts is commonplace, and clogs caused by impurities reacting with water can also easily occur. These extremes are necessary to the continued function of the particle accelerators, but bring with them complicated maintenance issues that the engineers here tackle on a daily basis.
Access is an even greater challenge in many cases. Certain parts have short lifetimes that need replacing or maintaining often, and others can operate for decades before needing service. But those that are in hard-to-reach places can cause disruption to research. The muon collimator, for example, is fitted in a part of the beamline that is highly radioactive and incredibly small, smaller than the average width of a human arm.
Therefore, repairing a water leak that may occur from the cooling system is made doubly difficult and often requires a total shutdown of the system. Fortunately for the muon collimator, this has only happened once after almost 30 years of use!
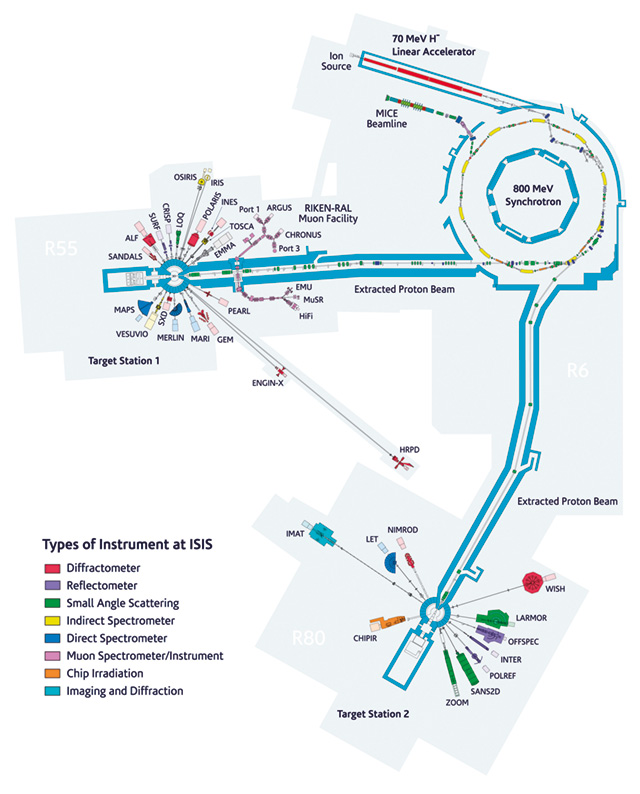
One method that helps us to maintain the facility, and prevent a full shut down, is to use our beamlines as diagnostic tools. In the accelerator we have the proton beam which goes to several target locations every 20 milliseconds. Our diagnostics tools monitor changes to the characteristics of the proton beam, alerting our engineers as to when a part might need investigation and maintenance.
This could include the detection of a change in the current, or increased radiation in certain areas – a sign that part or all of the proton beam has been disturbed. A change in the intensity or shape of the beam implies that we need to revisit the positioning of the magnets, which impacts on how they focus the beam.
Similarly, trips in our neutron beamlines can be easily identified by the extremely precise instruments on the end, which are carefully monitored by scientists as they conduct their work. We also use systems that monitor the vibration of a particular instrument using the neutrons and confirm that it is performing within the expected parameters.
These measures for preventative maintenance are effective at a facility like ours because making small changes without the need for a total shutdown is core to our ongoing operations. We have to prioritise tasks and do what we can with what we can access safely.
Meeting the needs of science and the environment
The facility’s priority is to serve researchers who come to explore the inner workings of materials at an atomic scale so they can be better used by society. Keeping the neutrons and muons running requires a perpetual programme of maintenance with this aim front and centre.
So far, we have achieved a continuous function 92% of the time, which is extremely good relative to other similar scientific facilities around the world, however, there is always room for improvement, and even a small increase in this number would have wide-ranging benefits for carbon emissions, water usage and costs.
It is not easy or efficient to shut down every part of the facility when any single thing needs maintaining, but occasionally it is necessary. Typically, the facility is shut down once every six years, for a rigorous programme of maintenance, repairs, replacements and updates. This is done to achieve high levels of reliability, and during this period the facility closes for at least three months for major repairs.
We also plan a mid-cycle shutdown as part of every operational cycle, which lasts for two to six weeks. Occasionally, a one day maintenance shut down will occur to repair equipment that will not make it to the end of an operational cycle. Only equipment undergoing maintenance is switched off to allow for a quick start up, as restarting the whole facility can take up to five days and is generally avoided.
Currently, as we write this article, the facility is undergoing a long shutdown. The accelerator has been turned off and we have made progress on a range of large engineering projects, for example:
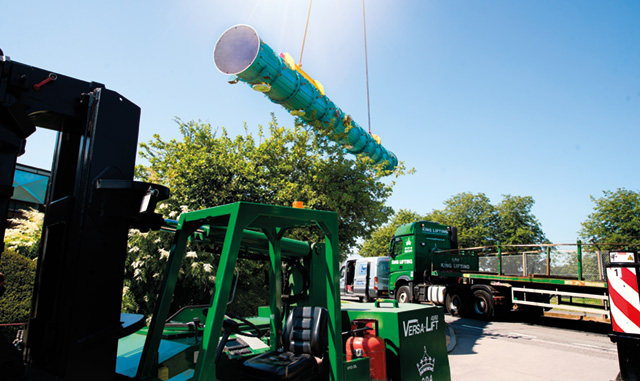
• The replacement of Tank IV, which was originally installed in 1976 and accelerates the particles in the linear accelerator while also maintaining a vacuum necessary for the particle accelerator’s normal function. Leaks in this tank had naturally weakened the vacuum, but it is inaccessible and therefore irreparable without a complete shutdown of the facility.
The only temporary fix to this problem is to increase the vacuum pumping capacity which cannot be done indefinitely. With the long shutdown, this tank could be removed and a new one installed.
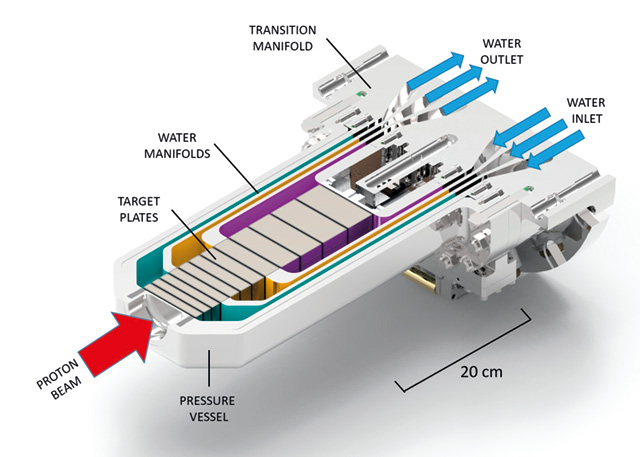
The replacement of the target in Target Station One (TS1), which had been operational for over 35 years without significant maintenance or development work. As parts of its components were radioactive, they had to be disassembled and sealed into shielded flasks before removal. The new design of the target includes improvements to its cooling systems, moderators, reflectors, and monitoring instrumentation.
Sustainability is also another focus of our maintenance plans. Electricity used by the facility generates 22,000 tonnes of CO2 equivalent per year. Particle acceleration also involves a high demand of electricity and water consumption. Reducing our carbon footprint is a goal of ours, and there is still some way to go with these aspirations.
However, thanks in part to the research conducted at this very facility, there are opportunities to be more sustainable in the future. In fact, it is estimated that while our current energy consumption from nonrenewable sources is high, the output from the science uncovered could be key to a net-zero National Grid, through finding the materials that will help us to store and create energy much more sustainably.
Maintenance is nothing without the human touch
Whilst the highly technical machinery at the ISIS Neutron and Muon Source is a crucial part of the research we are able to support, the facility would be nothing without its 400-strong community of engineers and technicians on site. The broad skillset required to run such a site is vast with people ranging from craft technicians to fully qualified chartered engineers.
Maintenance conducted at the site can be general in nature, or highly specialist, involving mechanical, electrical or even cryogenic systems that keep the facility running. Research is also undertaken at some of the highest pressures and temperatures seen on Earth, so specialists in high-energy furnaces and pressure systems hold a visible presence here.
Many of our engineers joined us at early stages in their careers, as part of degree programmes, apprenticeships or other formal schemes. They now play a crucial role in the evolution of our engineering projects, some of which span decades, nurturing them through their development into the fully-fledged research programmes we see today. We are also constantly recruiting engineers who are passionate about the work we do.
Not everyone will have the specialism required to spot an area that needs attention, or to even provide a solution, but ensuring a team of engineers with a coherent communication strategy is always on-call to assess any new issue is what makes our facility a world-leading particle accelerator.
The unique ecosystem here provides a space for engineers to solve exciting problems whilst working with hundreds of other specialists every day. While maintenance is a big part of our work here, engineers also spend their days feeding back and communicating their insights into each intimate detail of the accelerator’s inner workings. One day you might be repairing a magnet on a beamline, the next designing and building a new one to replace the older model.
Evolving to a new era of maintenance
As ISIS Neutron and Muon Source has been running for decades, the processes we have used for maintenance have evolved significantly, as you would expect. We’ve transitioned from solely working with paper, to recording on computers, and now we are at the cusp of the next generation of computer aided maintenance.
Looking to the future, we’re exploring machine learning software to monitor the lifetime of certain instruments and estimate when they will need replacing or cleaning. This has been used already in our methane moderator, a key piece of kit used to slow down the neutrons to the correct energy needed.
However, as neutrons are passed through methane, it has the side-effect of producing a substance similar to sludge, which build-ups up and eventually hinders the function of the whole beamline.
Currently, cleaning this methane moderator requires a stop to the beamline while it is warmed up, cleared, and then cooled down again. With machine learning, we can instead develop an accurate prediction of when that sludge is going to build and add foresight into our operations and ensure that all of this equipment can be cleaned with as little disruption to the facility as possible.
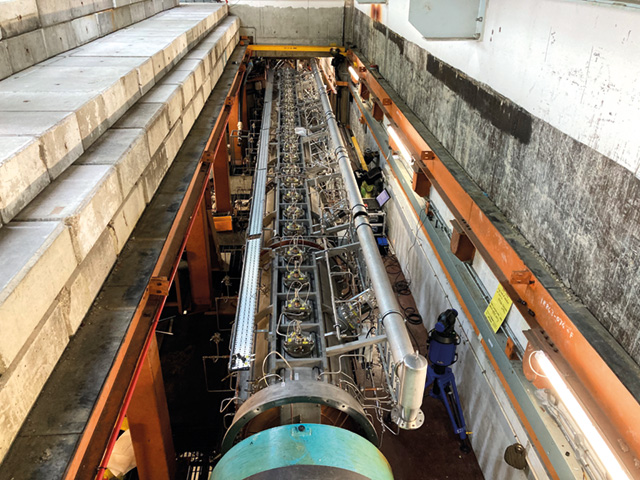
Looking forward to ISIS-II
Our experience of maintaining the current facility over its more than 30-year history has been leading towards ISIS-II, the next generation facility that will build upon the lessons of the original ISIS Neutron and Muon Source. The specifications are still being finalised, but this new facility is looking to secure higher powers, higher energies and not only maintain reliability but increase it.
Even at these beginning stages of design, our engineers are constantly thinking about how to take maintenance into account. We are in a unique position to apply the learnings we have taken with the current accelerator and apply them to our design of ISIS-II, for example, through better access and a need to reduce radiation risks in areas that need regular maintenance.
One design option that is being explored is a vertical Fixed Field Alternating (FFA) Gradient accelerator – where the particle beam spirals vertically as it accelerates. Only a handful of similar accelerators have been built over the last 30 years, but no vertical FFA has ever been fully designed and this would be the world’s first.
Although we are still undergoing feasibility studies for accelerator possibilities, it is exciting to be investigating how maintenance considerations will play out in these unique concepts, and how engineers more than 20 years down the line when ISIS-II becomes a reality will have to adapt and learn when it comes to repairing the facility.
We are also focused on how we can monitor the timelines of components in the accelerator and really consider the lifetimes, not just based on their specification, but how they will be used. For example, we may want to remove and test pieces of equipment earlier because we know that they have been fitted with insulation or sealant that could impact on performance. These are points we can pick up now, rather than wait for later.
Another exciting update we are looking to explore with ISIS-II is a digital twin system, using a virtual copy of the facility’s blueprints to help assess and plan maintenance operations before they are done in the real world.
This allows engineers to practice in a safe environment before being exposed to radiation, and therefore limit this exposure. State-of-the-art technologies such as this will ensure ISIS Neutron and Muon Source continues to be one of the most advanced facilities in the world, and experience of these new technologies is an unmissable opportunity for any trainee engineer.
The success and discovery of our search for answers to underpin what matters in the future hinges on the maintenance of our tools. At the ISIS Neutron and Muon Source, we are fortunate enough to have a dedicated and skilled team of engineers and technicians spotting problems, finding solutions, and preventing and reducing system downtime.
At the same time, we’re in the unique position to ensure maintenance is considered at every step in the plan for the next iteration of our facility. It is at the heart of the operation, and we are excited to see how developments of technology and science – from the facility or beyond – will build upon the work we have done here.
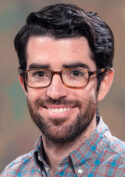
Galen Aymar
Accelerator Design Group Leader
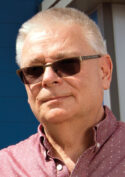
Mike Glover
Electrical Systems Division Head,
ISIS Neutron and Muon Source