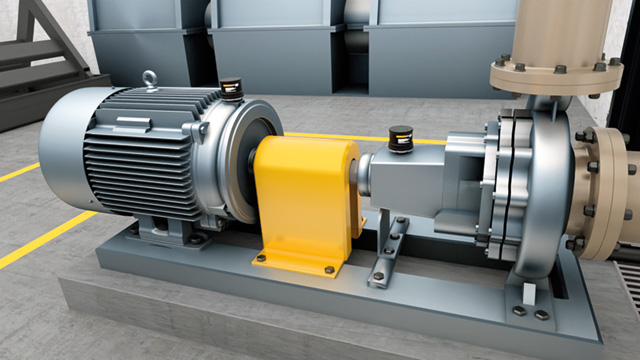
Achieving operational resilience with remote condition monitoring of assets is simpler than ever with easy to install vibration sensors, says John Bernet, a Certified Maintenance Reliability Professional and Application Specialist at Fluke Reliability.
Condition-based maintenance (CBM) is a strategy that employs sensors to detect variations in a wide range of parameters, which can include pressure, temperature or vibration of a piece of equipment, or the electrical current being drawn. This data can be accessed remotely, allowing maintenance professionals to identify variations from a normal range that may indicate the equipment requires attention.
In addition to potentially increasing operational resilience while lowering maintenance costs, increasing worker safety and enhancing workplace flexibility, the Covid-19 pandemic highlighted the importance of remote condition monitoring systems. Research by Fluke in 2020 found that, even early in the pandemic, companies were prioritising investment in data collection and remote asset monitoring.
Today’s technology and connectivity make it much easier to switch the maintenance model from reactive to predictive maintenance and benefit from CBM. Additionally, companies working to apply digital technologies into their regular maintenance practices have achieved cost savings, improved ROI, increased asset health and extended machine performance.
These factors are driving rapid adoption in a wide range of industries. Data Bridge Market Research suggests that the machine condition monitoring market in Europe will expand with a compound annual growth rate of 7.6% between 2022 and 2028.
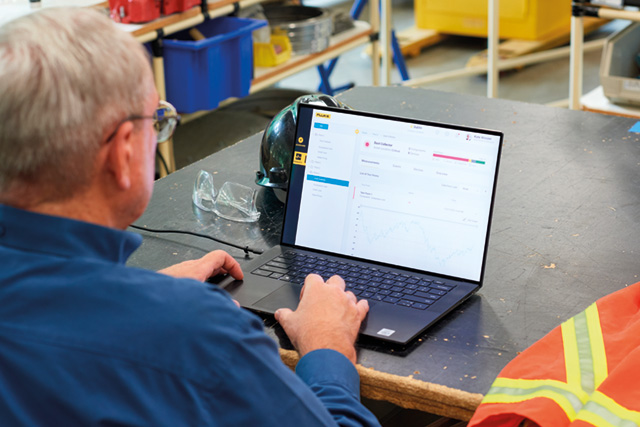
The wireless sensor revolution
Improvements in wireless sensors mean they are accurate and reliable, as well as being easy to set up and maintain. While technology limitations previously made wireless sensors expensive and inefficient, sensors today are more lightweight, have much longer battery life and do not require large amounts of communications bandwidth. Implementing wireless vibration sensors for a portion of plant assets is an effective, economical and low-risk way to jumpstart a CBM programme.
The benefits of wireless sensors mean their use is likely to grow much faster than wired systems. Technology research and advisory firm Mordor Intelligence projects a near quadrupling of the wireless condition monitoring market between 2021 to 2026.
Wireless sensors can be used to measure both the physical conditions of both an asset and its environment, such as power, temperature, oil condition and many other parameters. Monitoring vibrations – particularly in systems that include high speed or rotating machinery, such as pumps, fans and motors – is a particularly effective way to identify wear and other faults. Maintenance work is then triggered in order to prevent failure.
Vibration sensors and software for CBM
When considering the implementation of a CBM programme, there is no one-size-fits-all solution. Wireless vibration sensors, however, are a great place to start as they offer one of the strongest indicators of asset condition.
This is supported by recent research from Global Market Insights that shows widespread implementation of this technology in industries ranging from transportation and automotive to chemical, oil and gas.
An effective CBM programme requires software as well as sensors and other hardware. The best software can provide technicians with clear, actionable insights to determine the appropriate next steps to take in a maintenance operation. These tools also make machine health monitoring accessible to a range of skill levels within maintenance teams. In addition, reporting tools help the sharing of findings with other departments or the creation of work orders for third parties to fix machines.
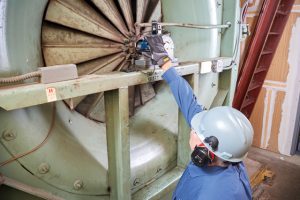
Benefits of wireless vibration monitoring
Vibration sensors are a proven technology, and have been available for several decades. The emergence of cost-effective, reliable wireless communications, however, is more recent. Using wireless vibration sensors can provide the following benefits:
1. Accurate indication of asset condition – All machinery vibrates, and excess vibration is a clear indication of issues. Today’s sensors track three axes of vibration, allowing monitoring in all directions, and many also offer other measurements such as temperature. Vibration data can be augmented by other data sets such as oil analysis, thermography, ultrasound or electric motor testing, providing a complete data set for evaluation that can be easily incorporated into your P-F curve.
2. Availability of the latest technology – It is easy to switch to the latest vibration sensing technology, and today sensors are built with piezoelectric technology, providing higher resolution and higher frequency vibration readings than the previous generation of devices that used microelectromechanical (MEMS) systems.
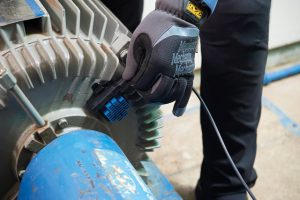
3. Powerful software support – modern software enables maintenance teams to constantly monitor and analyse data readings from critical assets. Features such as customisable frequency band alarms, pre-programmed thresholds, trend visualisation and notifications are also available, helping maintenance teams to determine critical next step actions. Today’s software extends the peak operating performance of assets while ensuring effective use of maintenance team resources.
4. Flexibility simplifies setup – Although many wireless sensors offer predefined data thresholds based on asset type, when required it is also possible to set custom thresholds. This enables the sensor to be configured precisely to the environment, application and asset being monitored.
5. Enabling large scale monitoring with high efficiency – Vibration sensors can monitor a broad array of assets. This enables maintenance technicians to focus their time and money on the machines needing attention. By ensuring highly skilled operatives are deployed efficiently to do the work they are trained to perform, large scale wireless monitoring systems can be built.
Jump start a CBM programme
The best way to begin is to experiment with a portion of assets and expand your programme over time. Starting with vibration sensors brings accurate indication of the condition of a wide variety of machines. To jump start your CBM programme, wireless sensors are the best choice because of their ease of implementation and quality.
As the programme grows, it is good to keep in mind that wired sensors can integrate successfully with wireless sensors. They fill an essential void in sections of the plant that lack Wi-Fi coverage, and wired sensors are especially well suited for production-critical, high end machines that mandate large volumes of high resolution monitoring data.
Vibration data can easily be augmented over time with electrical, thermography and other sensors. Using an array of data in this way to detect trends and analyse patterns allows operators to move from a CBM model to a predictive maintenance model and forecast when an asset will require attention. The change allows operators to reduce reliance on reactive maintenance, enabling better, more planned use of maintenance staff, minimal lost production and lower costs.
Help is at hand
Technology is accelerating the pace at which maintenance programmes are evolving. Outside training and guidance from an expert can help kickstart a condition-based monitoring and maintenance programme and ensure the latest technology and techniques are adopted, while allowing the maintenance team to focus their time and resources on the day-to-day demands of operations.
www.pruftechnik.com/en-GB | ptuk_sales@pruftechnik.com | t: 01543 417763