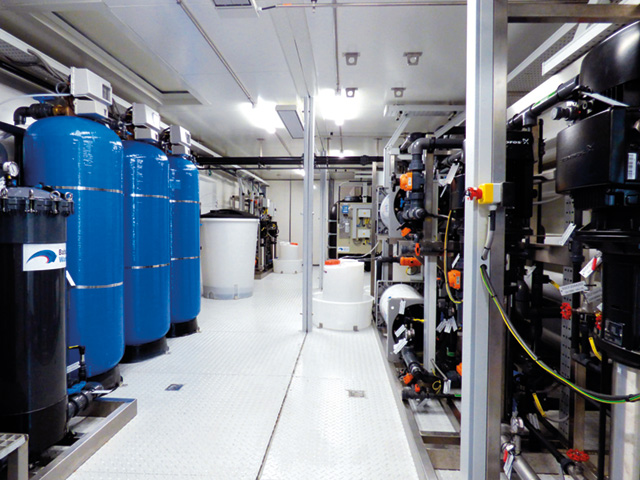
Chris Horsley, Process Engineering Director at Babcock Wanson, argues that to avoid being caught in the middle of a ‘blame game’ when something goes wrong with your boiler operation, consider employing the manufacturer directly for water treatment.
All steam raising equipment requires the feed water to be treated to prevent corrosion. Both the quality of the steam and the longevity of the boiler producing it are completely dependent upon the condition of that water feed. Poorly prepared water can cause rapid and costly damage to the heating surface and can lead to the end of a boiler’s working life in a short period of time.
In its most basic form, water treatment for steam raising boilers involves the controlled addition of a chemical oxygen scavenger, sludge conditioning and pH control correction.
Experience shows that poor husbandry is the main culprit of inadequate water treatment services. It is very important to test the feed water condition at different times of the working day and on different days of the week to glean an accurate picture. The dosing rate also needs to be adjusted if there are large variations to the temperature of the feed water and be sure to use quality treatment chemicals.
Whilst a steam boiler always requires properly treated water, this service has traditionally been supplied by a third party, independent to the equipment manufacturer. However, water treatment companies specialising in steam boiler treatment are few and far between, with the majority offering a range of water related services, with water treatment for process heating added as a bolt on service.
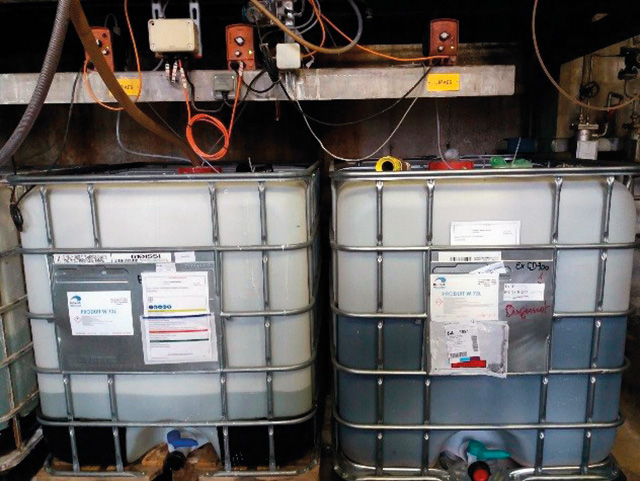
If problems do occur questions arise as to the root cause and who holds the underlying responsibility. The problem is that you’re dealing with two separate parties who won’t take responsibility for the damage to the boiler, leaving you to pay to put it right.
There’s no easy way out of the blame game for the customer.
What I can suggest instead is to avoid this potential pitfall altogether and employ the equipment manufacturer directly to undertake the water treatment instead. Not only do they have a superior understanding of the equipment which makes for a more effective, high quality water treatment service for the customer, but a single-source solution provides the customer with peace of mind and one company to deal with in the event of a fault.
Not every manufacturer will offer such a service and those that do still need to be vetted to ensure the quality of the water treatment service.
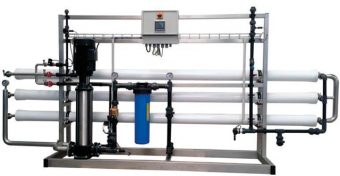
Using our in-depth knowledge of boilers, Babcock Wanson offers a comprehensive range of Water Treatment programmes for Steam Generators, which is backed-up with a 5-year corrosion warranty on the boiler coil. In the unlikely event of feed water deficiencies causing the coil to corrode within the first 5 years, we will replace it.
To provide the level of service that meets our requirements, we have established a unique and exclusive partnership with water treatment specialists Deep Water Blue. Employing highly qualified and professional chemists ensures the treatment and testing regime is completed to obtain an accurate picture of a site’s specific requirements under a variety of conditions.
Only top-grade, environmentally friendly treatment chemicals that are safe and simple to handle are used. In between scheduled consultancy visits the unique vSteam web portal allows customers to simply enter daily readings on-line and receive real-time feedback support.
At Babcock Wanson we see first-hand the effects of poor boiler water treatment and, more importantly, on our customers’ ability to run their plant effectively. We believe it’s time for the boiler manufacturers to step up and provide customers with the ongoing support they require by providing quality water treatment services and taking responsibility for what goes in, as well as what comes out, of the boiler.
www.babcock-wanson.co.uk | info@babcock-wanson.co.uk | t: 020 8953 7111