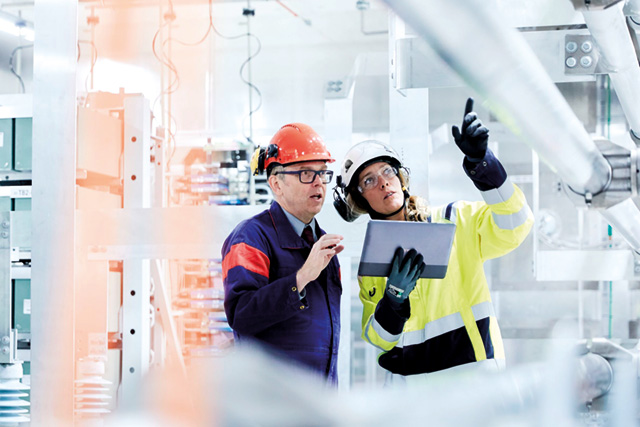
Operating under stringent quality control standards, the food and beverage industry is well used to controlling processes to ensure optimum product quality. Alan Hunt, ABB’s Electromagnetic Flowmeters Product Manager, UK & Ireland, explains why continuous verification software for measuring instruments offers peace of mind to all process owners that instrument readings are correct.
What is verification?
Instrument verification provides online checking of device health and importantly device accuracy. It allows maintenance to be carried out on a predictive rather than reactive basis. Reports from the tool can be used to demonstrate compliance and/or if any faults have been identified and subsequently resolved. Online access to the tool and the data allows anytime, anywhere operation.
Whilst not limited to digital sensors, it is more easily applied to a connected instrument. Where once verification was limited to some flowmeters, in-situ verification can now be applied to a variety of sensors in the measurement range including pressure, flow, temperature, and level.
1. Optimised product quality
By way of example, the food and beverage industry is fastidious about product quality and as such accurate measurement is critical. It is not only an important foundation for building and maintaining customer confidence, the food and beverage industry is also heavily regulated to protect consumer safety and as such having reliable measurement instrumentation can ensure optimised product quality.
Consumer-facing industries are not the only ones affected by the wider trend towards greater reliance on standards. Industries serving other businesses are also increasingly expected to operate within externally recognised standards. In fact, the importance of complying with industrial standards in general has never been greater.
Effective measurement and control practices can be the best defence regardless of the product and verified measurements can ensure that product quality is maintained.
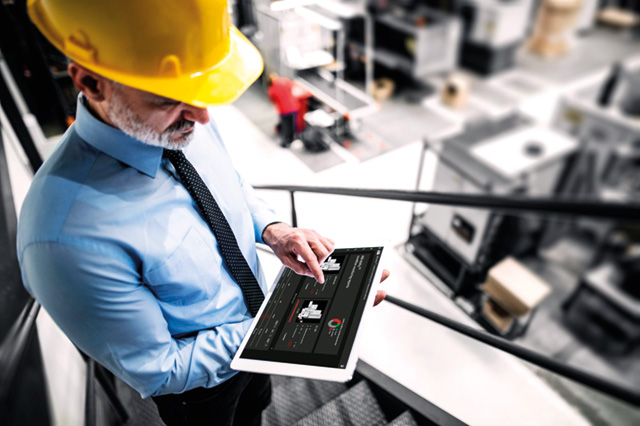
2. Peace of mind
Pioneers of in-situ verification for measurement instruments, ABB developed CalMaster to verify flowmeter accuracy for the water industry. It was a requirement of the Drinking Water Inspectorate (DWI) that measurements were accurate, and the in-situ tool allowed water utilities to report to regulators verified measurement accuracy.
In-situ continuous verification is now available across a variety of process measurement instrumentation, giving process owners further confidence in the continued accuracy of measurements being taken and with that greater control over product quality.
Verification software such as SRV500 software is designed to run continuously and can verify every few minutes if required, to check the circuitry of the sensors, cabling, and electronics, including the outputs. The measurements performed in the field are compared with a baseline set of measurements performed when the product was first manufactured, known as the fingerprint, giving peace of mind to instrumentation specialists and process owners that measurements are accurate.
3. Improved efficiency and reduced maintenance costs
Improving process efficiency whilst maintaining their product quality is at the forefront of the mind of every process owner. One way of achieving optimum process efficiency is to ensure processes remain up and running.
A key benefit of using verification software is that it allows customers to ensure their instruments are measuring properly and are in line with their original settings, but also allows maintenance to be performed on a predictive rather than reactive basis, cutting maintenance costs and the cost of unplanned downtime.
It is important to remember that verification is not calibration and does not provide a certificate in conformance with ISO 17025, however it does provide information to determine if calibration is required saving time and associated costs on calibration at regular intervals whether it is required or not.
The enhanced diagnostic reports available through regular instrument verifications is one way to ensure processes continuously operate at their peak performance reducing instances of unforeseen shutdown of processes.
Furthermore, maintenance requirements can be implemented as and when required rather than at regular intervals, building a more sustainable business practice which can help with reducing costs and reducing waste.
new.abb.com/products/measurement-products/service/advanced-services/SRV500 | enquiries.mp.uk@gb.abb.com | t: 0870 600 6122