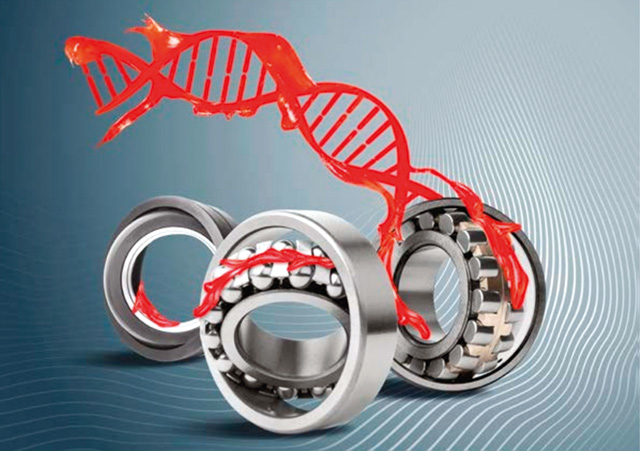
industrial equipment
Manufacturers are increasingly leveraging digital software to plan equipment monitoring and maintenance. This is particularly important when it comes to managing lubricant levels, usage and condition, writes Tom Hyde, Technical Support Manager, TotalEnergies.
Improving efficiency and productivity by keeping machinery working seamlessly and cost-effectively will always be a major consideration for manufacturers.
Factory floors contain a wide range of equipment dealing with numerous functions, and keeping track of what specific monitoring and maintenance they require and when – including effective lubrication – and building processes around those requirements can be complex and challenging.
However, the costs of getting it wrong can be high: from shorter asset lifespans and longer operational downtime to increased health and safety risks.
Many manufacturers are turning to software applications to help them simplify and manage this task.
By logging each individual piece of equipment in a tailored digital platform, along with their specific lubricant requirements and when maintenance should be carried out, planning, oversight and control of the maintenance schedule can be made far easier.
Managers and operational teams can gain greater visibility over what needs to be done, tasks can be assigned and checked off in a timely manner, and a clear audit trail is created.
Having appropriate systems in place is particularly important when it comes to managing lubricant levels, usage and condition. Regular testing of lubricants is essential, in turn helping to ensure that the machinery itself is maintained in peak condition too.
However, there are many different types of lubricant for different purposes, from hydraulic and gear oils to turbine oils and soluble cutting fluids, plus greases, each with different parameters for testing. This includes emerging, sustainable lubricants and fluids.
Some tests can be carried out on-site (for example, concentration and pH of soluble cutting fluids) while others must be analysed by a laboratory, such as testing for viscosity, total acid number (TAN), wear metals and cleanliness.
Having a holistic system in place to flag due dates for analysis, schedule testing, track samples, provide secure access to data and visualise diagnoses and trends over time can deliver real advantages and can form a central plank of a predictive (rather than curative) maintenance strategy.
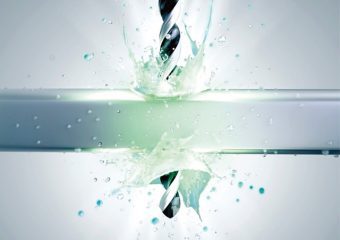
Even better is if this information is connected within the system to other important documents such as technical datasheets, safety guidance, maintenance manuals, internal policies and procedures and contact details for relevant bodies or key staff. And if it can be accessed live ‘on-the-job’ via integrated mobile functionality or has the option to be exported to create insightful reports for management, better still.
Armed with this information, oil drain intervals can be extended, production stoppages (if they are needed at all) can be planned for minimum disruption and maintenance scheduled for the best time to maintain the quality of parts and lubricants while limiting the impact on production.
Clear informational analysis can also assist with making better choices in terms of selecting / changing the lubricant product itself, based on a range of critical indicators including health and safety and environmental impact. For example, by selecting emerging products such as water-based metalworking fluids which have been shown to enhance machining performance, lengthen drain intervals and extend tool lifespans.
By taking a robust, connected approach to monitoring and analysis maintenance costs are kept low and the risk of sudden shutdowns and emergency repairs is minimised. Users of TotalEnergies TIG6 monitoring software have, for example, reported reductions in lubricant costs of up to 4.5% since introduction.
At the same time, this insight can help provide transparency over personnel and other resourcing needs, such as forecasting the volume of supplies that need to be ordered and to which sites, and how they should be applied to reduce waste and optimise consumption.
Just as lubricants are vital to the smooth running of manufacturing machinery and to keep components in tip top condition, so smart software solutions are today proving their worth to ensure that maintenance is timely, effective and properly evidenced.
Streamlining processes where possible and delivering top quality outcomes is core to the economic success of manufacturing – this imperative is equally true for machinery maintenance schedules and operations.
services.totalenergies.uk | ms.marketing@totalenergies.com | t: 01977 238200