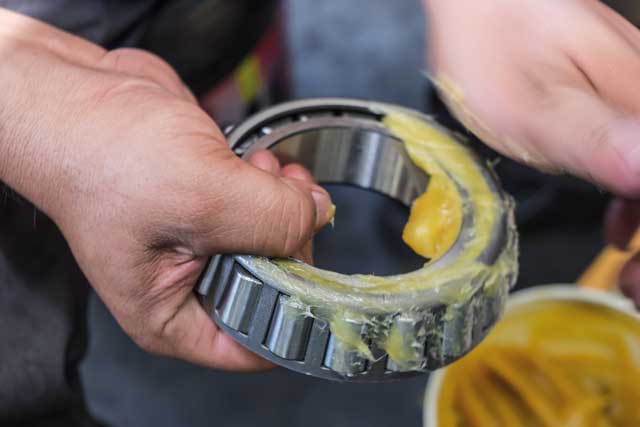
The word “grease” comes from the Latin word “crassus” meaning “fat”, which effectively describes its consistency.
It is believed that around 500BC the ancient Egyptians were among the first to develop a real grease by combining olive oil with lime (calcium), which acted as a thickening agent.
The purpose of grease lubrication
A lubricating grease is a semi-fluid to solid lubricant containing a thickening agent and additives.
There are three core principles of grease lubrication: the grease works its way into the cavities around a bearing; the thickener holds the oil in the lubricating zone; and the grease shears, delivering a slow release of oil into the path of the rolling elements.
The purpose of grease in industrial applications is to lubricate moving parts while retaining its performance properties under extreme temperatures and pressures.
Industrial applications where grease may be used include roller bearings, open gears, enclosed gears, centralised systems, wire ropes, slides and seals.
In most applications, the original manufacturer will recommend a grease or an oil for its machinery. If a bearing needs both cooling and cleaning, an oil may be recommended. However, if the location is difficult to access and cooling is not needed, a grease can be used.
Grease constituents
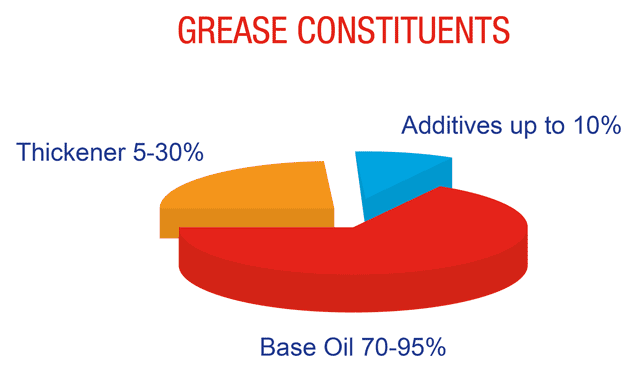
There are three constituents of a lubricating grease: a base oil, thickener and additives.
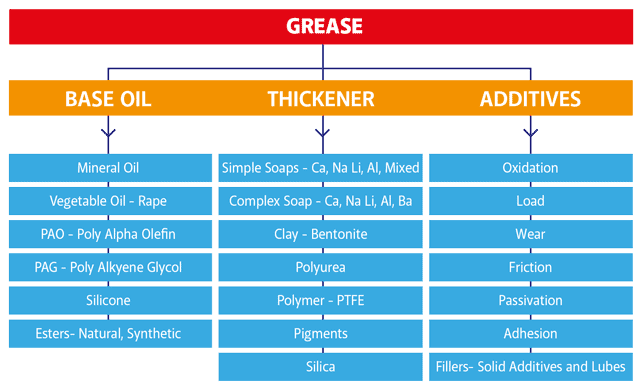
Grease is typically made of 70-95% base oil. The base oil used in most greases produced today is mineral oil, because it is cost-effective and performs well in industrial applications. Synthetic oils are used as the base oil in some lubricating greases where high temperatures are experienced, as well as in biodegradable greases.
A thickener is added to the base oil and this gives the grease its consistency. Whereas oils are classified according to their viscosity at different temperatures, greases are graded according to their consistency, measured by NLGI number, at 25°C.
The thickening agent can be soap-like and is often referred to as a sponge that holds the lubricant, which, on squeezing, releases the oil.
Thickeners include metal soaps (calcium, sodium, lithium or aluminium), complex metal soaps (calcium complex, sodium complex, lithium complex, barium complex or calcium sulphonate complex). Thickeners that may be more suited to very high temperature operations include bentonite clay, silica and polyurea.
The type of thickener that is added to the oil affects the properties of the grease – see table below.
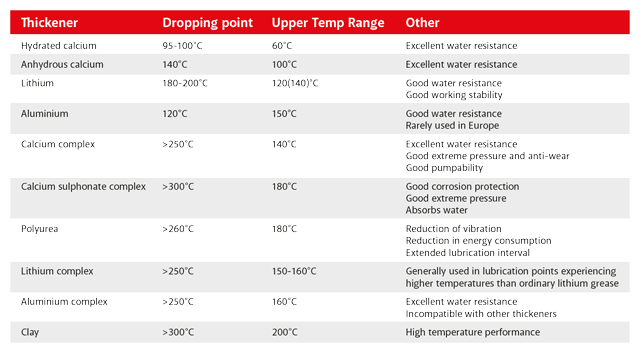
Typical thickener properties
Finally, additives are used to improve specific performance properties. For example, antioxidants may be added to reduce oxidation, thereby extending the life of the grease. Extreme pressure (EP) additives may be added to increase load-carrying capacity.
Advantages and disadvantages
Grease has both advantages and disadvantages compared with oil. Advantages include: grease stays in place because of its consistency; it seals out dirt, functioning as a sealant to prevent leakage and keep airborne contaminants out. It offers a high temperature range; lower coefficients of friction; water resistance; and noise and vibration damping. It is resilient – it copes well with neglect.
Some semi-fluid greases can be used in some oil systems to avoid leakage that may happen with an oil.
Disadvantages compared with oil are that grease does not remove heat; it does not clean; it cannot be filtered; and it needs replenishing frequently
Grease performance testing
Various laboratory tests are conducted to measure the performance of grease.
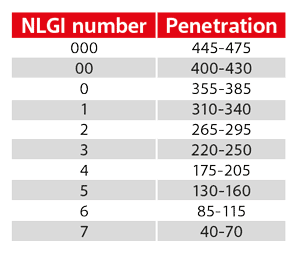
Consistency is rated by the cone penetration test, in which a cone of standard weight is placed on the surface of a level cup of worked grease at 25°C. The cone is allowed to sink into the grease under its own weight for five seconds and the depth to which it sinks is measured in tenths of a millimetre. The penetration measured is rated according to the National Lubricating Grease Institute classification scale, where 000 is very fluid at room temperature and 7 is much more solid.
Another important measure is “dropping point”: this is the temperature at which the oil separates out of the soap to flow through the orifice in a small metal test cup. However, it should be noted that the dropping point is only an indication of the upper temperature limit at which the grease retains its consistency, not the maximum temperature at which the grease may be used.
The performance properties of the grease, including extreme pressure resistance, can be measured using the four-ball scar and weld load tests, as well as the Timken OK Load test, which can give an indication of how the grease will perform under heavy loads. The SKF EMCOR bearing test gives a good indication of how the grease will perform in a bearing contaminated with water and sea water.
Specifying grease
It is important to select the right type of grease for a particular application, which can be done by checking the indications from the properties on the grease’s data sheet.
In theory, most greases will lubricate a bearing, but the difficulty arises when the bearing is subject to harsh environmental conditions such as heavy or shock loading, slow or very high speeds, dirt, water, cold or heat. It is therefore essential to use a grease that will be able to withstand such severe conditions.
Technical guidance should be sought from a grease manufacturer or a bearing manufacturer if there is any uncertainty.
To give some examples:
For high speed bearings, particularly in fans and blowers, it would be good to use a polyurea NLGI 2 grease with a thin base oil, because this provides good lubrication but also damps vibration and reduces noise.
For general purpose lubrication, in wheel bearings for example, a lithium NLGI 2 EP grease could be used.
For high temperatures, for example in heavily-loaded bearings, a bentone molybdenum disulphide grease could be used.
Calcium sulphonate complexes are very useful where EP, anticorrosion and water washout is needed, particularly in the steel industry, for example.
Method of application
How the grease is dispensed depends on the application. A handheld grease gun may be used, where a greaser puts the correct shot of grease into a moving bearing at regular intervals.
To get to hard-to-reach areas, small grease dispensers may be used. These may be powered by battery or gas and dispense the required amount of grease at scheduled times.
Electrical grease dispensers that pulse a specific amount of grease into the bearing at a certain time are widely used in factories instead of manual greasing. Large systems can use grease tote bins that supply factories through grease dispensing units.
If a grease gun is being used, a NLGI 2 or 3 grease would be suitable, whereas a NLGI 0, 00 or 000 would be the recommendation for a centralised lubrication system.
General considerations
The amount of grease required, for example in bearings, depends on the rotational speed. In a typical medium-to-high speed bearing the grease should fill about a third of the free space. In slow-moving, heavily loaded applications, more grease will be needed.
If the bearing is overpacked, when it rotates it will centrifugally throw out the grease into the housing. If it is too full, it will generate heat which will oxidise the grease, harden it, and allow the oil to leak out.
It is more efficient to lubricate little and often, so it may prove cost-effective in the long run to invest in a higher quality grease, as this will help to extend the intervals between re-lubrication.
Maintenance staff should also seek to rationalise the number of different grades they require and keep these to a minimum. A streamlined grease inventory will create less confusion.
The NLGI grade is just the starting point in understanding a grease’s consistency and this, together with other information about the grease’s properties and performance, are normally found on the product’s technical data sheet.
Compatibility
Care needs to be taken when mixing different types of grease. If they are incompatible, the soaps could react with each other and release the oil. If a new grease is introduced, it is essential to make sure it is compatible with the one already being used.
Finally, with the number of grease compositions available, it is important to select the right type for a specific application. The cost of grease itself is negligible compared with the cost of repairs and lost productivity if it is not suitable for the application or if it is not replenished adequately.
Total greases
General purpose
MULTIS EP range – multipurpose extreme pressure greases, will cover most applications
MULTIS Complex EP range – for higher temperature operating systems
Speciality
Anti-seize (SPECIS CU) – an anti-seizing copper grease for threaded assembly under severe corrosion conditions and high operating temperatures
Track roller – lithium semi-fluid
Constant Velocity (CV) joint grease – lithium EP plus solid lubricant
CERAN – based on calcium sulphonate complex thickener; providing outstanding resistance to water, wear, and load and mechanical stability
www.total.co.uk/businessproducts/industrial-lubricants
01977 636303 | email: lubesorders@total.com.