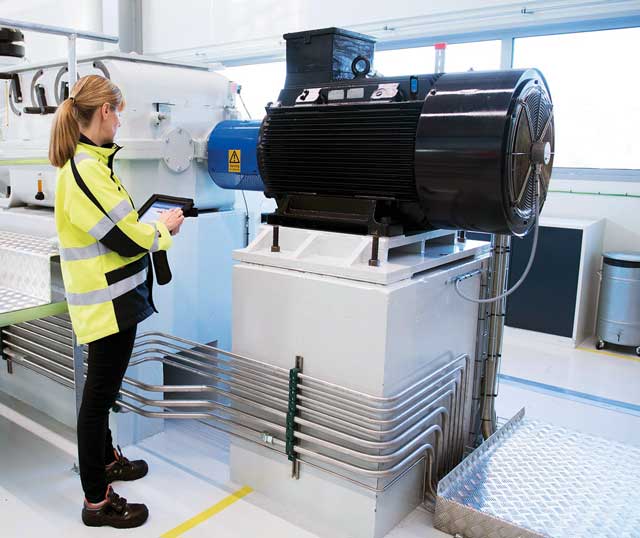
Integration of legacy machinery and new technology, with an initial focus on condition monitoring, can help manufacturers begin the journey toward digitalisation, says SKF service sales manager Gavin Coull.
For most businesses, overnight transformation of their operation from a traditional set-up into a smart factory is not practically or economically possible. The good news is that Industry 4.0 benefits can be achieved without replacing machines.
The important thing is to connect them, and the introduction of digital condition monitoring is a good place to start. This is also surprisingly affordable, given the falling prices of systems and components, and with the right specialist advice it is easy to avoid the wasted expense of overspecification.
For condition monitoring, the current digital revolution is strengthening the economic case for collecting and analysing data to increase machine reliability.
In the current decade, the emergence of the internet of things and cloud computing has taken the potential for condition monitoring to a higher level.
Intelligent manufacturing, supported by advances in connectivity, is drawing maintenance engineering and IT departments closer together. By fitting smart sensors to a factory’s existing equipment to collect comprehensive real-time data, older machines can become part of an intelligent system.
Lower prices
The falling cost of permanently installed data collection systems is partly due to the development of robust, inexpensive sensors. Even more important is the fact that connecting sensors is now cheaper.
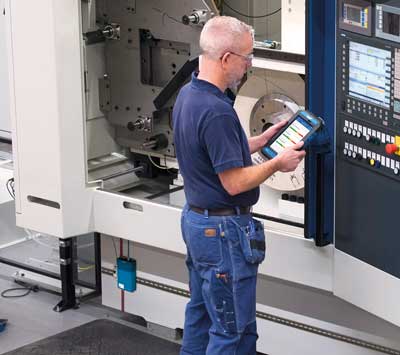
Companies have numerous options to reduce those costs. They can connect data acquisition devices directly to their existing wired networks or they can go wireless. Secure Wi-Fi networks are increasingly common in factories and other industrial plants. A new generation of low-power wireless “mesh” network technologies makes it possible to install sensors that can operate for years on battery power alone.
In addition, new technology is changing the way machine condition data is used. With the internet and cloud computing, data analysis can be centralised or carried out remotely. That can have big benefits for organisations with assets operating around the world. The same technologies make the results of analysis much easier to access.
Specify only what you need
It is important that the sophistication, functionality and cost of condition monitoring systems is appropriate to users’ needs and circumstances. Manufacturers should define what monitoring they need: avoid trying to monitor everything and generating a mass of data with no applicable use.
The purchase, installation and operating cost of each option must be weighed against its advantages. Asset criticality is a key consideration: how expensive the asset is to repair or replace; the potential cost of lost production through downtime; and any safety implications. Investing in higher levels of technology often makes most sense when assets are remote or difficult to access.
Several other practical considerations can be illustrated with reference to the compact, scalable and adaptable SKF Multilog On-line System IMx-8, developed to widen the user base for such systems. It can be wirelessly configured and monitored using mobile devices. In stand-alone mode, with no need for connection to central software or external communications, it will store a year’s worth of machine and event data.
The increasing range of condition monitoring options and prices has opened up the field for predictive maintenance. Now all manufacturers – big or small – have accessible choices for building monitoring regimes into their organisation. Whether by integrating sensors on minor as well as critical machines, or enabling data to be accessed offsite, these small changes are moving businesses toward the smart factory of the future.
For more information, visit www.skf.co.uk,
email marketing.uk@skf.com or call 01582 490049.