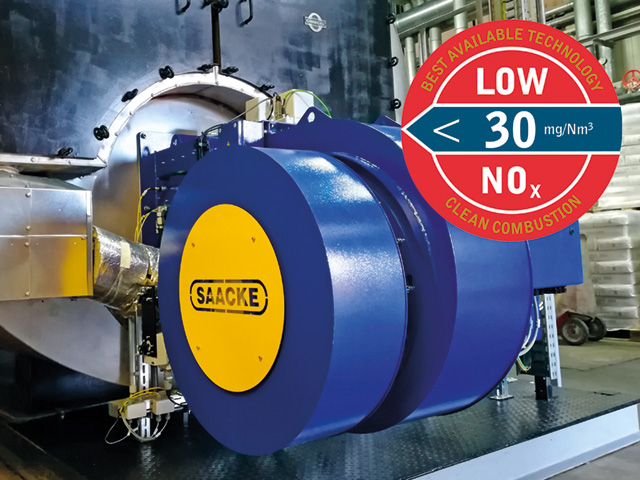
Costs associated with running firing systems could soon mount if care is not taken to ensure they are operated as efficiently as possible, says Phil Kemp, General Manager of SAACKE Combustion Services.
Anyone who operates firing systems in industrial plants, production facilities and in the central heating plants of large buildings needs an efficient and low-emission supply of heat or steam. High operational reliability and availability are crucial.
In the current climate we must all look at the efficiency of our plant to see where fuel savings can be made and where efficiency can be increased. If power, water levels, water quality or O2 (oxygen) are not working correctly, this wastes energy.
By monitoring the operation and needs of the plant, it can be possible to reduce the waste of valuable energy resources, ease strain on the environment and reduce operating costs. Small measures of change will improve the characteristics of the plant and increase its service life.
Major points to remember:
• For many companies, the cost of energy is surpassed only by their salary budget.
• Industrial and commercial plants consume 30-40% of the oil and gas supplied to the UK in the generation of steam and high pressure hot water processes. Are these processes being delivered in the most efficient way?
• Every drop of hot water down the drain is a drop too much and a waste of energy.
• To maintain a high level of safety and performance over the lifetime of products, customers must be made aware of the maintenance and replacement requirements of safety related components.
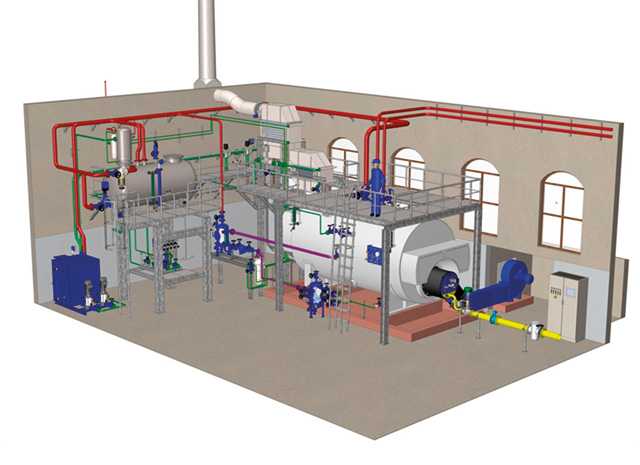
Remember the efficiencies:
Combustion
If you only measure flue gas losses when calculating the actual power output, you arrive at the combustion efficiency. This only tells you one thing: the amount of loss the burner or boiler system has at maximum power rating through the stack. Losses through radiation or blowdown are unfortunately omitted by this calculation. Boiler efficiency takes radiation losses as well as combustion efficiency into account and is therefore never quite as good. Boiler efficiency is also measured during a ‘static’ procedure – at a given power output. Losses at very low or zero loads are conveniently ignored.
Plant
In the case of plant efficiency (or total system efficiency), you have to look at all parts of the process from the fuel right up to your finished product. This can include water treatment, the condensate system and the deep fat fryer as well as bypass equipment, the condenser, the number of times the plant stops and starts and the accurate setting of the control limits.
Fuel
This efficiency ratio gives a useable basis not only to evaluate boilerhouse ‘hardware’ but also how this plant is controlled. Ultimately, there is a difference between a poorly optimised output control which constantly turns the burner on, modulates to full load and shuts off again. Compare this to a well adjusted control system which rarely restarts the burner and sensibly maintains it within an optimum load range. With the same hardware and producing identical amounts of steam, a plant with wildly fluctuating loads will use more fuel and be less efficient. This can only be measured properly by applying fuel efficiency, taking all operating parameters into account rather than just part of the system.
Remember the costs:
• Each percentage of oxygen above the optimum in the flue gases results in a 1 to 1.5% increase in energy consumption.
• With a 3 to 5% difference in O2 content and a 1 to 1.5% increase in energy consumption, it will mean a 3 to 8% variation in fuel used.
• A 2.5% variation in O2 will come as a combined result of a 10k change in temperature, a 20mbar pressure change and a 5% variation in fuel quality.
• A comprehensive tune-up with precision testing equipment to detect and correct excess air losses, smoking, unburned fuel losses, sooting and high stack temperatures can result in boiler fuel savings of 2 to 20%.
www. saacke.com | scsladmin@saacke.co.uk | t: 02392 333900