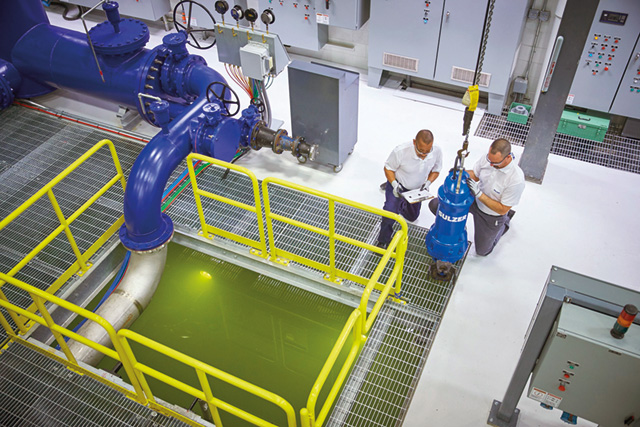
Oliver Minetti, Global Product Manager for Sulzer’s Water division, looks at decisions that affect pump reliability and how to keep maintenance costs to a minimum.
The water and wastewater sectors are reliant on pumps throughout the water cycle and any unplanned downtime or maintenance can have a significant impact on operating costs. The design of pumps, their application and their suggested maintenance schedule are all important factors in overall reliability and cost.
Pumps come in all shapes and sizes, each one specifically designed for its task. If the specification process has been completed correctly, it should deliver efficient service for decades, providing the routine maintenance is followed.
Pump manufacturers make great efforts to offer innovative designs that can handle the challenges of the water industry and keep operating costs to a minimum.
On time decisions
The frequency of maintenance tasks is usually determined by the number of hours operated or a set interval, such as every 12 months. This ensures that pumps operating round-the-clock are kept in optimum condition in the same way as those that work infrequently.
Removing a pump from service after five years or 20,000 hours and transporting it to a workshop for planned maintenance has an inherent cost that needs to be rationalised by the work carried out. If a full inspection is to be completed, it is usually best to replace the mechanical seals and bearings at the same time. This decision may also be affected by the pump’s application and the importance of reliability.
In situations where redundancy is built into the pump application, enabling some assets to be removed without affecting the effectiveness of the remaining pumps, more significant repairs can be completed over a longer time frame.
When a pump failure can quickly cause a location to be inundated, and possibly lead to fines for environmental damage, it is best to pre-empt maintenance intervals and replace service items before their expected service life is reached.
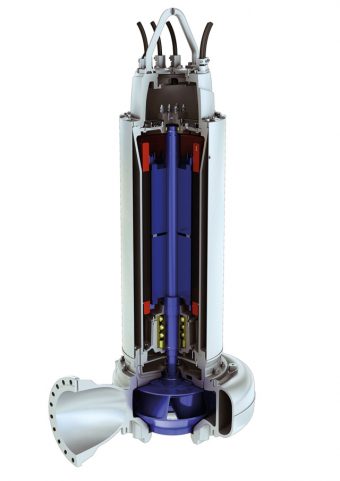
For less critical applications, smaller pumps, less than 10 kW, may often be left to operate until they fail because the expense of removing and repairing them is outweighed by the cost of a new pump.
In these situations, investing in high-quality, high-efficiency pumps will offer the most costeffective solution in the long-term. Pumps that offer excellent reliability through their inherent design and optimum energy consumption by using Premium Efficiency motors, provide the most cost effective solution over the lifetime of the pump.
Tackling the problems
One of the major challenges in the wastewater industry has been the huge increase in wipes entering the sewerage system. These wipes can cause major blockages, especially in pumping stations that are not equipped with any kind of screen.
Blocked pumps need to be cleared at the earliest opportunity, but this usually requires a maintenance team to be dispatched to the site, increasing costs and the carbon footprint of the business.
To counter this trend, pump manufacturers have designed new types of impeller for assets that are used in pumping stations. For example, Sulzer’s Contrablock Plus impeller has been proven in many situations to have greatly improved reliability in situations that previously had seen call-outs on a weekly or even daily basis.
The ability to reset the gap between impeller and bottom plate ensures continued efficiency and performance.
By taking advantage of engineering developments and combining the manufacturer’s guidelines with an application risk assessment, it is possible to determine the most effective maintenance routine for each pump in the network.