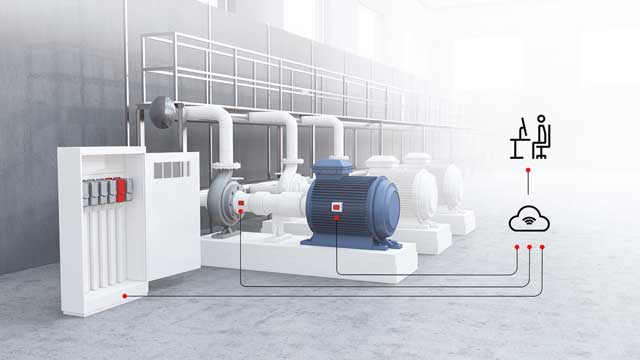
Powertrain technologies now coming on to the market are set to make the life of maintenance and service engineers in industry a great deal easier, while also helping with sustainability, says David Hughes, managing director of ABB UK.
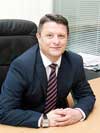
I read with interest the discussion on the pages of the last issue of M&E by the Editorial Advisory Board on the subject of sustainability.
As we head into a new decade, it’s becoming increasingly clear that the impact of human activity is unsustainable, and that urgent action is required on a global scale. It is my view that manufacturing industry has the opportunity to lead the charge on tackling climate change, but it also has the most to gain in reducing operating costs.
Energy efficiency, as the Editorial Advisory Board pointed out, is an area where there is potential to make a huge difference. Variable speed drives (VSDs) have been around for many years, but I find that there is still a relative lack of awareness about their benefits for industrial processes. In fact, it’s thought that up to 90% of all electric motors used in industry are still run without any speed control.
A recent survey by ABB asked financial managers and engineers “What is the single most effective way in which you can save energy at your plant?”.
The top answer was to change energy supplier. Though this might save some money in the short term, it is unlikely to materially reduce energy use, and sooner or later the cost could well go up again.
Another common survey response was to turn off lights. This might help, but still ignores the biggest culprit for energy use.
By far the biggest opportunity lies in tackling the activities that consume the most energy. Electric motors account for almost two-thirds of the electricity consumed by UK industry. A VSD can reduce a motor’s energy costs by up to 60%. If you were to fit one to every single motor in the UK right now, the immediate energy savings would be staggering.
However, it’s not just direct energy savings where VSDs can make a difference. New developments in motor and VSD technology are making it easier than ever to monitor, analyse and improve performance. Smart sensors are one example of such technology. Fitted directly to motors, mechanical transmission components such as bearings, and applications such as pumps, the sensors monitor parameters such as temperature, vibration, noise, energy consumption and bearing index. This can then be aggregated, stored and further accessed via the cloud for data analysis, to reveal information on performance, efficiency and condition.
Rather than having to visually inspect or manually measure equipment, the system draws all the data you could need from across a whole powertrain, whether a single mechanical line-up or an entire process line. It can then present the information to allow users to digitally “see” operational variables and equipment health.
This opens up a range of possibilities for predictive maintenance. The ability to track the status and condition of all the drives, motors, mechanical transmission components and applications in once place can save huge amounts of time. It means that maintenance issues can be flagged up before they turn into failures, preventing downtime while making sure that maintenance is carried out when and where it is needed. Maintenance spending is optimised according to individual equipment needs, so that spares and labour are only used when necessary.
The UK government has pledged to achieve net zero emissions by 2050. Achieving this will be a challenge for everyone. VSDs provide a pathway towards more sustainable operations without requiring large investment or significant behavioural change.
The digital capabilities that modern VSDs now bring for condition and performance monitoring can provide maintenance engineers with the tools they need to ensure that efficiency is improved, without compromising on productivity or profitability.
ABB has launched a website containing videos, leaflets and other resources explaining the uses and benefits of condition monitoring for powertrains. Visit http://bit.ly/2vxHlkO to find out more.