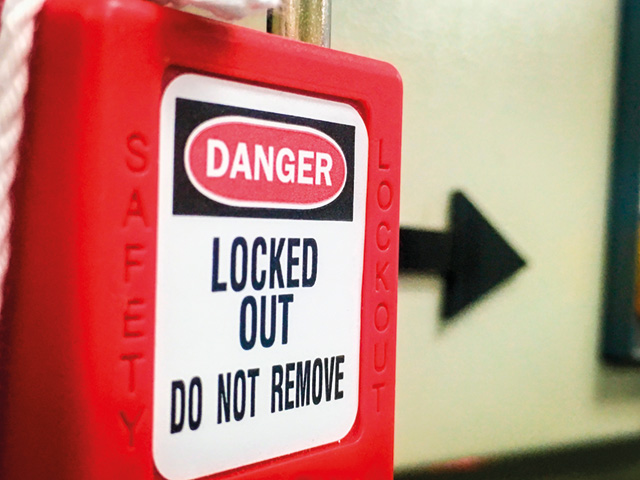
In this article, David Dearden – from leading safety specialist Euchner – examines the engineering challenges for protecting people and the machinery commonly used throughout the engineering sector.
Although not always ideal, maintenance operations often require access to dangerous parts of equipment and preventing inadvertent start-up or reducing hazards to an acceptable level needs to be considered. The Lock-Out-Tag-Out system is well established, but the long walk back to the control panel to place the padlock may provide motivation to ignore safety procedures and ‘risk-it’.
Using local interlocking devices incorporating a local padlock ‘lock-out’ facility (a number of interlocks can accommodate up to six padlocks on a single device), the likelihood of an operator sidestepping safety procedures in place is greatly reduced.
The ability to ‘lock-out’ is great when operators recognise the danger to themselves or others, but what do you do when they, or maintenance staff, try to deliberately override an interlocking system, often to make things easier for themselves?
The most common method of overriding a guarding system is using a spare actuator (key) tricking the guarding system to believe the door is closed. This is easily overcome by using RFID ‘coded’ actuators paired to the safety-switch – only one actuator can be ‘paired’ at a time and if the operator tries to use a different actuator the machine won’t run.
Euchner was responsible for developing the first RFID locking guard-switch, so knows a thing or two about preventing the defeat or manipulation of safety systems. With greater focus being placed on this subject within the relevant safety-standards, including BS EN 14119, it is vitally important all equipment manufacturers and end-users consider their existing arrangements are adequate.
Some may feel the use of electronic safety devices unsuitable for arduous applications, but these devices can handle pull-out forces up to 8KN (much more than even the strongest person could manage), often use vibration-tolerant encapsulated solidstate failsafe electronics and achieve very high ingress protection ratings, including IP65, IP67 & IP69.
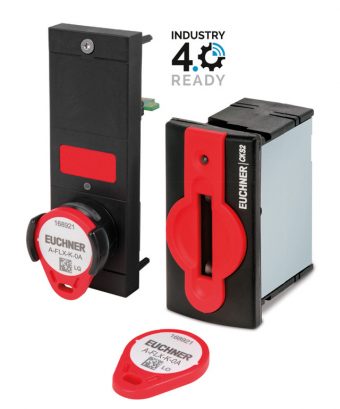
The selection of safety interlocks is only part of the story, plant and equipment used in manufacturing is often extremely dangerous and therefore the safety-related control system used to safeguard many of the dangerous parts needs to be designed to meet a high performance level and detect faults when they occur. It is no good only finding out your guard interlock has failed when the machine doesn’t stop on opening the guard door!
This is one of the most common issues Euchner encounters on site, with machinery operators not aware of their responsibilities and risk assessments that haven’t looked thoroughly enough into the safeguarding measures being provided by a particular safety control system.
Many site-based risk assessments highlight the safeguard measures fitted to a machine, such as interlocks, pull-cords, etc., but has someone actually assessed the design of the electrical control system behind the devices? The standards, including BS EN 13849-1, assist in the process of determining the Performance Level (PL) required for the control system protecting the hazard.
And while it is sometimes seen as too complex, there is plenty of help from companies, including Euchner, to assist with this much-too-often missing step. The safety manager needs to ensure that safety-related control systems have been designed and verified irrespective of how much functional testing is taking place during the working week.
The functional test often used at the start of a shift only shows the system is working at that moment in time, it doesn’t guarantee the system will operate next time it is called upon, which may be when someone’s life is depending on its operation. However, not all applications are the same, and it is always important for the correct components to be selected for any given application.
By focussing on good practice with suitable equipment, it is possible to achieve increased plant efficiency and operate a safer site, quashing the long-considered opinion that machinery safety reduces throughput – and not even considering the distressing consequences of not getting plant safety right in the first instance.
www.euchner.co.uk | joe.ardley@euchner.co.uk | t: +44 (0)114 256 0123