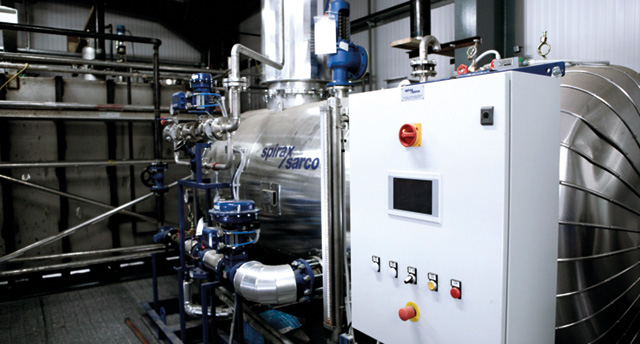
Michael Hyde, Business Development Manager at Spirax Sarco UK, explains key advantages of condensate recovery. and how this relatively simple concept can have huge benefits for organisations relying on steam for their processes.
After steam, condensate is arguably the next most valuable resource available to your plant; containing up to a quarter of the total energy of the steam from which it came, every. last drop should be recovered.
The ability to recover condensate to the boiler has the potential to provide exceptional return on investment. This energy saving process is easily achieved and can be done in more ways than one. Because of this, condensate recovery can sometimes feel like the unsung hero in the boiler house. Not only can it cut energy bills dramatically, but it can also see maintenance costs reduced.
Financial benefits
Utility bills and fuel costs can affect the profitability of the boiler house in a major way. Water and energy are the two key resources used to create steam, but the ever present pressure from fluctuating fuel prices can really impact overall running costs. It is for this reason that condensate recovery is one of the most effective resource-saving measures for most steam sites.
While a good system will recover 80% of its condensate and feed it back into the system, failure to recover condensate will cause the boiler house to suffer losses which can only be made up by a supply of fresh water. The energy then used to heat this water to the optimum temperature will directly impact operating costs.
When recycling condensate, users can therefore achieve valuable savings in both fuel and water-related expenses. Feeding the boiler with high temperature condensate provides steam users with the potential to maximise boiler output as less energy is required to convert ‘make-up’ water into steam.
Improvement of feed water quality
In a boiler, condensate recovery is also one of the best ways to reduce the level of oxygen in water, helping to minimise the risk of system corrosion. As condensate is formed from steam it has few impurities but in contrast to this, cold make-up water needs to be treated before entering the system.
Importantly, condensate – unlike make-up water – also contains energy from the steam it is derived from, so again, the more condensate that is brought back to the system, the better.
Environmental impact
What has to be remembered is that energy is lost during blowdown, so the ability to reduce this through recovering condensate will allow steam users to benefit from the associated energy savings.
By saving energy, operators of steam plants can experience significant financial gain as well as improved equipment life, all while reducing their impact on the environment. No matter how much condensate a site generates per day, it should never be put to waste.
How to recover condensate
Listed below are some useful tips to provide a starting point:
• Steam traps retain steam within the system for its heat, while releasing condensate and incondensable gases as needed.
• Condensate will always be pushed through the trap by motive steam force. If this is not possible, then it may be necessary to use pumps.
• Automatic pump traps act as conventional steam traps, but when ‘back pressure’ rises, pump traps automatically switch to pumping mode to remove condensate.
• A deaerator head is important to mix returned condensate, flash steam and cold make-up water as they are fed into the feed water tank.
• Flash steam is released from hot condensate when its pressure is lowered. Use it, don’t waste it. Collect in a flash vessel and use for heating, and recover any associated condensate.
• Closed-loop, pressurised flash steam recovery allows most of the energy from both the condensate and its flash steam to be used, reducing steam-raising costs and increasing boiler efficiency.
• Use the boiler water and flash steam from the boiler TDS (total dissolved solids) blowdown to heat the boiler feed tank.
There is no doubt that the payback period of an effective condensate recovery system has the potential to make this investment an attractive proposition. The ability to maximise boiler output and make the best possible use out of the energy found in condensate should be considered a huge advantage and never underestimated.
www.sxscom.uk/savingenergy | hello@uk.spiraxsarco.com | t: 01242 521361