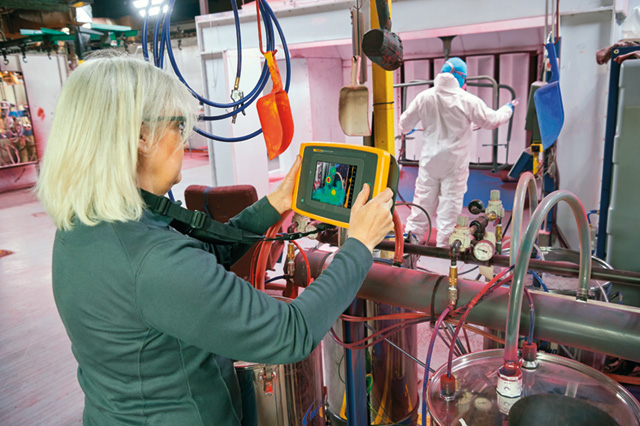
Fluke’s Senior Technical Sales Manager, Marc Sherwood, discusses the advantages of acoustic imaging to keep a handle on energy wastage and boost productivity.
Research by The Carbon Trust has found that the British manufacturing sector uses more than 10TWh of energy every year to generate compressed air. The USA’s Department of Energy has calculated that around 30% of compressed air is lost due to leakage while the British Compressed Air Society (BCAS) says that figure can be nearer to 40%-50%. That is a staggering amount of energy being wasted and a major impediment to maximising plant productivity.
As well as the cost and energy factors, irregular system pressure can affect the efficiency of air tools and other air-operated equipment in a facility. At the same time, using excess compressor capacity or increasing operating times in order to compensate for leaks can lead to unnecessarily high running costs.
Likewise, operating equipment at higher than necessary levels can increase the requirement for maintenance or repairs while cutting short the equipment’s working life.
The BCAS says that industry in general should be aiming for between 5%-10% of compressed air loss through leakage. This would certainly save a lot of money and increased productivity but the issue is, of course, how to achieve such a significant reduction.
According to Fluke, the answer is acoustic imaging. However, before we look into detail about what that approach offers, it is worth reminding ourselves of the current systems of leak detection that have clearly been failing to save manufacturers’ use of energy and to boost efficiency.
Ears, eyes and ultrasonics
An all too common method of detecting compressed air leaks involves listening for a hissing sound as air escapes. This is easier said than done in a noisy factory environment so some manufacturers have used visual cues such as bubbles coming out of pipes and hoses after putting liquid on to them.
This is almost as much a hit-and-miss method as listening for leaks, with an awful lot of effort and time wasted attempting to locate the exact (and sometimes minute) hole from where the air is escaping. If there are multiple holes, the difficulties can increase exponentially.
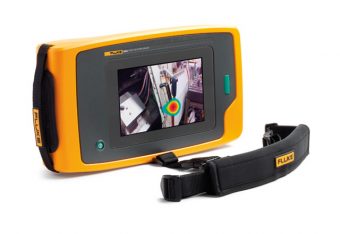
In search of a more reliable method of compressed air leak detection, industry has looked towards ultrasonic equipment that ensures distances and loud environments are less of an impediment.
The downside is that ultrasonic detection requires operators to move their scanners around almost randomly until a signal alerts them to a leak… but doesn’t tell them exactly where it is. The ultrasonic equipment is also prone to interference which can give false or inaccurate readings and the operator might have to resort to locating a leak manually, essentially defeating the object of using sophisticated and costly equipment.
Speed and accuracy
Fluke’s solution to leak detection is the ii900 Sonic Industrial Imager, a hand-held unit weighing just 1.7kg that has been designed specifically to filter out loud background noises and isolate the sound frequency of a leak. Leak location is achieved using SoundSight technology which overlays a SoundMap on a visual image and displays it on a 7” LCD touch-screen.
The built-in video camera generates a live image which is supported by 64 microphones. This combination of audible and visual signals increases speed and accuracy of leak detection by producing a heat map of ultrasonic emissions using coloured dots. Even if there are barriers in the way or the leak is in an awkward place, the ii900 imager will pinpoint the problem while eliminating issues caused by ‘reflections’ or interference from other equipment.
Not only can the operator produce a close-up of a leak – either as a video or still image – but all images can be saved and exported for subsequent reporting. The imager can also generate accurate estimates of leakage flow for working out the total cost of every leak, with an inspection team able to check a whole factory in a matter of hours. This automatically generated information is called a LeakQ report.
Eyes, ears, ultrasound and guesswork can be consigned to the past when it comes to tackling leaks in compressed air systems. Now productivity can increase and energy bills can be reduced thanks to acoustic imaging.
www.fluke.com/en-gb | iss.uk@fluke.com | t: 0207 942 0721