Synchronous reluctance (SynRM) motors are known primarily for their efficiency, and with IE5 drive and motor packages available, they are among the most efficient motors on the market. However, from a maintenance perspective, they can also add significant value for your operations. James Thomas, UK Water Industry Manager, ABB, explains why.
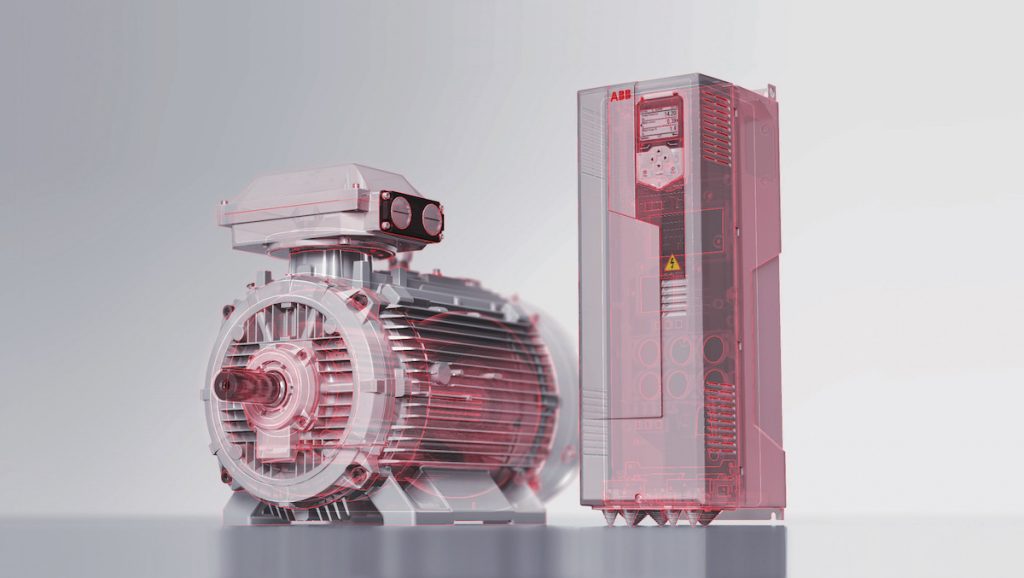
The synchronous reluctance motor (SynRM) has been around for some time, but it is only in the past couple of decades that it has really come into its own, and the technology has progressed quickly since. Today the SynRM is among the most efficient motors available. Energy efficiency is of course the SynRM’s biggest asset, but to frame the conversation primarily around efficiency is to overlook some of the motor’s soft benefits, particularly when it comes to maintaining your installed base.
You may often see it claimed that a SynRM is easy to maintain, but it is rarely explained in any depth why that actually is. In fact, a SynRM has very similar service requirements to that of a standard induction motor, and uses the same basic components. Unlike a permanent magnet motor, ABB’s SynRM contains no rare earth minerals, and so requires no specialist skills to maintain beyond that of a conventional motor. Furthermore, SynRMs use the same basic component parts (i.e. rotor and stator) as an induction motor. It has no traditional rotor windings or permanent magnets, and so there are fewer parts to go wrong.
SynRMs achieve their high efficiency levels through the use of a specially designed cageless rotor which removes traditional rotor losses, in turn helping to reduce overall losses by up to 40 percent compared to an equivalent IE3 motor, with significantly lower energy consumption and CO2 emissions. The stator is similar to that of an induction motor, with torque generated by using the principle of magnetic reluctance to pull the rotor around.
As a result, a SynRM runs more quietly than other motor types and, crucially for maintenance engineers, has a lower operating temperature, resulting in 30°C lower winding temperatures and up to 15°C lower bearing temperatures. This helps to prolong the life of bearings, which account for around 70 percent of unplanned motor outages. Regreasing intervals are also less frequent as a result, while no brush changes are needed. This means that the motor requires less maintenance in general. As well as reducing maintenance time and costs, this also reduces performance drift over time, enabling those ultra-premium efficiency levels to be preserved for as long as possible for reduced energy usage. Indeed, repairing an old IE3 motor still leaves you with IE3 efficiency performance, as well as more frequent maintenance and a higher risk of failure.
In the water industry, companies are often unaware of how simple and easy it is to upgrade their old motor assets. The efficiency savings alone of jumping from IE2 or IE3 up to IE5 can mean that a SynRM motor, when combined with a variable speed drive (VSD), can recoup its initial investment within a matter of months. When you add in the reduced maintenance costs as well, the savings can very quickly accumulate, particularly when you extrapolate across a large fleet of installed electric motors. As well as being lower maintenance, a new SynRM is also much less likely to fail compared to an older motor, leading to a much lower TOTEX cost.
Efficiency is clearly a top priority at the moment and rightly so, but this is not the only way in which significant savings can be achieved when it comes to motor-driven applications. ABB first launched its IE4 SynRM in 2011, and in 2019 introduced the IE5 SynRM ultra-premium motor, representing a major leap forward in the efficiency of electric motor technology.
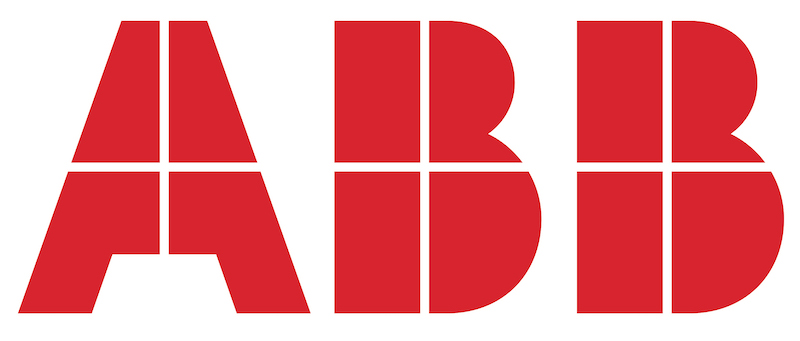
If you’d like more information about ABB’s SynRM offering, please contact james.thomas@gb.abb.com, or download the white paper here: https://bit.ly/3m9iQ9a