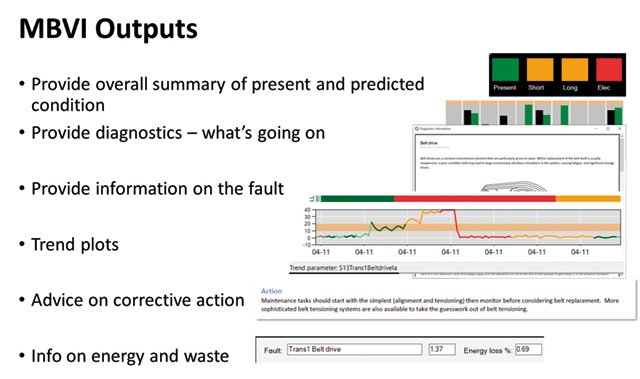
Geoff Walker of Faraday Predictive discusses how the best elements from a range of available condition monitoring technologies can be combined for better machine information.
Condition Monitoring is generally a good thing to do, helping you understand the behaviour and condition of your machines. Key benefits include the ability to be warned of developing faults in advance, to avoid unexpected breakdowns and optimise maintenance planning.
You can also diagnose what these faults are, so maintenance can be prepared and targeted at the right fix with the right spare parts and tools organised in advance – to minimise downtime during the repair work.
However the biggest benefit comes if the condition information is good enough to allow you to adopt Condition Based Maintenance as a strategy – ie. moving away from both Breakdown Maintenance and Planned Maintenance which can save your business up to 90% of the costs of maintenance and downtime.
Why am I hearing more about Condition Monitoring nowadays?
There has been something of a buzz about condition monitoring recently, with new technologies being introduced, new companies being founded and other companies being acquired by larger firms, all keen to bring this technology to a wider customer base.
There are a wide variety of technologies available for condition monitoring; Vibration Analysis (VA) has been the most common technique up to now. Although this has been in use for 40 years or more, newer aspects include the use of wireless sensors which avoid the very high cost of connecting sensors on every bearing on every machine back to a central point.
Battery life of these sensors can become an issue, but Energy Harvesting wireless sensors are able to avoid the need for batteries altogether. Other condition monitoring techniques include Ultrasound, Motion Amplification, Thermography and Motor Current methods, which in addition to condition monitoring can also bring an energy optimisation / carbon footprint angle.
In recent years, there has been an enormous amount of hype around the Industrial Internet of Things (IIoT), based on low-cost sensors communicating data via the internet. Underneath this hype, connectivity to the cloud allows data from different systems to be viewed together to give a more complete picture and permits visibility wherever you are, on your phone / PC / tablet.
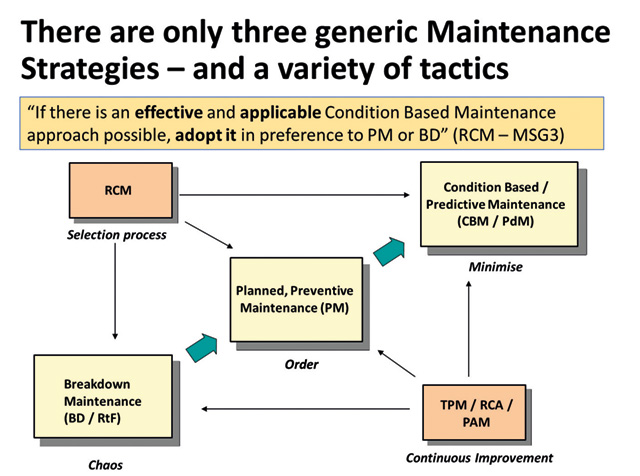
These elements are all being brought together with Artificial Intelligence / Machine Learning (AI / ML) to make sense of large volumes of data and turn them into simple conclusions and advice.
Cloud Processing runs the AI algorithms on a central server, with all the raw data communicated from sensors via internet connections – with possibly large data volumes required – while Edge Processing does this locally, reducing data volumes and hence bandwidth requirement, but with potential battery life implications.
Learning / training the algorithms can require very large volumes of data, either using historic records or taking a significant time before good results are delivered.
Combining the best elements
Model-Based Voltage and Current Analysis (MBVI) systems such as those from Faraday Predictive combine the best elements of all of these categories and provide comprehensive machine information including:
• Condition Monitoring – present and predicted status up to 3 months ahead;
• Monitoring of the entire machine – motor, transmission, driven machine, and sometimes process;
• Diagnosis of the widest range of fault types – mechanical, electrical, load, speed;
• Information on energy consumption, energy cost and energy waste;
• Flexible architecture – cloud based or local or stand-alone, avoiding comms bandwidth issues;
• Installed-in switchgear – allowing the monitoring of inaccessible machines, minimal cable runs and no issues about battery life.
So how can you evaluate which system is going to work well on your equipment? Each different manufacturer has their own approaches to this but, for example, Faraday Predictive offers a service using its portable kit, to assess the condition of a handful of machines. This provides a convincing demonstration of how well the system works on a customer’s machines.
www.faradaypredictive.com | info@faradaypredictive.com | t: +44 333 772 0748