ABSTRACT
The development and implementation, within Nuon Productie (part of Vattenfall), of the Maintenance Criticality Reassessment (MCR) method – based on the FMECA concept – is described. With this new method it is possible to improve and consolidate the effectiveness and cost efficiency of preventive maintenance, in particular when applied to low risk classified systems. Such systems possess a low criticality in terms of process and HSE safety risks and therefore applied maintenance should be focused on achieving and securing the lowest Total Cost of Ownership (TCO).
For each maintenance activity the risks of failure that are to be managed are determined, the presence of improvement potential, the necessary modifications in order to achieve this, and the optimised maintenance activity to be performed. All these elements have to be in line with the business strategy. Also, relevant policy documents are actively used, whereby the quality of the results obtained and the time required is secured since aspects such as process automation, information productivity and stakeholder motivation are an integral part of the MCR concept.
By verifying the MCR concept during a series of case studies and workshops, it has been proved that the functionality and results obtained were in compliance with stakeholder expectations: An annual Total Cost of Maintenance (TCM, which includes both corrective and preventive maintenance costs) reduction of approximately 30% of a considerable original maintenance budget was realised. This was the result of discontinuing, on average, 43% of activities (due to the absence of legitimacy for them) and the optimisation of the remaining activities (i.e. those for which legitimacy could be proved). This was achieved without introducing unacceptable risks and was obtained by highly motivated participants, in an average of 90% less time than required if earlier available methods had been used.
INTRODUCTION
An important contribution in this comes from maintenance, its purpose described by Moubray as ‘ensuring that physical assets continue to do what their users want them to do.’ [2], which in this case means generating energy at minimal operational costs, i.e. at the lowest TCM of the asset portfolio that can be pursued, without incurring unacceptable risks in the process of doing so. Also, Zaal [3] has stated that ‘maintenance should be treated and organised as a business process to fulfil the company’s main goals in a profitable way’. Within Nuon this strategy is currently incorporated to a limited extent in preventive maintenance which manages low risks of failure. Although risk levels are low, a significant budget is allocated for the preventive maintenance of these systems. It is anticipated that this expenditure arises from preventive work which is performed too often, or includes unsuitable activities, or which is substantiated by irrelevant arguments and is therefore not necessary at all.
This situation is allowed to develop over time, presumably because systems classified low risk, due to their low criticality regarding process and HSE risk, have historically had little attention in terms of sound asset management, since assessment of their maintenance performance did not come naturally. This behaviour went even further because available assessment methods were found to be too labour intensive and produced results that were unpredictable as regards their effects on maintenance cost.
This specific context gives rise to the desire to develop a new method, requiring low human resource, for optimising the TCM of systems classified as of low risk. This method should comprise a structural approach, like RCM and FMECA, where relevant corporate policies are used as a reference framework and that produces verifiable results.. The method and forthcoming results should furthermore be accepted by its stakeholders.
PROBLEM STATEMENT
By which (human) resource-efficient method can the cost-efficiency and risk management effectiveness, of existing preventive maintenance applied to low risk systems, be systematically assessed and improved, and where results in terms of asset management risk analyses are secured in the ERP system of Nuon (SAP PM with the RCMO application)?
RESEARCH METHODOLOGY
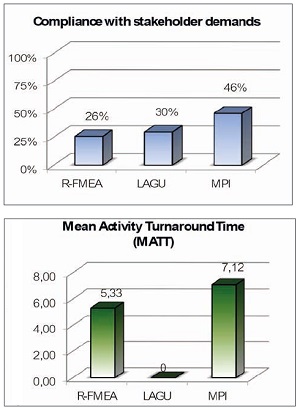
During stakeholder interviews and workshops three methods – namely R-FMEA, LAGU (Designation used at the Local Asset Group Utrecht of the best practice for maintenance optimisation) and MPI (Maintenance Performance Initiative, another method for maintenance optimisation, previously used within Vattenfall) – that are currently used for managing the maintenance of low risk assets, were identified and their performances assessed (see Figure 2). This showed that none of these methods functioned as required: for being, among other things, too demanding on human resource and using decision-making for risk assessment which was not in accordance with the risk policy of the company.
This experience, and the knowledge thus gained, has led to the evolution of the concept of Maintenance Criticality Reassessment (MCR), and its subsequent development into a tool which can be used in daily practice. After receiving approval of all the involved stakeholders to incorporate it into Nuon’s Asset Management Process it was piloted during three case studies which have demonstrated that it performs as intended.
RESULTS
Availability of the MCR concept
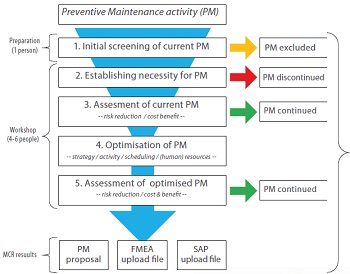
As a result of this project, the concept of MCR is now available to reduce, by residual risk optimisation, the TCM of low risk systems,. It is based on the well-known FMECA concept, in which aspects such as stakeholder motivation, information productivity and process automation are integrated throughout. It is conducted during a workshop, with participating stakeholders, in which a series of consecutive steps is elaborated (see Figure 3):
1) Prior to the workshop each activity is screened by the workshop facilitator as to whether it is fit for being assessed or not, and in doing so it is ensured that only relevant maintenance activities are included in the scope of work. If an activity fails to meet a set of criteria it is excluded from further analysis.
2) The first step during the workshop is to establish for each activity whether there is a necessity for preventive maintenance. This is done by assessing the risk of failure to be managed and then by plotting this information on the company’s risk matrix. If the risk levels are acceptable this means there is no need for preventive maintenance and the activity concerned is marked to be discontinued and excluded from further analysis.
3) Each activity that incurs levels of unacceptable risk is assessed next, on its risk managing effectiveness and cost efficiency, by comparing its performances with predetermined standards. If performances are up to, or above, standards the activity in its present form is deemed both effective and efficient and can be continued in its present form and is therefore excluded from further analysis.
4) If performances of an activity are sub-standard its characteristics (e.g. maintenance strategy, performance based interval rather than time based, responsible department, etc.) must be re-considered in order to improve its effectiveness and/or cost efficiency.
5) Each optimised activity is assessed once more, as previously. If performances are up to, or above, standards the activity in its optimised form is both effective and efficient and can be continued in its reconsidered form and is therefore excluded from further analysis. The activity reconsidered must be assessed again if performances are still sub-standard.
The MCR work file
The elaboration of the above steps is facilitated by an MCR work file, which also contains previously entered data dumps from the Enterprise Resource Planning (ERP) system, such as maintenance activity details and budget. Gathered information is included in this work file from which the MCR end results, among other things, are automatically derived:
1) A preventive maintenance proposal, which summarises the accomplished cost saving potential for the asset´s TCM. Furthermore, the residual risk levels resulting from the optimised activities are displayed, by which it is demonstrated that the optimisations do not introduce unacceptable risks.This document is used, by the person responsible for managing the particular asset, whenr deciding if the workshop results are going to be implemented in the operational maintenance activities. After approval has been received, the next two documents are available, via which the workshop results can be uploaded directly into the relevant applications.
2) A file containing maintenance concept revisions, in which the results from the workshop are converted into a FMECA analysis, its layout compatible with the application it is uploaded to.
3) A file containing maintenance plan revisions, in which the results from the workshop are converted into maintenance activity modifications, its layout again compatible with the application it is uploaded to.
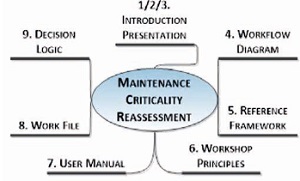
In addition to the work file used, the carrying out of MCR as a whole is supported by a set of provisions which serves the purpose of improving and consolidating the quality of the results and the time required to obtain them (see Figure 4).
MCR’S FIRST USE
To demonstrate the actual capabilities of the MCR concept it has been piloted through three case studies in which a total of 192 maintenance activities were included.
An annual TCM reduction of approximately 30% of a considerable original maintenance budget was realised. This resulted from discontinuing an average of 43% of activities due to their lack of legitimacy and also the optimisation of the remaining activities (i.e. those for which legitimacy could be proved). This result was achieved without introducing unacceptable risks and was obtained by highly motivated participants in 90% less time, on average, than would have been required if earlier available methods had been used.
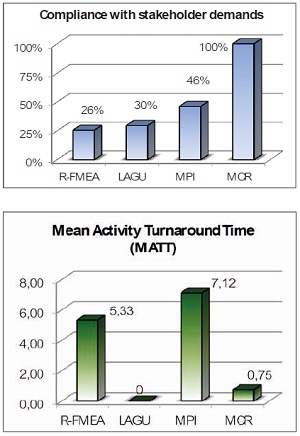
Based on stakeholder feedback concerning the specifications of the results produced, and on the time required to obtain them, it can be stated that, with MCR, results can be produced which are in full compliance with stakeholder demands. This result has been acquired using a method with an 88% improved time efficiency (as a result of the reduction in the human resources required) and a 54% improved effectiveness (as a result of improved conformity with quality expectations) (see Figure 5).
Conclusions
Derived from these combined results it can be concluded that, validated through a series of case studies, our operations are now able to produce results, using MCR, which are in full compliance with stakeholder demands in terms of the method’s effectiveness and efficiency. This enables us to reduce the TCM of the asset portfolio in accordance with corporate policies, in order to improve and consolidate advantage, in cost leadership, over competition.
Discussion
The field of application of MCR is not limited to low risk systems; it has already been successfully applied in managing the maintenance of moderate and high risk systems. It is therefore strongly believed that MCR can be used to reduce the TCM of all systems in an asset when cost leadership is a prerequisite.
Furthermore, MCR can be regarded as an evolution of the well-established FMECA concept; it uses a re-arranged sequence of FMECA aspects in order to focus on a maintenance activity instead of on the technical system or object itself. Furthermore, process control, stakeholder motivation, re-use of readily available information and process automation are integrally incorporated within MCR.
MCR is now incorporated in the asset management methodology of Nuon. Its application on a major asset has resulted, in that case, in an annual TCM reduction of approximately 45%. More MCR sessions are scheduled for several power plants in the asset portfolio. Recommendations
Continuous developing insights should be obtained concerning the standards which are used for assessing the performance of maintenance activities. Further cost savings can be achieved by using stricter threshold values. Additional research should therefore be conducted in order to achieve progressive insights concerning such values.
Interval optimisation algorithms from reliability theory should be added to the concept of MCR, replacing the arbitrary estimation currently used. In this way further optimisation of maintenance activities can be achieved.
REFERENCES
1. Porter M, Competitive Strategy (59th ed.), :Simon and Schuster Ltd (1998)
2. Moubray J, Reliability Centred Maintenance (2nd ed.), Butterworth-Heinemann, Oxford:(1997)
3. Zaal T, Profit-Driven Maintenance (2nd ed.), Maj Engineering Publishing (2013)
Authors may be contacted via –
sander.hendriks1@nuon.com
tim.zaal@hu.nl