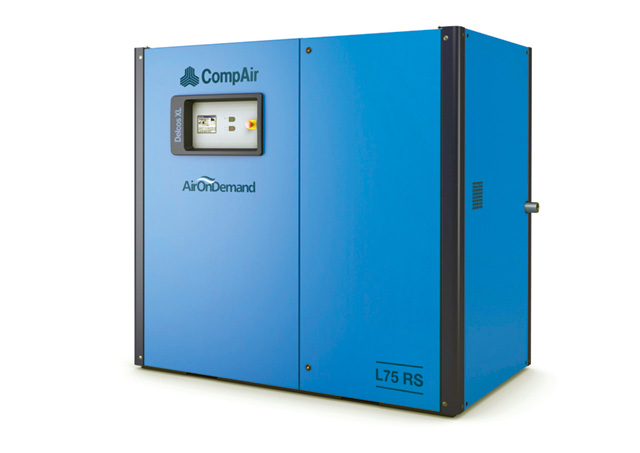
With total greenhouse gas emissions of around 700 million tonnes per year, the industrial sector is the third largest climate polluter in Europe. Here, Colin Mander, Business Line Director at CompAir, discusses how variable speed compressors can play a vital role in helping businesses meet ambitious sustainability goals.
Sustainability has become one of the leading factors for decision-makers when selecting a new air compressor. In addition to cost and performance considerations, determining a compressor’s impact on the environment is now a major consideration in the purchasing decision.
Often referred to as the fourth utility, compressed air accounts for around 10 percent of all the industrial energy consumed in Europe. An efficient compressed air system, then, can help play a larger role in contributing towards a business’s long-term sustainability ambitions. One way that this can be achieved is through variable speed technology.
Traditionally, compressors have used fixed speed motors, which means they run at a consistent speed, and produce a fixed amount of compressed air per minute, regardless of air demand. In most scenarios, it is unlikely that the exact amount of compressed air generated will be required. This means the compressor can potentially be creating compressed air that ends up being wasted.
In contrast, variable speed compressors use an intelligent drive system to constantly alter the speed of the motor and to match the air generated to the required process demand.
This technology can potentially have a big impact on businesses productivity, efficiency and sustainability levels. When compared with a fixed speed compressor, a variable speed model can achieve energy savings of up to 30 percent, and can help reduce power surges, avoiding peak currents from starting the compressor’s motor.
Furthermore, precise electrical controls ensure motors can be easily slowed down, stopped, or revved up, and the risk of leaks is minimised through the lower system pressure that is achieved with a variable speed drive. Minimising leaks in a compressed air network is another key benefit, and one of the most important energy saving measures for businesses.
The Carbon Trust reports that a 3mm hole could cost over £1,000 a year in wasted energy – not to mention the associated impact on the environment, from generating all this lost energy.
Whether you are in the food and beverage industry, automotive, medical industry or even manufacturing, there will be times when your demand for compressed air will vary. Using variable speed technology allows you to hit sustainability targets, without compromising on quality or productivity.
www.compair.com | enquiries.red@irco.com | t: +44 (0)1527 838200
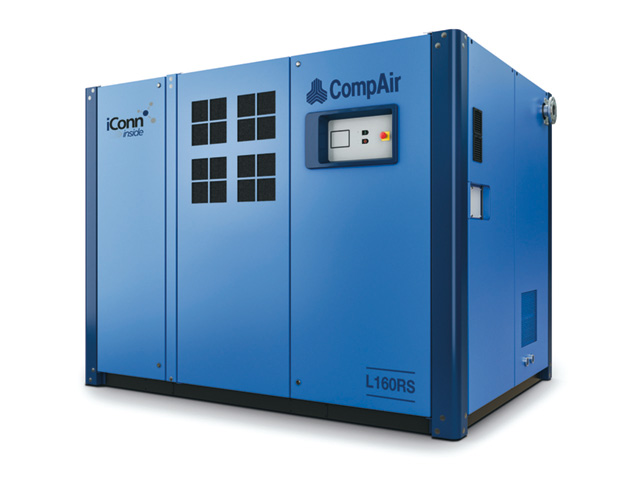
Case study
The Metal Drum Company, a manufacturer of steel drums, is saving £23,000 per annum, thanks to new, high efficiency, speed-regulated compressors from CompAir.
A long-standing customer of CompAir distributor, Air Compressors and Blowers North (ACB), the company has always relied on the efficiency and durability of CompAir machines, dating back to the early 1990s with its first Broomwade 6150e compressor.
Now, thanks to a programme of energy-efficiency improvements, The Metal Drum Company is benefitting from a new, CompAir L160 RS, variable-speed drive machine at its main Chilton site, delivering payback in just 3.5 years; alongside a smaller L75 machine, offering 3.7 years’ payback at its Hull facility.