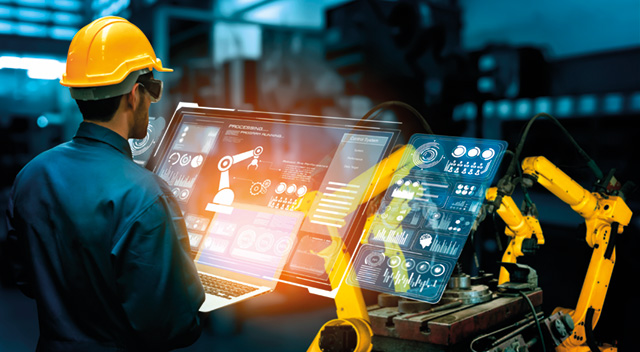
Nicola Coote, Director at Personnel Health & Safety Consultants Ltd, describes how work equipment risk assessments should be executed, and considers the implications of changes related to CE marking.
A question we are often asked as health and safety practitioners is how a work equipment risk assessment should be completed, and if there is a common standard that should be followed.
CE marking requirements to will change to UKCA in January 2023 following Brexit. The first step to this process is machinery risk assessment and engineers and manufacturers should start considering how they are going to approach their assessment and certification process now. The first step is to complete your machinery risk assessment to the required standard to identify and eliminate or manage risks identified.
Legal requirement for assessment
The general duty of care comes under Section 2(2)(a) to ensure that your plant and systems of work are safe. This is very wide-ranging and covers everything that is in your workplace, including the building, the furniture and all the equipment (generic term for “plant”).
It’s important to understand that UK health and safety legislation is based on wide-ranging objectives, rather than prescriptive requirements. So you need to consider what the law is seeking to achieve (ie, its objective) and how best you can achieve it. This pragmatic approach is sometimes what people refer to as “common sense”. The problem is that sense is not always “common”.
To help meet the objective, you should also refer to the Provision and Use of Work Equipment Regulations 1989 as they give more specific requirements that must be met. There are over 30 requirements in total, listed in five different sections depending on the type of equipment and whether it is mobile or fixed.
Machinery risk assessment
The specific requirement for risk assessment is is specified in the Management of Health and Safety at Work Regulations 1999. In order to ensure that our work equipment is suitable for the job and is safe, a risk assessment is needed to determine what could go wrong so it can be eliminated (by designing out where possible), or managed, eg by guards, isolators, cut-off switches and then maintained.
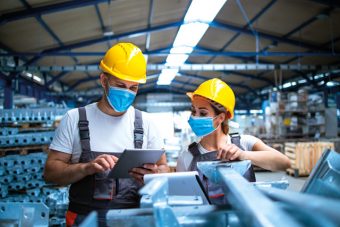
A fresh approach to assessment
Risk assessment, when done well, enables you to look with a fresh pair of eyes at your equipment and to talk to the people working with it to consider things may have never been discussed or considered previously.
When completing your risk assessment you must involve your workers as the Health and Safety Executive (HSE) are clear in their view that a risk assessment is not deemed to be valid unless it has had the input of the end user.
When the end user is involved in doing the machinery assessment it becomes an excellent tool to tease out all the “near-miss” incidents that people don’t bother to mention or raise, let alone to formally report as it is quick, easy and appropriate. And if someone suggests an improvement that can help quality, safety, environmental or efficiency of the product they become more engaged, and the equipment is also improved. A win:win outcome.
What is the correct standard of risk assessment?
If you have machinery which may need to be modified, upgraded or otherwise changed it could affect the CE marking. If you have new machinery coming onto the market you are likely to need certification to assure customers it is fit for purpose, safe and meets UK requirements for machine safely.
To do this effectively you should refer to ISO 12100:2010 “Safety of Machinery– General Principles for Design – Risk assessment and risk reduction”. This provides all the criteria that should be considered when completing your machinery risk assessment and applies to new machines coming onto market as well as those which are modified.
Your risk assessment should clearly show that it has considered the guidance within this standard and how you have eliminated or managed the risks. Your assessment will enable you to also consider minor design change features, eg if one customer wants the machine to be slightly taller, wider, and this can be completed in one assessment provided the modification does not affect the essential safety features.
The HSE has also produced a guidance document on meeting safety objectives by design and construction and can be downloaded here: www.hse.gov.uk/work-equipment-machinery/single-europeanmarket.pdf
www.phsc.co.uk | phsc@phsc.co.uk | t: 01622 717700