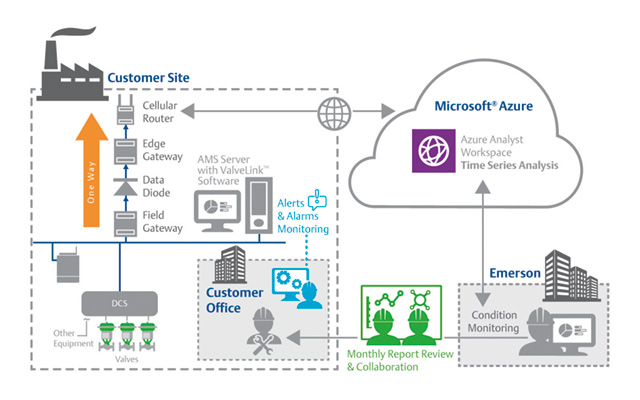
John Carlow, Business Development Manager at Emerson, explains how using third-party remote monitoring services can enable organisations to improve plant uptime and reliability, and reduce maintenance costs.
Automated valves are critical to most processes, so it is therefore commonplace for organisations to install digital positioners with advanced sensors and diagnostics on their valves to detect performance degradation well before it leads to a failure. However, these important diagnostic capabilities are often not used to their full potential.
There are several reasons for this. Sometimes, positioner diagnostics are run only when the valve is offline, which limits the opportunity to perform testing. Some plants have positioners with online diagnostic capability, but lack the resources to properly analyse the available data.
In many cases, data is reviewed only after a valve has failed. This can be helpful for troubleshooting, but using the data to predict and possibly prevent failure would have been much more effective.
Remote continuous monitoring as a service
Where plant resources are limited, third-party experts can provide remote continuous monitoring of critical automated valves as a service, taking advantage of the digital positioner diagnostics already installed in many plants. Digital controllers provide sense valve travel, drive signal, temperature, cycle count, travel deviation, supply air pressure, friction/torque, valve stroke time and other diagnostic parameters.
Through instantaneous and trended data, most developing problems can be detected before a valve fails, but the data is only useful if it is accessible by someone with the ability and time to. interpret it.
Emerson, for example, can perform scheduled online testing of valves in operation through its Fisher ValveLink software. Data is automatically gathered if the positioner detects an abnormal condition, with all the information securely transferred to Emerson for review. Data files can be emailed on a weekly basis, automatically transferred via a wireless network and a data diode, or transferred via a secure data highway and firewall set up by the end user’s IT department.
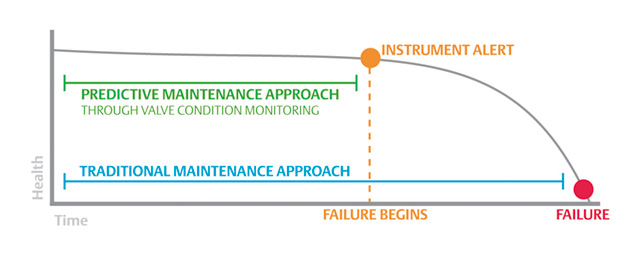
Once the diagnostic data is delivered, experts can review it via a cloud-based analytics platform. These analysts monitor both current data and historical trends to identify performance degradation or developing mechanical problems. Non-critical issues are noted in a monthly report that documents the overall health of each valve and provides recommended corrective actions. Developing issues are flagged well in advance, enabling repairs to be planned. If critical problems are detected, the end user is notified immediately so they can address the issue.
Performance declines are typically detected weeks in advance of failure, giving plant personnel enough time to plan and execute the repair. This transition from reactive to predictive maintenance improves plant uptime and profitability, while reducing repair costs, with safety improved by avoiding incidents.
Applications
Remote valve condition monitoring can benefit any plant with critical automated valves and limited resources, but there are certain applications in which it can be particularly advantageous. For example, pressure swing adsorption (PSA) units play a vital role in refinery production. These units incorporate a number of valves operating in high-temperature, high-cycle service.
Despite the severe conditions, the valves must ensure virtually zero leakage and very fast stroke times to achieve optimal service. Remote monitoring allows each valve’s performance to be constantly evaluated, with developing issues flagged early enough to avoid unplanned outages. This improved uptime translates directly into increased refinery production.
Near real-time valve condition monitoring information is also extremely useful when planning future maintenance outages. By focusing only on valves that have known problems, turnaround schedules can be shortened, with significant amounts saved on parts and labour. For example, a combined cycle power plant was overhauling every critical valve during each outage to maximise uptime upon restart.
After installing upgraded digital valve positioners and implementing diagnostic alert software, plant personnel focused their repair efforts more efficiently, saving £57,000 in one shutdown alone.
emerson.com/uk/automation | uksales@Emerson.com | t: 0870 240 1978