ABSTRACT
Advances in the technology, and high energy demand, have resulted in requirements to extend the operating life of offshore installations well beyond their original design lives, maintaining production capability against changing demands, in a cost effective way, and developing an approach to asset management which requires that all aspects of operations essential to safety, integrity and environmental impact are properly dealt with (and which will also, where necessary, contribute to gaining regulatory consent). This paper describes, in detail, how a structured asset life review, covering all the relevant factors, is one means of developing such an approach – while additionally delivering significant potential financial benefits. Also presented is a short case study of asset life extension assessment for a North Sea installation.
INTRODUCTION
Improved extraction technology, combined with high energy demand, has resulted in requirements to extend the operating life of offshore installations well beyond the ‘retirement’ dates anticipated at the time of installation, when a typical design life would be 25 years. Many installations around the world are approaching, or have already exceeded, this figure but are now required to continue in productive operations for a further 20 or 25 years.
Operating the installations beyond their design life does not mean that they are no longer fit for service, but their owner operators face a common challenge, namely, ‘how to maintain production capability against changing operational demands, in a cost effective way whilst preserving integrity?’
A significant element of this challenge is the need to develop an effective approach to asset integrity management, an implementation which requires that all aspects of operations essential to safety and integrity are properly designed, constructed, tested, operated, inspected and maintained in a sustainable, holistic and systematic way, thus allowing continued beneficial operation. This approach will also help to meet the reliability and availability required by the business without compromising safety, integrity or environmental impact.
In certain regions, such as the North Sea, there is a requirement to gain consent from the regulator to continue to operate an asset beyond its original design life. A structured asset life review, as will be described in this paper, is one means of developing a case to support ongoing operation. It also delivers potential financial benefits through protecting or improving Overall Equipment Effectiveness as well as facilitating effective management of operating and capital expenditure.
The chosen approach must apply not just to the traditional interpretation of asset integrity management, focusing only on mechanical equipment, but also be extended to cover all factors with an impact on ongoing operation, including safety critical protective systems, electrical, instrumentation, control systems, maintenance practices, operations, engineering and human factors. This paper will highlight the key relevant issues, principally with regard to topside equipment, and provides a practical approach or insight into a suitable methodology to achieve this with optimal use of time and resources.
ISSUES FACED BY OFFSHORE OPERATORS
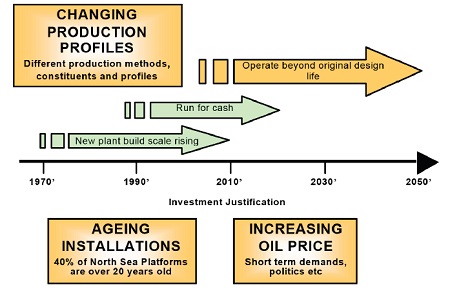
Industry, irrespective of the sector, faces challenging times. Increasing stakeholders’ expectations and relentless economic pressures are compounded by the difficulties of managing an aged asset base. Many offshore installations were built and commissioned during the 1970s and 1980s and are still operating today. Oil and gas price increases over the last few years have completely changed the dynamics of the industry, with marginal fields ceasing to be marginal and operating life requirements extending to the 2040s and beyond. (see Figure 1).
Availability of capital is not necessarily the main driver. Increasingly, operating companies are ‘sweating the assets’ i.e. operating existing assets beyond their original design life, rather than attempting to build new facilities against a backdrop of increasing competition for scarce EPC resource and long equipment delivery.
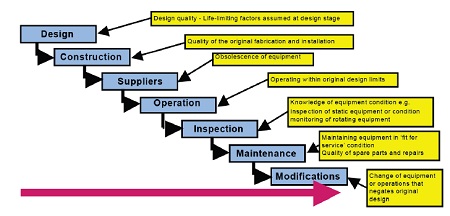
To fully understand the issues affecting asset life extension, it is necessary to understand the factors which will have already had an impact and need to be managed in the future. Figure 2 provides a typical view across the whole asset life cycle.
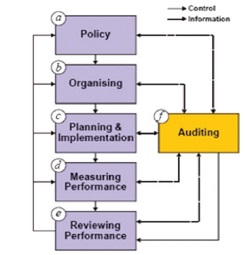
Figure 3 shows a typical process for managing asset life, in this case that given in the UK Health and Safety Executive’s guidance HSG65 (1997).
The wide ranging nature of these factors dictates the need for an integrity management framework that includes:
- Clear policies and objectives
- Appropriate organisational structure and clear responsibilities
- Effective planning, procedures and implementation
- Measurement (KPIs)
- Review and audit
The management framework is essentially a structure for managing risk and should address the key areas of Competent People, Reliable or Predicable Assets and Effective Systems.
Managing risk is not only about equipment condition. Equipment could have been originally specified, designed and constructed to the best possible standards, but if it has not been maintained, inspected, modified and operated in an appropriate manner in line with standards and best practice, its effective operating life will have been reduced. Further, if in the future, an appropriate asset management strategy is not followed, the future operating life and budgetary requirements are almost impossible to predict.
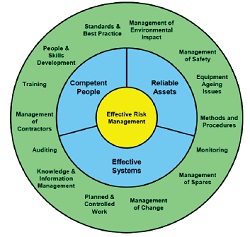
Effective risk management is a wide ranging and holistic activity, as can be seen from Figure 4, which shows only a typical list of the activities and processes required to support Competent People, Reliable Assets and Effective Systems. Hence, any study or review to look at asset life extension must be comprehensive or not simply equipment focussed.
The long term viability of the field, whether for oil or gas or both, is the key life extension consideration. Once this viability is established, then the capability of the installation, in terms of fabric and equipment, to continue to operate for the remaining period of viability for the field is an obvious next step. This is usually covered by detailed review of the sub-sea elements, such as the well heads, jackets, main platform structures and sub-sea piping. Failure or significant degradation of the structures or the sub-sea elements renders the installation unusable and inoperable. Once these have been addressed, the top-sides equipment must also be able to deliver expectations in terms of asset life, often against changing future demands and operating regimes.
In this area, asset life is not simply the integrity of the top-side equipment items; degradation of pipe work or vessels, obsolete equipment or unreliable machines, but also needs to include the capability and competencies of the operations, maintenance and engineering organisations to allow the life to be extended and cope with changing circumstances. In addition, equipment must also be capable of dealing with changing production demands such as changes in well pressure as well as new deterioration mechanisms or potential failure modes that arise from these changes, such as running compressors at low rates or the impact of new corrosion mechanisms driven by new or increasing levels of contaminants such as carbon dioxide or mercury.
To illustrate this, the following list is a compilation of the typical issues relating to the top-sides identified during recently undertaken asset life extension studies for offshore installations.
- Removal of redundant equipment to simplify the systems and reduce structural loadings or create space for new equipment
- Replacement of obsolete equipment, often a number of times during the life cycle
- Reducing equipment reliability, particularly machines and rotating equipment
- Need to replace people skills with automation, as skilled people become harder to recruit and retain
- Management of newly emerging corrosion/deterioration mechanisms (not always considered at the design stage) that relate to new production regimes, increased understanding of deterioration, such as corrosion under insulation or long cycle time based, such as creep.
- Lack of defined operating envelope for some equipment, giving the risk of operations outside the original specifications
- Turn down capacity of key equipment as process requirements change
- Integrity of minor structures (handrails, walkways, ladders)
- Maintenance of competencies against ageing workforce and retention of corporate knowledge
- Electrical power limitations, often as a result of increased demand or equipment reliability/availability.
- Compliance with current and future environmental legislation
- Fire Protection due to ageing or as an opportunity to adopt best practice
- Safety and Escape equipment as standards improve
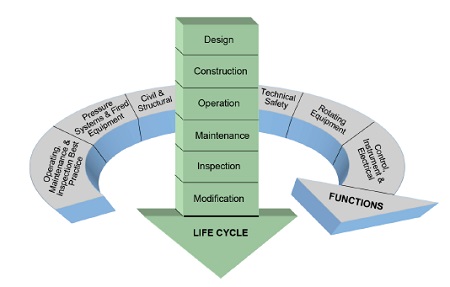
Topsides asset life extension studies therefore require a holistic approach covering a wide range of topics and expertise, as illustrated in Figure 5. The key, as will be described later, is to apply the expertise in the most efficient manner, delivering results in an acceptable time to a level of accuracy compatible with the capability of the operator to predict the future.
Overall, asset life extension is concerned with the effective development of a strategy to manage future risk – of which the risk to equipment integrity is only one factor. Figure 6 shows the wide range of potential topics involved in a truly holistic approach.
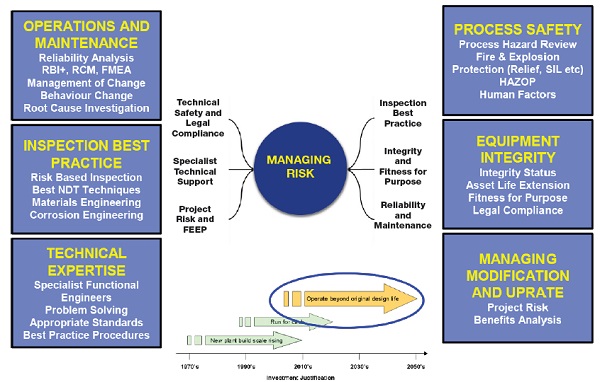
Many operators of ageing assets are also facing the challenge of maintaining production efficiency, where one of the problems is the deterioration in equipment reliability. Managing reliability in ageing assets is fundamentally an exercise in risk management. Much can be done to improve equipment reliability through investment and replacement policies, but experience shows that failures will still occur. Accepting this as a possibility and managing the impact of these failures on availability can be significantly beneficial.
Understanding equipment criticality is essential, but equally important is understanding vulnerability, or how well the risks generating the criticality are being managed. It may be necessary to become good at breakdown maintenance again, by ensuring that the necessary people competencies, tools, equipment and spares are available for key areas of vulnerability.
Operating equipment comfortably within its design envelope generally results in high levels of reliability.
Such an approach could, for example, result in upgrading the protection system on a key compressor to include not just vibration alarms set early enough to give reasonable response time, but also trips that shut the machine down before too much damage takes place. The net impact on availability by reducing the machine repair time generally outweighs any short term production loss. A pragmatic review of vulnerability will reveal many more examples across the full equipment range.
Probably the biggest impact on availability is achieved by reducing the duration of planned shutdowns or turnarounds (TARs). There are many proven methodologies for ensuring effective, minimum duration TARs, but how many TARs over-run the planned duration? The capability to effectively manage TARs to meet the planned outage periods should be considered a key competence for an operator as plant continues to age.
BASICS OF AN ASSET LIFE EXTENSION ASSESSMENT METHODOLOGY
An asset life extension methodology needs to address two areas:
- The effectiveness of risk management (as shown in Figure 4).
- The integrity of the equipment
There are many options for assessing risk management capability in terms of the people, practices, procedures and systems aspects of the regime concerned. Methodologies, often called ‘Health Checks’, in this area are usually in the form of a gap analysis, using a combination of quantified measures, such as benchmarking or best practice KPIs in combination with the semi-quantification of qualified assessments, using word models to assess areas such as the quality of the inspection process, availability of expert technical support or the levels of people competency. A typical gap analysis could look something like that shown in Figure 7.
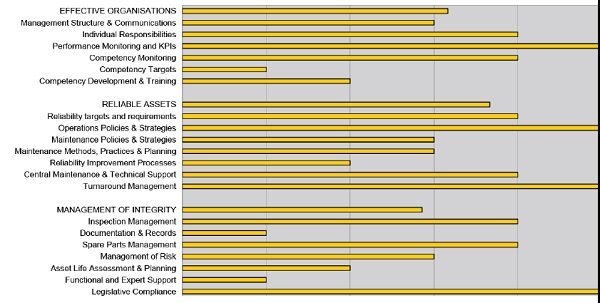
Studying the asset life limitations for equipment requires an understanding of the likely deterioration modes, and assessment of the capabilities of the equipment to resist the deterioration, largely based on the Life Cycle factors shown in Figure 1 and the capability of the organisation to manage the risk. The following is a typical list of the deterioration modes relevant to offshore installations:
- Corrosion, particularly arising from changing operations and production profile.
- * Fatigue, particularly where corrosion and material loss results in stress increases.
- Creep.
- Structural and fabric integrity.
- Wear-out.
- Obsolescence
- Thermally induced deterioration.
- Overstress as loadings change over time.
- Blockage and choking resulting in dead legs for corrosion and overstress.
- Explosion, which is an extreme view but often relates to inadequate management of risk from equipment in potentially explosive atmospheres .
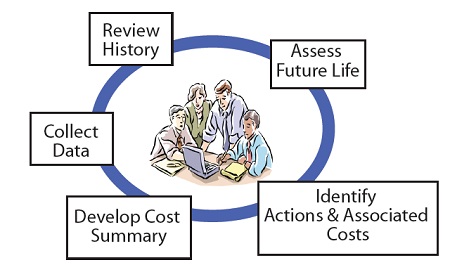
The basic process for assessing the equipment integrity is shown in Figure 8.
Figure 9 illustrates an assessment of asset life of an item of equipment, in this case a de-aerator vessel.
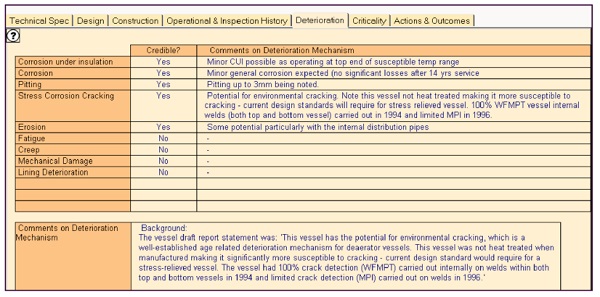
The process of establishing the technical specification for the vessel, the original design criteria, construction materials and operational/inspection history is not as time consuming as it might appear and can often be achieved electronically or worst case as a clerical exercise. The deterioration stage is similar to that used for an RBI (Risk Based Inspection) study and is a top-down approach rather than a remnant life assessment (The difference between these will be explained later.).
The deterioration review leads to the identification of actions either to manage the risk in terms of best practice actions from the gap analysis, further activities to clarify the risk, such as further inspections, or repair/replacement activities. Each action is allocated a cost and an implementation date to allow the production of a budget programme histogram, such as that shown in Figures 10 and 11.
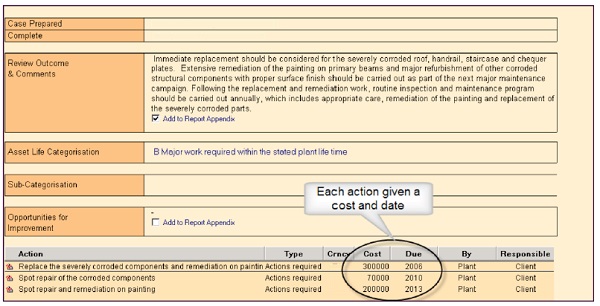
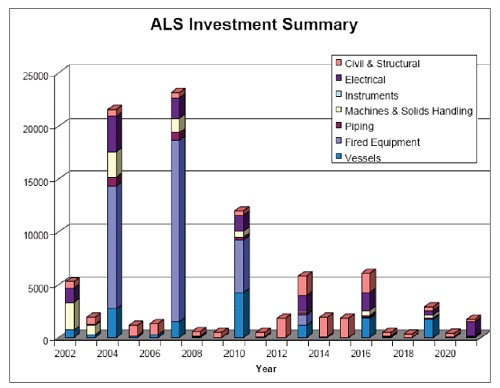
ASSET LIFE, REMNANT LIFE AND TOP-DOWN ASSESSMENTS
The methodology and approach to asset life extension described in this paper is often confused with, and not the same as, a remnant life assessment.
Effectively a remnant life assessment is an estimate of the remaining life by calculation or quantification of the effect of the deterioration mechanisms in comparison with the original design. It is governed by specific guidelines and standards, such as API RP 579, for each type of equipment and can be extremely time consuming.
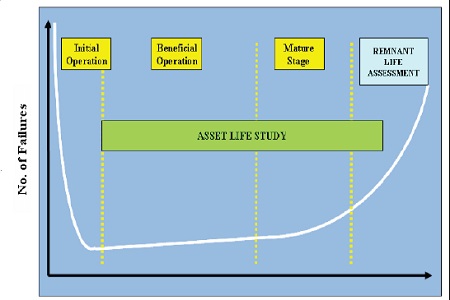
The principal difficulties with remnant life assessments can be summarised as below:
- Remnant life assessments depend on predictable (usually linear) deterioration and consistent operations.
- Hence they are only sensibly accurate over short time periods and usually only add value towards the end of the Asset Life Cycle, as shown in Figure 12.
- The accuracy needs to be greater than the shutdown interval.
- They need a lot of fundamental design information to do the calculations for each deterioration mechanism.
- Our experience suggests that it is best to only use them when you have to!
An alternative to the conventional remnant life assessment is the Top-Down approach. Here, starting from the normal design life, taken from design standards or best practice, the impact of deterioration mechanisms is estimated and an assessed life estimated. This can appear to be a rather crude estimate, but when the limitations and accuracies of conventional remnant life calculations are taken into account, it is certainly comparable and has the considerable advantages of speed and much lower resource usage.
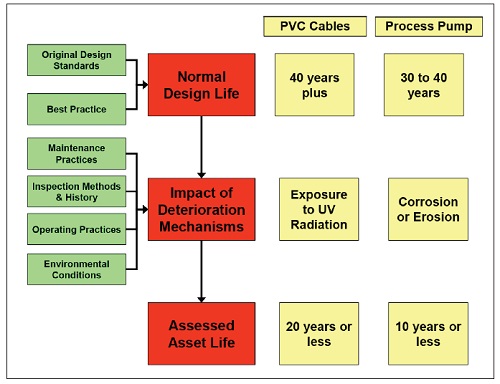
An obvious question relates to what standards to apply when considering the asset life. Over the life of an installation, standards will change. Retrospective application of new standards can result in complex and expensive actions to maintain asset life. A better approach is to understand why the new standards were introduced and review the deterioration or future asset extension requirements in that context.
CASE STUDY – ASSET LIFE EXTENSION FOR A NORTH SEA INSTALLATION
An operator in the northern sector of the North Sea required an external risk based assessment of the expenditure required to provide continued operation of the installation until the end of the licence. At the time of the study the platform and field had been in operation for about 25 years and a further 30 years of life was being considered. The main decision faced by the operator was to refurbish or replace, and the primary objective of the study was to provide the essential inputs into their OPEX and CAPEX budgets to support the decision making process. A secondary objective was to assess the current vulnerability to identify any major issues not currently understood and covered by the budgets. Here vulnerability is defined as a measure of how well risk is being managed.
The scope of the study covered the topside equipment, including:
- Vessels, storage tanks, sea sumps
- Piping, including risers from splash zone
- Valves, include wellhead valves/Christmas trees
- Machines and rotating equipment
- Structure including cranes, well supports and life boat davits/supports
- Control/instrumentation
- Electrical and power distribution
- HVAC
The scope excluded subsea assets such as pipelines and jackets, well and well operations, the drilling rig and helicopter/marine support. These areas had been covered previously by the operator. The study revealed no significant obstacles to the required life extension and showed many areas of good practice, viz.
- Knowledgeable and committed workforce, on-shore and off-shore
- Key asset integrity issues largely covered by existing plans
- Standards of asset care generally good
- Management systems in place for effective asset care
- Evidence of high standards, e.g. regarding electrical cabling and cable racks, pressure vessel inspection and housekeeping
Some of the issues that required specific action are summarised as follows:
Corrosion protection
Assets showed evidence of a historically reactive approach to ‘Fabric Maintenance’
Observed levels of corrosion should not prevent life extension
Without a proactive and planned programme of fabric maintenance, it was unlikely that the asset life targets would be met
Piping
Only 20-50% of piping systems were inspected using a thorough scheme of examination and concerns arose relative to inspection of small bore systems and branches. Remediation or replacement was assessed as high cost.
Registration required of all systems required to support risk based asset strategy
Utility piping CS corrosion allowance consumed, e.g. in fire water piping system
Some areas of hydrocarbon piping subject to micro-biological induced corrosion (MIC) and will require replacement in Super Duplex
Electrical
The original low voltage switchgear was obsolete and spare parts were difficult to obtain, requiring an action to replace original equipment with new switchboards
Most cables and cable support systems were in very good order but attention required to steelwork attachments
Power limitations and supply reliability related to generation equipment unreliability rather than capacity limitations
Rotating equipment
Structural vibrations associated with replacement diesel generators was a major contributor to unreliability
HVAC refrigeration – R22 conversion was required
Fire water pump long term unreliability is a significant threat and requires an investigation followed by equipment replacement
Export compressor turn-down and low suction capability was inadequate against the predicted production profile
Gas turbine CO and NOX emissions were likely to be beyond future consent levels
The above issues were translated into a range of actions and recommendations, which were in turn allocated costs and timings. Timings were related not only to priorities but also to opportunities to perform the work, such as shutdowns or resource availabilities. The resulting cost histogram is shown in Figure 14.
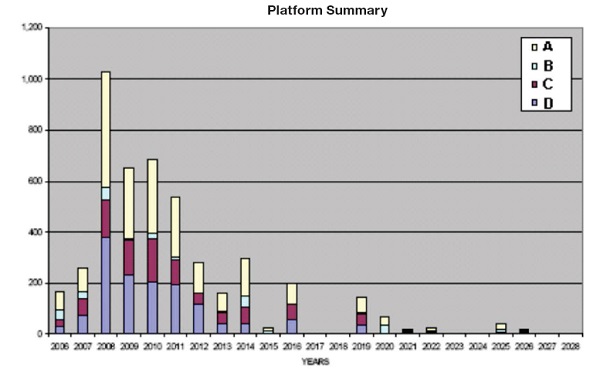
The profile showed a number of points worthy of note:
* A large peak of expenditure was required in the first 5 years or so to replace certain piping systems and control or instrumentation items, but once replaced, these should provide for continued operation with minimal on-going costs.
* The profile includes maintenance costs, based on a strategy to ensure that minor issues do not accumulate to create major expenditure but accepting that maintaining old assets, even after major refurbishment, requires a different philosophy to maintaining new assets!
SUMMARY OF BENEFITS AND CONCLUSIONS
Asset life planning allows informed planning of expenditure, based on a cohesive view of what the future holds – bringing forward expenditure when times are good, deferring the right things when times are bad! .
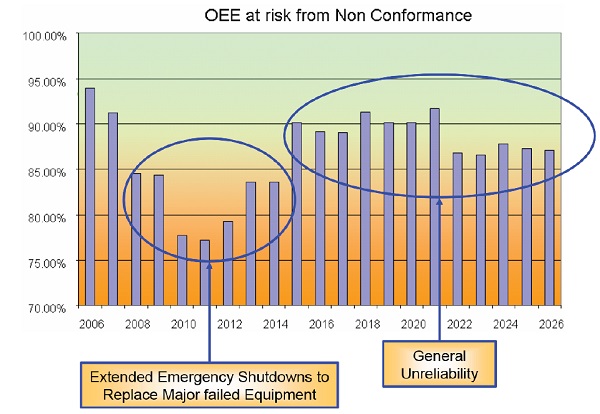
Figure 15 shows the impact of poor asset life management on the Overall Equipment Effectiveness of an asset. Failure to plan for major equipment replacement can easily result in extended shutdowns as inspections reveal unforeseen problems or general reduction in equipment reliability. A properly specified and conducted Asset Life Extension Study will identify:
- Where and why deterioration is taking place
- What is needed to maintain equipment integrity
It will provide life cycle actions and budgetary plans with investment to prevent failure rather than as a reaction to it. As additional benefits, it will provide:
- Improvement of operating and maintenance practices
- Demonstration of pro-active management of assets
- Education of plant personnel through exposure to the study
- Reduced risk of HSE incidents.
It allows the development of a strategy to control and manage the risk associated with extending the life of offshore installations – a strategy based on a systematic process to support the case for life extension that will satisfy stakeholders, shareholders, legislators and employees.
REFERENCE
1. Health and Safety Executive (United Kingdom), Successful Health and Safety Management, HSG65, ISBN0717612767, published in 1997